EN 10219 Welded steel pipe | 10219 LSAW & DSAW
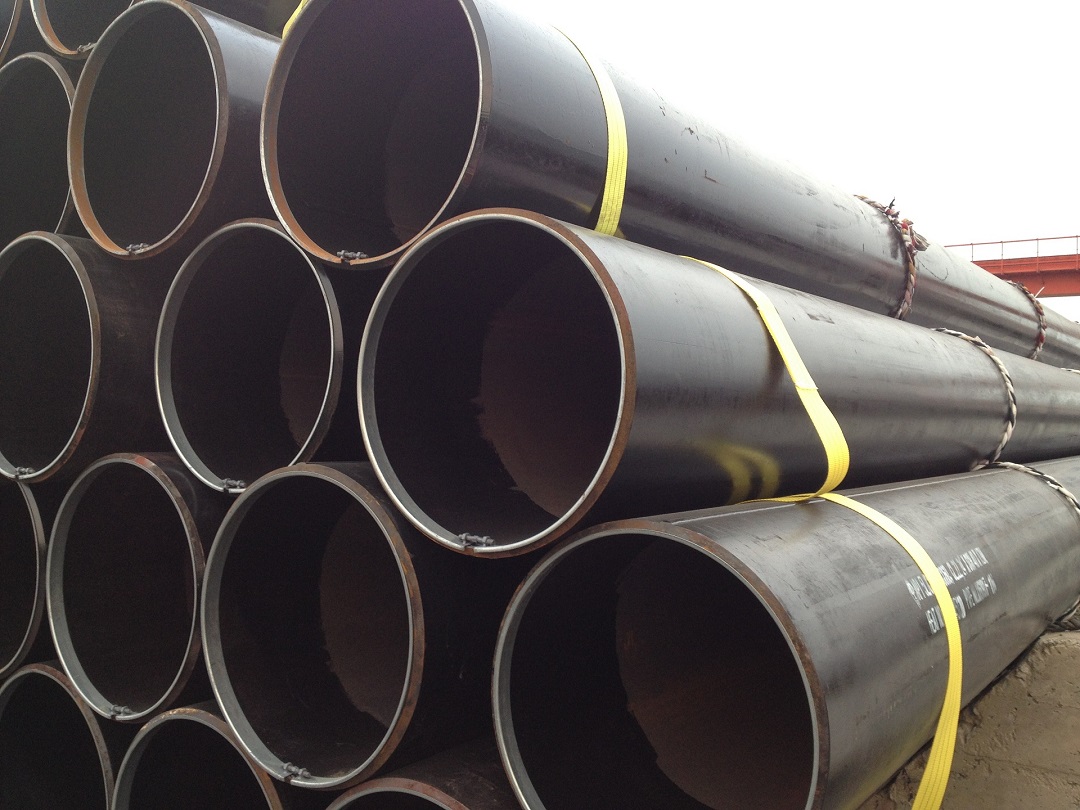
EN 10219 LSAW & DSAW Steel Pipe
EN 10219 is a European standard that specifies the technical delivery conditions for cold-formed welded structural hollow sections of non-alloy and fine grain steels. LSAW (Longitudinal Submerged Arc Welded) and DSAW (Double Submerged Arc Welded) steel pipes produced according to this standard are used in various structural and engineering applications.
Key Features
-
- Standard: EN 10219
- Types:
- LSAW (Longitudinal Submerged Arc Welded)
- DSAW (Double Submerged Arc Welded)
- Grades:
- S235JRH
- S275J0H
- S275J2H
- S355J0H
- S355J2H
- Sizes:
- Outside Diameter: 12” to 64” (304.8 mm to 1625.6 mm)
- Wall Thickness: 0.109” to 2.5” (2.77 mm to 63.5 mm)
- Lengths: Standard or custom lengths as per project requirements
Chemical Composition
Grade | Carbon (C) % (max) | Manganese (Mn) % (max) | Phosphorus (P) % (max) | Sulfur (S) % (max) | Silicon (Si) % (max) |
---|---|---|---|---|---|
S235JRH | 0.17 | 1.40 | 0.035 | 0.030 | 0.50 |
S275J0H | 0.20 | 1.50 | 0.035 | 0.030 | 0.50 |
S275J2H | 0.20 | 1.50 | 0.035 | 0.030 | 0.50 |
S355J0H | 0.22 | 1.60 | 0.035 | 0.030 | 0.50 |
S355J2H | 0.22 | 1.60 | 0.035 | 0.030 | 0.50 |
Mechanical Properties
Grade | Yield Strength (min) | Tensile Strength (min) | Elongation (min) |
---|---|---|---|
S235JRH | 235 MPa | 360-510 MPa | 24% |
S275J0H | 275 MPa | 370-530 MPa | 23% |
S275J2H | 275 MPa | 370-530 MPa | 23% |
S355J0H | 355 MPa | 470-630 MPa | 22% |
S355J2H | 355 MPa | 470-630 MPa | 22% |
LSAW Manufacturing Process
- Plate Selection: High-quality steel plates chosen according to EN 10219 requirements.
- Edge Preparation: Edges of the steel plates are beveled to create a V-shaped groove.
- Forming: Steel plates are formed into cylindrical shapes using press or roll bending machines.
- Tack Welding: Formed plates are tack-welded to maintain the shape.
- Submerged Arc Welding: Longitudinal seam is welded using submerged arc welding both internally and externally.
- Heat Treatment: Welded pipe may undergo heat treatment to relieve stress and improve properties.
- Inspection: Pipes undergo non-destructive tests such as ultrasonic testing and radiographic testing.
- Finishing: Final processes include end beveling, coating, and marking.
DSAW Manufacturing Process
- Plate Selection: High-quality steel plates chosen according to EN 10219 requirements.
- Edge Preparation: Edges of the rolled plate are prepared to create V-shaped grooves.
- Forming: Plates are formed into cylindrical shapes using press or roll bending machines.
- Tack Welding: Formed plates are tack-welded to maintain the shape.
- Double Submerged Arc Welding: Pipe seam welded with an arc welder on both interior and exterior surfaces using submerged arc welding.
- Ultrasonic Inspection: Seam inspected by continuous ultrasonic automatic flaw detection.
- Cutting: Pipes cut into individual pieces.
- Hydrostatic Pressure Test: Each pipe undergoes hydrostatic pressure testing to ensure it can withstand the specified pressure.
- Finishing: Final processes include end processing, beveling, coating, and marking according to customer specifications.
Applications
- Structural Engineering: Used in construction of buildings, bridges, and other structures requiring high strength and durability.
- Piling Foundations: Employed as steel pipe piles in foundation construction for buildings and infrastructure projects.
- Mechanical Applications: Suitable for various mechanical and engineering applications, including machinery and equipment frames.
- Infrastructure: Utilized in the construction of pipelines, towers, and other infrastructure projects.
Advantages
- High Strength: Capable of withstanding high pressure and stress, making them suitable for heavy-duty applications.
- Dimensional Accuracy: Offers precise control over pipe dimensions, ensuring consistent quality.
- Strong Weld Integrity: Both LSAW and DSAW processes provide robust and reliable weld seams.
- Versatility: Suitable for a wide range of applications and environments, including harsh conditions.
- Quality Assurance: Extensive testing ensures compliance with EN 10219 standards and high-quality output.