Nickel 201 Steel Tube (UNS N02201)
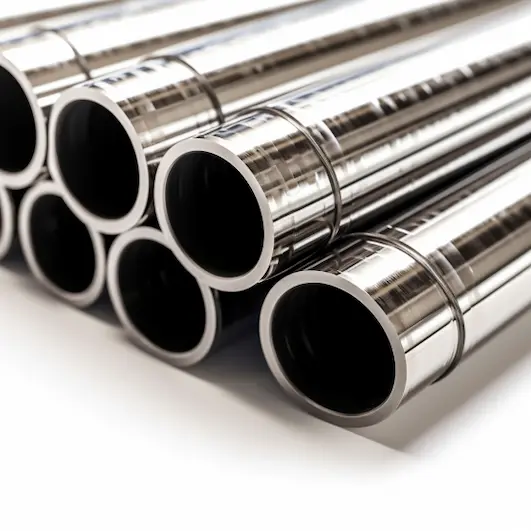
Nickel 201 Steel Tube (UNS N02201)
Nickel 201, also known as UNS N02201, is a commercially pure wrought nickel with properties similar to Nickel 200 but with a lower carbon content. This lower carbon content makes Nickel 201 less susceptible to embrittlement by intergranular carbon at temperatures above 315°C (600°F), making it suitable for applications involving higher temperatures.
Chemical Composition
The typical chemical composition of Nickel 201 is as follows:
Element | Percentage (%) |
---|---|
Nickel (Ni) | 99.0 min |
Copper (Cu) | 0.25 max |
Iron (Fe) | 0.40 max |
Manganese (Mn) | 0.35 max |
Silicon (Si) | 0.35 max |
Carbon (C) | 0.02 max |
Sulfur (S) | 0.01 max |
Mechanical Properties
Nickel 201 exhibits good mechanical properties over a wide range of temperatures:
- Tensile Strength: 365 MPa (53 ksi) min
- Yield Strength (0.2% offset): 83 MPa (12 ksi) min
- Elongation: 40% min
- Hardness: 65 HRB max
Physical Properties
- Density: 8.89 g/cm³ (0.321 lb/in³)
- Melting Point: 1435°C (2615°F)
- Specific Heat Capacity: 0.11 cal/g·°C (at 20°C)
- Thermal Conductivity: 90.7 W/m·K (at 20°C)
- Electrical Resistivity: 0.096 µΩ·m (at 20°C)
- Modulus of Elasticity: 207 GPa (at 20°C)
- Poisson’s Ratio: 0.31 (at 20°C)
Industries Predominantly Using Nickel 201
- Chemical Processing:
- Manufacturing and handling of sodium hydroxide, particularly at elevated temperatures.
- Production of caustic soda, hydrochloric acid, and other chemicals.
- Electronics:
- Components such as anodes, cathodes, and battery components due to its excellent electrical conductivity.
- Aerospace and Defense:
- Parts requiring resistance to corrosion and good mechanical properties at elevated temperatures.
- Food Processing:
- Equipment and machinery due to its resistance to food acids and alkalies.
Typical Manufacturing Specifications
- ASTM B161: Specification for Nickel Seamless Pipe and Tube
- ASTM B163: Specification for Seamless Nickel and Nickel Alloy Condenser and Heat Exchanger Tubes
- ASTM B725: Specification for Welded Nickel (UNS N02200/UNS N02201) and Nickel-Copper Alloy (UNS N04400) Pipe
- ASME SB161/SB163/SB725: Standards for nickel alloy seamless and welded pipe and tube
Available Tube Product Forms
- Seamless Tubing
- Welded Tubing
- Straight Lengths
- Coiled Tubing
Typical Applications
- Chemical Processing:
- Equipment and piping systems for handling caustic alkalis such as sodium hydroxide.
- Acid production and handling equipment.
- Electronics:
- Components in electronic applications requiring high electrical conductivity.
- Aerospace and Defense:
- Components exposed to corrosive environments and high temperatures.
- Food Processing:
- Equipment and storage vessels for food and beverage industries.
Welding and Fabrication Characteristics
Welding
- Weldability:
- Nickel 201 can be welded using conventional welding methods such as Gas Tungsten Arc Welding (GTAW/TIG), Gas Metal Arc Welding (GMAW/MIG), and Shielded Metal Arc Welding (SMAW).
- Filler Metals: Typically, matching composition filler metals such as ERNi-1 are used.
- Preheating and Post-Weld Heat Treatment (PWHT):
- Preheating: Generally not required. However, cleanliness is crucial to prevent contamination.
- PWHT: Not typically required for Nickel 201, but can be performed to relieve stresses if necessary.
- Weld Defects and How to Avoid Them:
- Porosity: Ensure clean surfaces and proper shielding gases to minimize porosity.
- Cracking: Nickel 201 is generally resistant to cracking, but control welding parameters to avoid solidification cracking.
Fabrication
- Machining:
- General: Nickel 201 is relatively easy to machine, especially compared to other high-nickel alloys. It can be machined using standard techniques.
- Coolants: Use water-based coolants to reduce heat and friction, thereby extending tool life and improving surface finish.
- Tooling: High-speed steel tools can be used, but carbide tools are recommended for better performance and longer tool life.
- Forming:
- Cold Forming: Nickel 201 can be cold-formed using standard methods. It has excellent ductility, allowing for significant deformation without cracking.
- Hot Forming: Hot forming is typically conducted at temperatures between 650°C and 1230°C (1200°F and 2250°F). Proper temperature control is necessary to prevent grain growth and maintain mechanical properties.
- Heat Treatments:
- Annealing: Annealing is performed to soften the material and relieve stress. For Nickel 201, annealing temperatures range from 705°C to 925°C (1300°F to 1700°F), followed by air cooling.
- Stress Relieving: Stress relieving can be performed at temperatures around 480°C to 750°C (900°F to 1380°F) for 1-2 hours, followed by air cooling.
- Surface Cleaning:
- Pickling: Use a pickling solution of sulfuric acid or nitric acid to remove oxides and scale formed during heat treatment or welding.
- Mechanical Cleaning: Grinding and brushing are effective for removing surface contaminants, but care should be taken to avoid embedding iron particles, which could lead to corrosion.
Best Practices for Welding and Fabrication
- Cleanliness: Maintain a clean work environment to prevent contamination. Contaminants such as sulfur, phosphorus, lead, and zinc can lead to weld defects and corrosion issues.
- Tooling: Use dedicated tools for Nickel 201 to avoid cross-contamination from other metals.
- Controlled Environment: Whenever possible, perform welding and fabrication in a controlled environment to minimize the introduction of impurities.
- Training: Ensure that welders and fabricators are specifically trained for handling high-nickel alloys to achieve the best results.
Conclusion
Nickel 201 (UNS N02201) is a versatile material known for its excellent corrosion resistance, good mechanical properties, and high thermal and electrical conductivity. It is suitable for a wide range of applications, especially in chemical processing, electronics, aerospace, and food processing industries. By adhering to best practices in welding and fabrication, engineers and fabricators can ensure high-quality results and reliable performance in their intended applications.