Difference Between Hot-Dip Galvanizing and Pre-Galvanizing
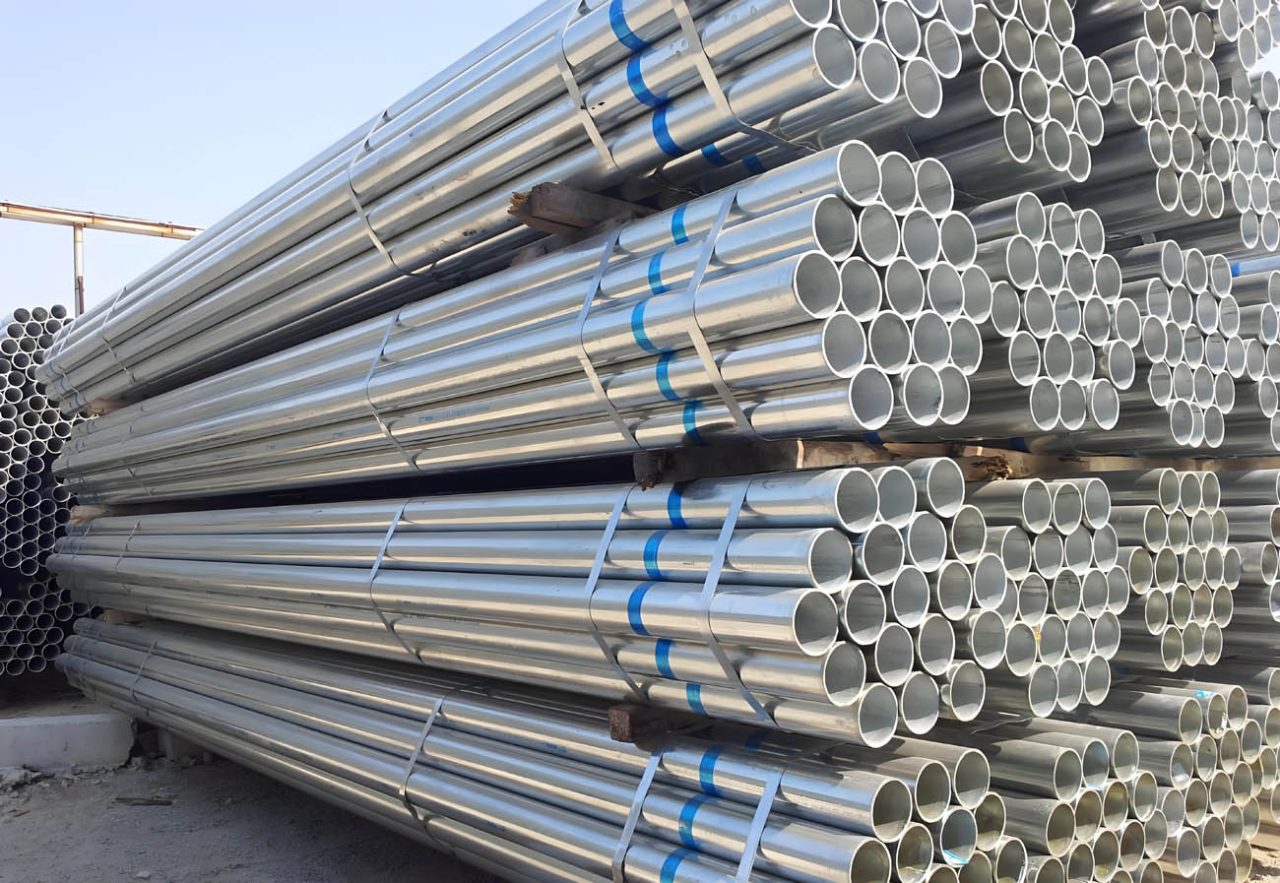
Difference Between Hot-Dip Galvanizing and Pre-Galvanizing
Hot-dip galvanizing and pre-galvanizing are two methods used to apply a protective zinc coating to steel, but they involve different processes and result in different coating characteristics. Understanding these differences is crucial for selecting the right type of galvanized steel for specific applications.
Hot-Dip Galvanizing
Process:
- Preparation: The steel is cleaned through a series of steps including degreasing, pickling in acid to remove oxides, and fluxing to promote the zinc bonding.
- Dipping: The cleaned steel is immersed in a bath of molten zinc, typically heated to around 450°C (842°F).
- Cooling: After coating, the steel is cooled, either by air or by immersion in a quench tank.
Characteristics:
- Coating Thickness: The zinc coating is typically thicker, ranging from 70 microns to 200 microns, depending on the thickness of the steel and the time it is immersed in the zinc bath.
- Coverage: Provides a uniform coating over the entire surface, including edges and corners.
- Durability: Offers superior corrosion resistance, making it ideal for outdoor applications and environments with high humidity or exposure to saltwater.
Applications:
- Structural steel components
- Outdoor construction materials
- Guardrails, poles, and other infrastructure
Pre-Galvanizing
Process:
- Preparation: Similar to hot-dip galvanizing, the steel sheet or coil is cleaned.
- Coating: The cleaned steel is passed through a bath of molten zinc in a continuous process.
- Post-Processing: The coated steel is then cut and formed into the desired shapes, such as pipes or sheets.
Characteristics:
- Coating Thickness: The zinc coating is generally thinner, typically around 20 microns to 50 microns.
- Coverage: More consistent on flat surfaces but may be less effective on edges and welds.
- Durability: Provides adequate protection for less harsh environments but may not be as durable as hot-dip galvanized steel in aggressive conditions.
Applications:
- Indoor plumbing
- Light structural applications
- Fencing and smaller outdoor fixtures
Comparison Table
Feature | Hot-Dip Galvanizing | Pre-Galvanizing |
---|---|---|
Coating Thickness | 70-200 microns | 20-50 microns |
Process | Immersion in molten zinc bath | Continuous coating of steel sheet/coil |
Corrosion Resistance | High (suitable for harsh environments) | Moderate (suitable for less aggressive environments) |
Edge and Weld Coverage | Excellent | Moderate to good |
Cost | Higher due to thicker coating | Lower due to thinner coating |
Typical Applications | Outdoor structures, infrastructure | Indoor plumbing, light structures |
Benefits of Thicker Galvanized Layer
Hot-dip galvanization results in a thicker zinc coating, which offers several advantages:
- Superior Rust Protection: The thicker layer of zinc provides a more robust barrier against corrosion, especially in environments with high moisture, salt, or industrial pollutants.
- Longer Lifespan: The durability of hot-dip galvanized steel often translates to a longer service life, reducing the need for frequent replacements and maintenance.
- Better Edge and Corner Protection: Thicker coatings ensure that even the most vulnerable parts of the steel, such as edges and corners, are well protected.
Zinc Coating Requirements (ASTM A525)
- ASTM A525 Grade G90: Requires a total zinc weight of 0.90 oz/sq ft (0.45 oz/sq ft per side).
- ASTM A525 Grade G120: Requires a total zinc weight of 1.20 oz/sq ft (0.60 oz/sq ft per side).
These standards ensure a minimum level of protection by specifying the zinc coating weight, which directly correlates to the thickness and durability of the protective layer.
Conclusion
When choosing between hot-dip galvanizing and pre-galvanizing, consider the environmental conditions and the specific requirements of your application. Hot-dip galvanizing offers superior protection for harsh environments due to its thicker coating, while pre-galvanizing is a cost-effective solution for less demanding conditions. Both methods, when adhering to standards like ASTM A525, provide reliable corrosion protection for steel components.