3LPE / 3LPP Coated Pipe
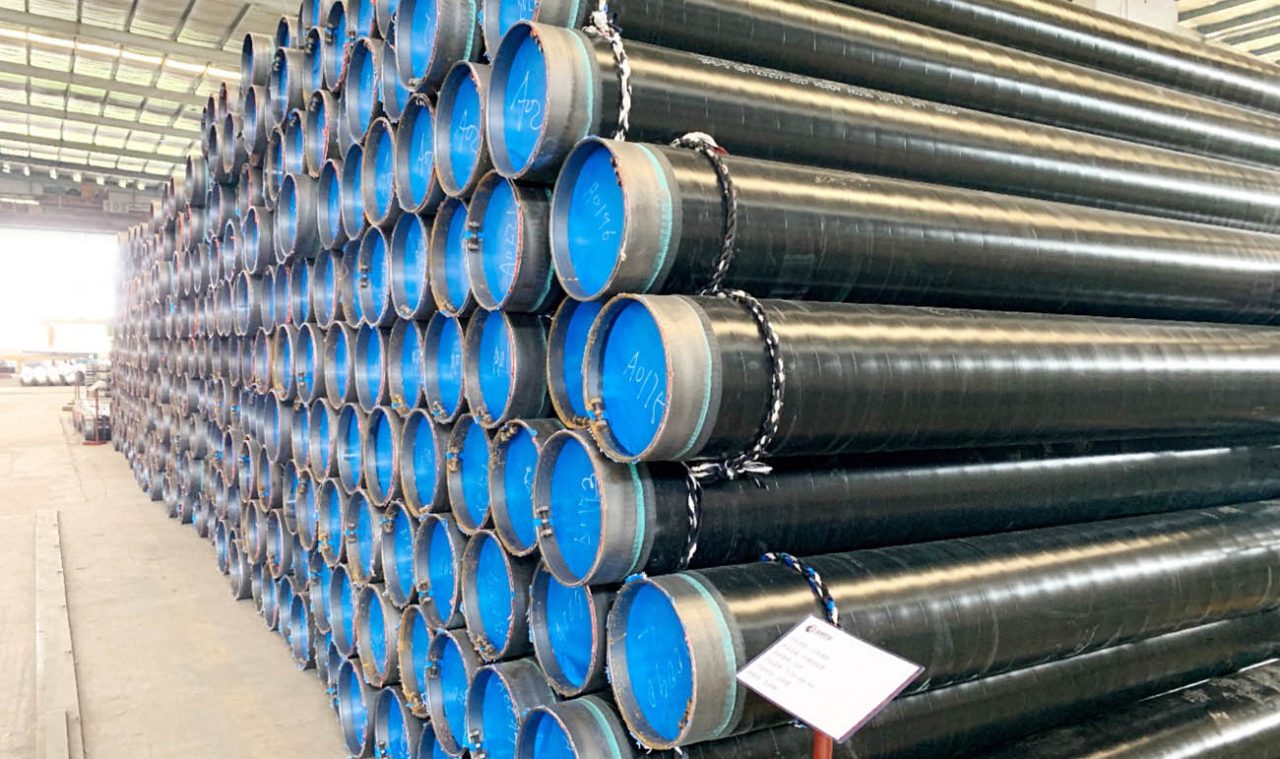
3LPE / 3LPP Coated Pipe Overview
3LPE (Three-Layer Polyethylene) and 3LPP (Three-Layer Polypropylene) coatings are advanced pipe coating technologies used to protect steel pipes from corrosion, mechanical damage, and other environmental factors. These coatings are widely used in various industries, including oil and gas, water supply, and chemical processing.
Structure of 3LPE and 3LPP Coatings
Both 3LPE and 3LPP coatings consist of three layers:
- First Layer (Fusion Bonded Epoxy – FBE)
- This layer offers excellent adhesion to the steel pipe and provides primary corrosion protection.
- The FBE layer is applied by spraying melted epoxy powder onto the pre-heated pipe surface, which then fuses and cures.
- Second Layer (Adhesive)
- This layer is typically a copolymer adhesive that bonds the FBE layer to the outer layer.
- It ensures strong adhesion between the FBE and the outer polyethylene or polypropylene layer.
- Third Layer (Polyethylene for 3LPE / Polypropylene for 3LPP)
- The outermost layer provides mechanical protection against impacts, abrasions, and other physical damages.
- Polyethylene is used in 3LPE coatings, while polypropylene is used in 3LPP coatings, each offering different properties suited to specific conditions.
Specification
Nominal Diameter of Steel Pipe(DN) | Epoxy Coating | Adhesive Layer | Min Thickness of Anti-Corrosion Layer (mm) | |
(mm) | (a/μm) | (mm)/um | General Type | Strengthen Type |
DN≤100 | ≥120 | ≥170 | 1.8 | 2.5 |
100<dn≤250< p=””></dn≤250<> | / | / | 2 | 2.7 |
250<dn<500< p=””></dn<500<> | / | / | 2.2 | 2.9 |
500≤DN<800 | / | / | 2.5 | 3.2 |
DN≥800 | / | / | 3 | 3.7 |
3LPE and 3LPP coating steel pipe Specification
Coating materials | Characteristics |
PE/PP compound layer | High density PE (Containing 2~3% furance black and small amount of antioxidant) Stabilized PP |
PE/PP adhesive layer | Same as above |
Primer layer | Liquid epoxy or fusion bond epoxy power |
The Three Layer Polyethylene (3LPE) system is applied to pipelines operating at temperatures ranging from -40 to +80ºC. The Three Layer Polypropylene (3LPP) system is applied to pipelines operating at temperatures ranging from -20 to +110ºC. Typically the two systems have a thickness ranging from 1.5 to 3mm.
The 3LPE and 3LPP external coating plant is equipped to coat pipes with a nominal diameter ranging from 2” to 48”, and lengths ranging from 8m to 18m.
The standard layer thickness is minimum 2.5mm or 3/5mm but this value can be changed upon customers’ request.
Production Process
The pipes are first cleaned and heated. Then the powder epoxy is applied, forming the first layer of the system. This is followed by the application of a copolymeric adhesive via lateral extrusion to provide the adherence necessary between the primer and the third system layer. Finally, a polyolefin (Polyethylene or Polypropylene) is applied, also via lateral extrusion, completing the three layer system. This system is suitable for underground gas and oil pipelines and underwater installations.
Production equipment of 3LPE and 3LPP coating steel pipe
Process
3LPE Coated Pipe Manufacturing Equipment
Packing
Key Features of 3LPE / 3LPP Coated Pipes
- Corrosion Resistance:
- The FBE layer provides exceptional corrosion resistance, preventing the steel pipe from rusting and extending its lifespan.
- Mechanical Protection:
- The outer polyethylene or polypropylene layer offers robust protection against physical damage, ensuring the pipe can withstand harsh handling and installation conditions.
- Adhesion:
- The adhesive layer ensures excellent bonding between the inner FBE layer and the outer polyethylene or polypropylene layer, maintaining coating integrity.
- Chemical Resistance:
- Both 3LPE and 3LPP coatings provide strong resistance to chemicals, making them suitable for pipelines transporting corrosive substances.
- Temperature Range:
- 3LPE: Suitable for moderate temperature ranges, typically up to 80°C.
- 3LPP: Can withstand higher temperatures, usually up to 110°C, making it ideal for pipelines in hotter environments.
Comparison of various coating systems
Property | CTE coating | FBE Coating | 3LPE Coating | |||
---|---|---|---|---|---|---|
Service temperature : | 45 oC | 110 oC | 80 oC | |||
Impact resistance : | Poor | High | Excellent | |||
Penetration resistance : | Initially good but changes to poor with passage of time | High | Excellent (No changes observed during service life) | |||
Damages during handling & transportation : | High | High | Low | |||
Cathodic disbondment : | Good | Very good | Good | |||
Resistance to soil stress : | Poor | Good | Excellent | |||
Resistance to water and oxygen permeation : | Good (initially) | Good | Excellent | |||
Chemical resistance : | Good | Very good | Very good | |||
Volume resistivity : | Good | Excellent | Excellent | |||
Bending flexibility : | No flexibility | 1.5 oppd length | 2.0 oppd length | |||
Hardness : | Less | Excellent | Excellent | |||
Requirement for maintenance and refurbishment frequency of coating/ CP system : | High | High | Low | |||
Impact on human health : | Highly injurious | Less injurious | Less injurious | |||
Environmental impact : | Highly polluting | Less polluting | Less polluting | |||
Cathodic protection current demand (design) : | 0.3 – 1.0 mA/ m2 | 0.3 – 1.0 mA/ m2 | 0.05 – 0.1 mA/ m2 | |||
Resistance to peel : | Fair | — | Excellent | |||
Distance between CP stations : | 20 km – 25 km | 20 km – 25 km | 40 km – 45 km |
Applications
3LPE and 3LPP coated pipes are used in various applications, including:
- Oil and Gas Industry:
- Transportation of crude oil, natural gas, and refined petroleum products.
- Water Supply Systems:
- Long-distance water pipelines for potable and industrial water.
- Chemical Processing:
- Pipelines carrying corrosive chemicals and materials.
- Infrastructure Projects:
- Used in construction projects requiring durable and long-lasting pipeline solutions.
Conclusion
3LPE and 3LPP coated pipes provide superior protection against corrosion and physical damage, making them ideal for a wide range of industrial applications. The combination of fusion bonded epoxy, adhesive, and polyethylene or polypropylene layers ensures long-lasting performance and reliability. By selecting the appropriate coating (3LPE for moderate temperatures and 3LPP for higher temperatures), industries can ensure optimal protection and longevity of their pipeline systems.