ASTM A632 Stainless Steel Pipe
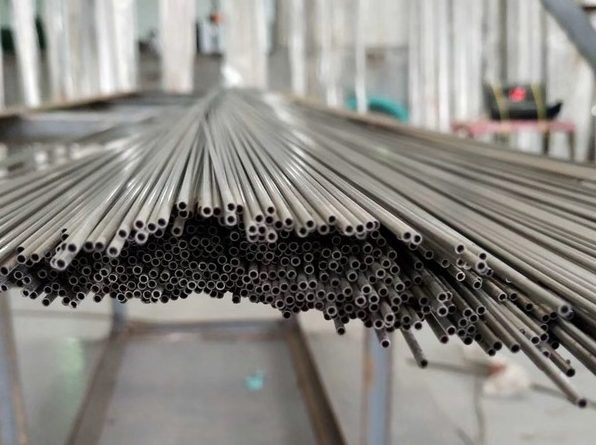
ASTM A632 Stainless Steel Pipe
Introduction
ASTM A632 is the standard specification for seamless and welded austenitic stainless steel tubing intended for low or moderate temperatures and general corrosive service, particularly where a superior surface finish is required. This specification includes seamless and welded pipes in various grades, ensuring versatility and reliability for different applications.
ASTM A632 Specifications
Scope
ASTM A632 covers seamless and welded austenitic stainless steel tubing that is intended for low or moderate temperatures and general corrosive service. This specification includes several grades of austenitic stainless steel, such as TP201, TP202, TP304, TP304L, TP316, and TP316L. The pipes are commonly used in applications requiring good corrosion resistance and a high-quality surface finish.
Chemical Composition
The chemical composition of ASTM A632 stainless steel pipes varies depending on the grade. The following table summarizes the typical chemical composition for some common grades:
Element | TP201 | TP202 | TP304 | TP304L | TP316 | TP316L |
---|---|---|---|---|---|---|
Carbon (C) | 0.15 max | 0.15 max | 0.08 max | 0.03 max | 0.08 max | 0.03 max |
Manganese (Mn) | 5.5-7.5 | 7.5-10.0 | 2.00 max | 2.00 max | 2.00 max | 2.00 max |
Phosphorus (P) | 0.060 max | 0.060 max | 0.045 max | 0.045 max | 0.045 max | 0.045 max |
Sulfur (S) | 0.030 max | 0.030 max | 0.030 max | 0.030 max | 0.030 max | 0.030 max |
Silicon (Si) | 1.00 max | 1.00 max | 1.00 max | 1.00 max | 1.00 max | 1.00 max |
Chromium (Cr) | 16.0-18.0 | 17.0-19.0 | 18.0-20.0 | 18.0-20.0 | 16.0-18.0 | 16.0-18.0 |
Nickel (Ni) | 3.5-5.5 | 4.0-6.0 | 8.0-11.0 | 8.0-13.0 | 10.0-14.0 | 10.0-14.0 |
Molybdenum (Mo) | – | – | – | – | 2.00-3.00 | 2.00-3.00 |
Mechanical Properties
The mechanical properties of ASTM A632 stainless steel pipes are suitable for low to moderate temperature and general service applications. The typical mechanical properties include:
- Tensile Strength: Minimum 515 MPa (75 ksi)
- Yield Strength: Minimum 205 MPa (30 ksi)
- Elongation: Minimum 35% in 2 inches
Tube Sizes
ASTM A632 pipes are available in various sizes, indicating the outside diameter (OD) and wall thickness. The sizes range from small-diameter tubing to larger pipes, catering to different application needs.
Technical Details, Dimensions, and Tolerances
Dimensions
The dimensions of ASTM A632 pipes are specified by their outside diameter (OD) and wall thickness. Standard sizes range from small-diameter tubes to larger pipes. Common dimensions include:
- Outside Diameter (OD): 1/8 inch to 5 inches
- Wall Thickness: Varies based on application requirements.
Tolerances
ASTM A632 specifies precise tolerances to ensure the tubes meet quality and performance standards. These tolerances include:
- Outside Diameter (OD): ±0.1% of the specified OD
- Wall Thickness: ±10% of the specified wall thickness
- Length: Tubes are typically supplied in random lengths, with specific tolerances based on customer requirements.
Wall Thickness & Tolerance
The wall thickness of ASTM A632 pipes is critical for their performance in general service applications. Tolerances on wall thickness are essential to ensure consistent performance. The standard tolerances include:
- Wall Thickness Tolerance: ±10% of the specified wall thickness.
- Minimum Wall Thickness: The minimum wall thickness must not be less than 87.5% of the specified nominal wall thickness.
Materials and Manufacture
Materials
ASTM A632 pipes are made from austenitic stainless steels, known for their excellent corrosion resistance, good strength, and superior surface finish. Common grades include TP201, TP202, TP304, TP304L, TP316, and TP316L, each offering specific advantages for different applications.
Manufacture
The manufacturing process for ASTM A632 pipes involves several steps to ensure quality and performance:
- Seamless Tube Production: Seamless tubes are produced by extruding or piercing solid billets of stainless steel.
- Welded Tube Production: Welded tubes are produced by forming and welding strips of stainless steel. The weld seam is typically subjected to heat treatment to ensure homogeneity and strength.
- Cold Working: Cold working processes such as cold drawing or cold pilgering may be used to achieve the desired dimensions and surface finish.
Tests
To ensure the quality and performance of ASTM A632 pipes, several tests are conducted:
Hydrostatic Test
A hydrostatic test is performed to verify the pipes’ ability to withstand internal pressure. The pipes are filled with water and pressurized to a specified level, typically 1.5 times the design pressure, to check for leaks and structural integrity.
Nondestructive Testing (NDT)
Nondestructive testing methods are used to detect internal and surface defects without damaging the pipes. Common NDT methods include:
- Ultrasonic Testing: High-frequency sound waves are used to detect internal flaws.
- Eddy Current Testing: Electromagnetic induction is used to detect surface defects.
- Radiographic Testing: X-rays or gamma rays are used to inspect the internal structure.
Mechanical Tests
Mechanical tests are conducted to verify the pipes’ mechanical properties, including:
- Tensile Test: Measures tensile strength, yield strength, and elongation.
- Hardness Test: Verifies hardness levels to ensure compliance with specified limits.
- Flattening Test: Checks the pipe’s ability to withstand deformation without cracking.
Heat Treatment
Heat treatment is an essential process for enhancing the properties of ASTM A632 pipes. The specific heat treatment process depends on the grade and application requirements:
Annealing
Annealing involves heating the pipes to a temperature above the critical temperature (usually around 1040-1120°C) and then rapidly cooling them in water or air. This process dissolves precipitated carbides and restores the material’s corrosion resistance and ductility.
Stress Relieving
Stress relieving involves heating the pipes to a temperature lower than the critical temperature (usually around 400-500°C) and then cooling them slowly. This process relieves internal stresses caused by manufacturing processes such as cold working.