LSAW Steel Pipe (Longitudinally Submerged Arc Welding Pipe)
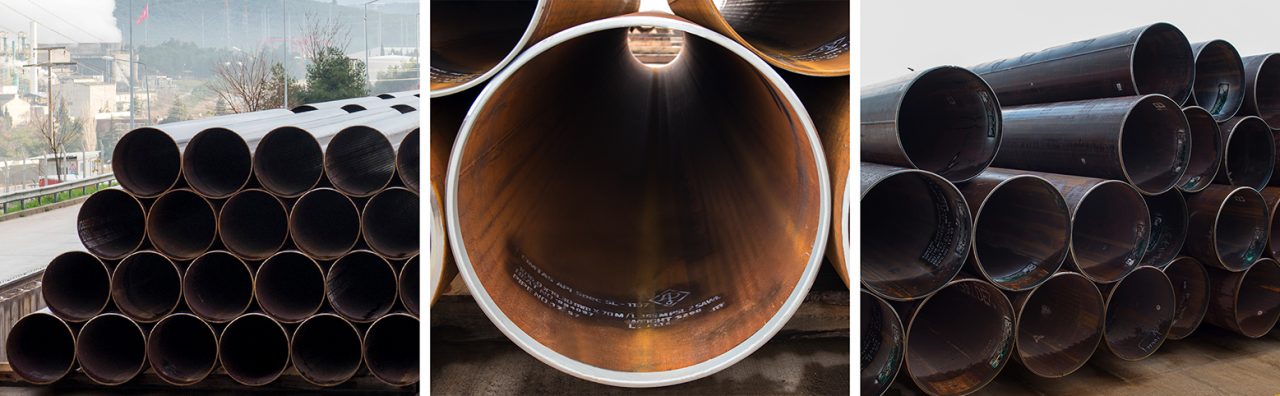
LSAW Steel Pipe (Longitudinally Submerged Arc Welding Pipe)
UOE SAWL PIPES
Outside Diameter:Φ508mm- 1118mm (20″- 44″)
Wall Thickness: 6.0-25.4mm 1/4″-1″
Quality Standards: API、DNV、ISO、DEP、EN、ASTM、DIN、BS、JIS、GB、CSA
Length: 9-12.3m (30′- 40′)
Grades: API 5L A-X90,GB/T9711 L190-L625
JCOE SAWL PIPES
Outside Diameter:Φ406mm- 1626mm (16″ – 64″ )
Wall Thickness:6.0- 75mm (1/4″ – 3″ )
Quality Standards:API、DNV、ISO、DEP、EN、ASTM、DIN、BS、JIS、GB、CSA
Length:3-12.5m ( 10′- 41′ )
Grades:API 5L A-X100, GB/T9711 L190-L690
LSAW PIPE APPLICATIONS
CIVIL CONSTRUCTION:
Structural pipes for stadiums, bridges and buildings.
SPECIAL ITEMS:
Mother pipes for bends, pipes for slug catcher facilities (including HIC & SSC). Prefabricated tubular elements ready to be assembled at the construction yard.
ONSHORE PLANTS:
Pipes processed for the petrochemical industry, oil and gas treatments plants, power plants and reactors, oil and gas refineries, and LNG terminals.
OFFSHORE STRUCTURES:
Pipes, piles, cans and cones for offshore platform jackets. Topsides and foundation jackets for wind farms.
Longitudinally welded steel pipes are used in onshore and offshore oil and gas pipelines requiring critical service, high performance and tight tolerances. LSAW pipe are also used in conveyance of flammable & nonflammable liquids, and as structural members in construction projects.
Tolerance of Outside Diameter and Wall Thickness
Types | Standard | |||||
SY/T5040-2000 | SY/T5037-2000 | SY/T9711.1-1977 | ASTM A252 | AWWA C200-97 | API 5L PSL1 | |
Tube end OD deviation | ±0.5%D | ±0.5%D | -0.79mm~+2.38mm | <±0.1%T | <±0.1%T | ±1.6mm |
Wall thickness | ±10.0%T | D<508mm, ±12.5%T | -8%T~+19.5%T | <-12.5%T | -8%T~+19.5%T | 5.0mm<t<15.0mm, ±0.11<=”” p=””></t<15.0mm,> |
D>508mm, ±10.0%T | T≥15.0mm, ±1.5mm |
Chemical Composition and Mechanical Properties of LSAW Steel Pipe
Standard | Grade | Chemical Composition(max)% | Mechanical Properties(min) | |||||
C | Mn | Si | S | P | Yield Strength
(Mpa) |
Tensile Strength
(Mpa) |
||
GB/T700-2006 | A | 0.22 | 1.4 | 0.35 | 0.050 | 0.045 | 235 | 370 |
B | 0.2 | 1.4 | 0.35 | 0.045 | 0.045 | 235 | 370 | |
C | 0.17 | 1.4 | 0.35 | 0.040 | 0.040 | 235 | 370 | |
D | 0.17 | 1.4 | 0.35 | 0.035 | 0.035 | 235 | 370 | |
GB/T1591-2009 | A | 0.2 | 1.7 | 0.5 | 0.035 | 0.035 | 345 | 470 |
B | 0.2 | 1.7 | 0.5 | 0.030 | 0.030 | 345 | 470 | |
C | 0.2 | 1.7 | 0.5 | 0.030 | 0.030 | 345 | 470 | |
BS En10025 | S235JR | 0.17 | 1.4 | – | 0.035 | 0.035 | 235 | 360 |
S275JR | 0.21 | 1.5 | – | 0.035 | 0.035 | 275 | 410 | |
S355JR | 0.24 | 1.6 | – | 0.035 | 0.035 | 355 | 470 | |
DIN 17100 | ST37-2 | 0.2 | – | – | 0.050 | 0.050 | 225 | 340 |
ST44-2 | 0.21 | – | – | 0.050 | 0.050 | 265 | 410 | |
ST52-3 | 0.2 | 1.6 | 0.55 | 0.040 | 0.040 | 345 | 490 | |
JIS G3101 | SS400 | – | – | – | 0.050 | 0.050 | 235 | 400 |
SS490 | – | – | – | 0.050 | 0.050 | 275 | 490 | |
API 5L PSL1 | A | 0.22 | 0.9 | – | 0.03 | 0.03 | 210 | 335 |
B | 0.26 | 1.2 | – | 0.03 | 0.03 | 245 | 415 | |
X42 | 0.26 | 1.3 | – | 0.03 | 0.03 | 290 | 415 | |
X46 | 0.26 | 1.4 | – | 0.03 | 0.03 | 320 | 435 | |
X52 | 0.26 | 1.4 | – | 0.03 | 0.03 | 360 | 460 | |
X56 | 0.26 | 1.1 | – | 0.03 | 0.03 | 390 | 490 | |
X60 | 0.26 | 1.4 | – | 0.03 | 0.03 | 415 | 520 | |
X65 | 0.26 | 1.45 | – | 0.03 | 0.03 | 450 | 535 | |
X70 | 0.26 | 1.65 | – | 0.03 | 0.03 | 585 | 570 |
lSAW ( Welded Pipes )Manufacturing Process
UOE is a method used for production of longitudinally welded large diameter pipes. Longitudinal edges of steel plates are first beveled using carbide milling equipment. Beveled plates are then formed into a U shape using a U-press and subsequently into an O shape using an O-press.
Longitudinal edges of the plates are then tack welded followed by internal and external welds.
Pipes manufactured by this process are subjected to expanding operation in order to relieve internal stresses and obtain a perfect dimensional tolerance.
After the pipes are conveyed to cold expansion, hydrostatic testing and NDT inspection, the pipes will be subject to final inspection for the compliance to customer requirements.
Starting from incoming control up to the final inspection stage; entire process is monitored and supported by computerized system. Traceability is achieved by input controls and barcodes through entire production lines.
Production Flow
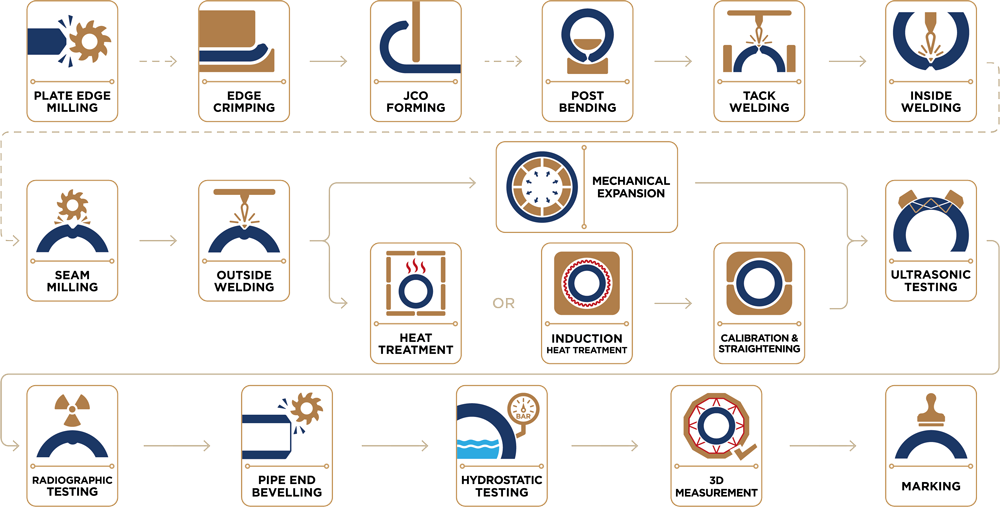
Production Range
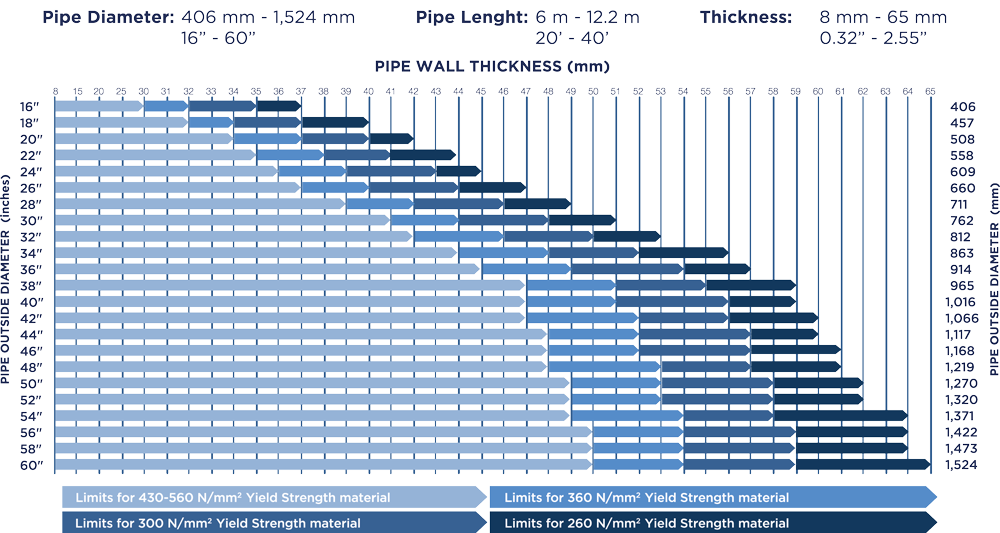
- Pipe Diameter : 406 mm – 1,524 mm (16” – 60”)
- Pipe Length : 6 m – 12.2 m (20” – 40”)
- Thickness : 8 mm – 65 mm (0.32″ – 2.55″)
COMPANY EQUIPMENT VIEW
Oxy – Plasma cutting machines
Pre bending machine
Press bending machine
Roll bending machine
Tack welding machine
Internal LSAW machines
Milling machine
External LSAW machines
Welding portals
Grinding machine
Sizing press
Post welding heat treatment
End bevelling machines
Pipe cutting machines
AutomaticUT
Bunker RX
Hydrotest machine
Automatic dimensional inspection