Alloy Steel 602 CA (2.4633, N06025) Pipe
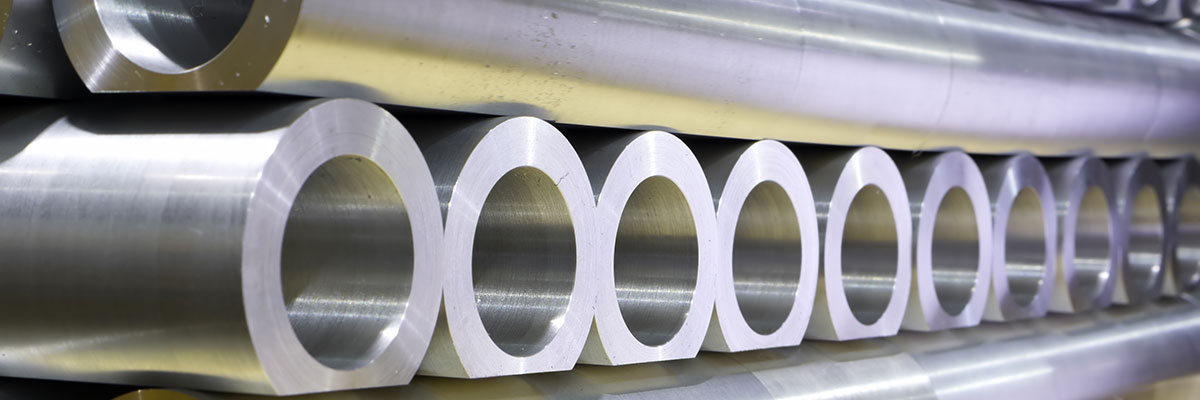
Alloy 602 CA (2.4633, N06025) Alloy Steel Pipe – Comprehensive Overview
Alloy 602 CA, also known by its material number 2.4633 and UNS designation N06025, is a high-performance nickel-chromium-iron alloy designed for extreme environments. This alloy is widely recognized for its exceptional resistance to oxidation and corrosion at high temperatures, making it a preferred material in industries requiring durability under thermal stress. Below, we provide an in-depth exploration of its standards, description, special properties, chemical composition, mechanical properties, physical properties, suitable welding filler materials, applications, and available forms.
Standards for Alloy 602 CA (2.4633, N06025)
Alloy 602 CA complies with various international standards that define its composition, properties, and manufacturing processes. These standards ensure consistency and quality across applications.
Standard | Description |
---|---|
DIN EN 10302 | Specifies creep-resisting steels, nickel, and cobalt alloys, including Alloy 602 CA, for high-temperature applications. |
ASTM B167 | Covers nickel-chromium-iron alloys (UNS N06600, N06601, N06603, N06025, etc.) in seamless pipe and tube forms. |
ASTM B168 | Addresses nickel-chromium-iron alloys in plate, sheet, and strip forms, applicable to Alloy 602 CA components. |
ASME SB-167 | ASME specification for seamless nickel alloy pipes, including N06025, for high-temperature service. |
ISO 6207 | International standard for seamless nickel and nickel alloy tubes, including Alloy 602 CA. |
These standards ensure that Alloy 602 CA meets rigorous requirements for chemical composition, mechanical performance, and dimensional tolerances, making it suitable for critical applications in industries such as chemical processing, power generation, and automotive engineering.
Description of Alloy 602 CA
Alloy 602 CA (2.4633, N06025) is a high-carbon nickel-chromium-iron alloy fortified with microalloying elements such as aluminum, yttrium, titanium, and zirconium. This alloy belongs to the family of heat-resistant nickel-based superalloys, engineered to perform in environments where temperatures exceed 1000°C (1832°F). Its high chromium content, combined with aluminum and yttrium, forms a protective oxide layer that enhances its durability in oxidizing and carburizing conditions.
The alloy’s exceptional creep strength and resistance to thermal cycling make it ideal for prolonged exposure to extreme heat. It is commonly supplied in a solution-annealed condition with an oxidized or descaled surface, ensuring optimal performance in high-temperature settings. Alloy 602 CA stands out among nickel alloys for its ability to maintain structural integrity and resist degradation in harsh chemical and thermal environments.
Special Properties of Alloy 602 CA
Alloy 602 CA exhibits a unique combination of properties that distinguish it from other materials in its class. These properties contribute to its widespread use in demanding applications.
Property | Description |
---|---|
Outstanding Oxidation Resistance | Resists oxidation at temperatures up to 1200°C (2192°F), even under cyclic conditions, due to a dense chromium oxide and aluminum oxide layer. |
Carburization Resistance | Excellent performance in carburizing environments, preventing carbon absorption that could compromise ductility. |
High-Temperature Creep Strength | Maintains structural integrity under prolonged stress at elevated temperatures, ideal for furnace components. |
Corrosion Resistance | Resilient in oxidizing, reducing, and chlorinating media, including metal dusting conditions. |
Thermal Stability | Retains mechanical properties during thermal cycling, reducing the risk of cracking or deformation. |
These special properties make Alloy 602 CA a top choice for applications where reliability under extreme conditions is paramount. Its ability to form a self-repairing oxide scale, enhanced by yttrium, ensures long-term performance with minimal maintenance.
Chemical Composition of Alloy 602 CA
The chemical composition of Alloy 602 CA is carefully controlled to achieve its remarkable properties. The following table lists the typical composition ranges for its key elements.
Element | Composition Range (%) |
---|---|
Nickel (Ni) | Balance (approximately 60-63%) |
Chromium (Cr) | 24.0 – 26.0 |
Iron (Fe) | 8.0 – 11.0 |
Carbon (C) | 0.15 – 0.25 |
Aluminum (Al) | 1.8 – 2.4 |
Yttrium (Y) | 0.05 – 0.12 |
Titanium (Ti) | 0.10 – 0.20 |
Zirconium (Zr) | 0.01 – 0.10 |
Silicon (Si) | ≤ 0.50 |
Manganese (Mn) | ≤ 0.50 |
Phosphorus (P) | ≤ 0.02 |
Sulfur (S) | ≤ 0.01 |
Copper (Cu) | ≤ 0.10 |
The high nickel content provides a stable matrix, while chromium and aluminum enhance oxidation resistance. Yttrium improves oxide scale adhesion, and the elevated carbon content contributes to creep strength. Trace elements like titanium and zirconium refine the grain structure, further boosting high-temperature performance.
Mechanical Properties of Alloy 602 CA
The mechanical properties of Alloy 602 CA are optimized for high-temperature service. These values are typically measured at room temperature unless otherwise specified.
Property | Value |
---|---|
0.2% Yield Strength (Rp) | ≥ 270 N/mm² |
Tensile Strength (Rm) | ≥ 670 N/mm² |
Elongation (A5) | ≥ 30% |
Modulus of Elasticity | 215 kN/mm² |
Hardness (Brinell, HB) | Approx. 150-200 HB |
At elevated temperatures, Alloy 602 CA maintains significant strength and ductility. Its creep resistance is particularly notable, with the alloy capable of withstanding prolonged stress without significant deformation. These properties are critical for components like pipes and furnace parts operating in continuous high-temperature environments.
Physical Properties of Alloy 602 CA
The physical properties of Alloy 602 CA support its use in high-temperature and corrosive conditions. These properties remain stable across a wide temperature range.
Property | Value |
---|---|
Density | 7.9 g/cm³ |
Specific Heat Capacity | 450 J/kg·K |
Thermal Conductivity | 11.3 W/m·K |
Electrical Resistivity | 1.15 Ω·mm²/m |
Melting Range | 1340 – 1390°C (2444 – 2534°F) |
The relatively low thermal conductivity and high electrical resistivity reflect Alloy 602 CA’s suitability for heat-resistant applications. Its density is typical of nickel-based alloys, providing a balance of strength and weight for structural components.
Suitable Welding Filler Materials for Alloy 602 CA
Welding Alloy 602 CA requires careful selection of filler materials to maintain its properties. The following table lists suitable options.
Filler Material | Standard | Description |
---|---|---|
2.4649 | DIN EN ISO 18274: S Ni 6025 | Nickel-based filler matching Alloy 602 CA’s composition for high-temperature strength. |
ENiCrFe-12 | AWS A5.11 | Electrode for shielded metal arc welding, offering good corrosion resistance. |
ERNiCr-4 | AWS A5.14 | Filler wire for TIG/MIG welding, compatible with Alloy 602 CA’s chemistry. |
Welding methods such as TIG (Tungsten Inert Gas), MIG/MAG (Metal Inert Gas/Metal Active Gas), and manual electric welding are suitable. Preheating is typically not required, but post-weld heat treatment is recommended for components used between 600-750°C to relieve stresses and enhance stability.
Applications of Alloy 602 CA
Alloy 602 CA is employed in a variety of industries due to its robust performance under extreme conditions. The following table highlights key applications.
Industry | Application |
---|---|
Chemical Processing | Reformers, hydrogen production units, methanol and ammonia synthesis equipment. |
Power Generation | Radiant tubes, furnace muffles, kiln rollers in heat treatment furnaces. |
Automotive | Exhaust system components, glow plugs for diesel engines. |
Petrochemical | Components exposed to carburizing and oxidizing atmospheres. |
Waste Management | Glass pots for melting radioactive waste. |
These applications leverage Alloy 602 CA’s ability to withstand high temperatures, resist corrosion, and maintain mechanical strength, ensuring safety and efficiency in critical operations.
Available Forms for Alloy 602 CA (2.4633, N06025)
Alloy 602 CA is available in various forms to suit different manufacturing and application needs. The following table lists common forms.
Form | Description |
---|---|
Seamless Pipes | Used in high-pressure, high-temperature systems; complies with ASTM B167. |
Welded Pipes | Suitable for larger diameters and less critical pressure applications. |
Sheets and Plates | Available in superformats (e.g., 2000×6000 mm); per ASTM B168. |
Rods and Bars | For forging or machining into components; per DIN 17752. |
Forgings | Custom shapes like rings, blanks, and flanges for specialized parts. |
Tubes | Seamless or welded for heat exchangers and piping systems. |
Fittings | Elbows, tees, reducers for piping assemblies. |
These forms can be customized through cutting (e.g., plasma or water jet) to meet specific dimensional requirements, enhancing Alloy 602 CA’s versatility in industrial applications.
Extended Discussion on Alloy 602 CA
To fully appreciate Alloy 602 CA, it’s worth exploring its development and performance in greater detail. This alloy was engineered to address the limitations of earlier nickel alloys in extreme environments. Traditional materials often succumbed to oxidation, creep, or carburization at high temperatures, leading to frequent maintenance or replacement. Alloy 602 CA overcomes these challenges through its sophisticated alloying strategy.
The high chromium content (24-26%) forms a protective Cr₂O₃ layer, which is further stabilized by aluminum (1.8-2.4%) creating an Al₂O₃ subscale. Yttrium (0.05-0.12%) enhances the adhesion of these oxide layers, preventing spalling during thermal cycling. This synergy results in an alloy that can operate at temperatures exceeding 1200°C without significant degradation, a feat few materials can achieve.
In terms of mechanical performance, the elevated carbon content (0.15-0.25%) contributes to precipitation strengthening, improving creep resistance. This is critical for applications like furnace muffles or radiant tubes, where components are under constant load at high temperatures. The addition of titanium and zirconium refines the grain structure, reducing the risk of grain coarsening and maintaining strength over time.
The alloy’s corrosion resistance extends beyond oxidation to include carburizing and chlorinating environments. In petrochemical reformers, for instance, Alloy 602 CA resists carbon uptake that could embrittle lesser materials. Its performance in metal dusting conditions—where carbon-rich gases degrade metal surfaces—further underscores its suitability for harsh industrial processes.
Welding Alloy 602 CA requires attention to detail. The recommended filler materials, such as 2.4649 or ENiCrFe-12, match its composition to ensure weld integrity. Techniques like TIG welding provide precise control, minimizing heat-affected zone issues. For components operating in the 600-750°C range, post-weld heat treatment stabilizes the microstructure, preventing sensitization or cracking.
In practical applications, Alloy 602 CA shines in scenarios demanding longevity and reliability. In power plants, radiant tubes made from this alloy withstand the intense heat of combustion gases, while in automotive exhaust systems, it resists thermal fatigue and corrosive exhaust gases. Its use in hydrogen production units highlights its ability to handle reducing atmospheres, a testament to its versatility.
The available forms of Alloy 602 CA—pipes, sheets, bars, and more—cater to diverse manufacturing needs. Seamless pipes, for example, are ideal for high-pressure systems, while sheets can be formed into complex shapes for furnace linings. The ability to customize these forms through cutting or forging enhances its adaptability, making it a go-to material for engineers designing for extreme conditions.
Looking forward, Alloy 602 CA’s role in emerging technologies, such as advanced nuclear reactors or renewable energy systems, could expand. Its ability to handle high temperatures and corrosive environments aligns with the needs of next-generation energy infrastructure. As industries push the boundaries of performance, this alloy remains a reliable foundation for innovation.