K55 Casing Tubing
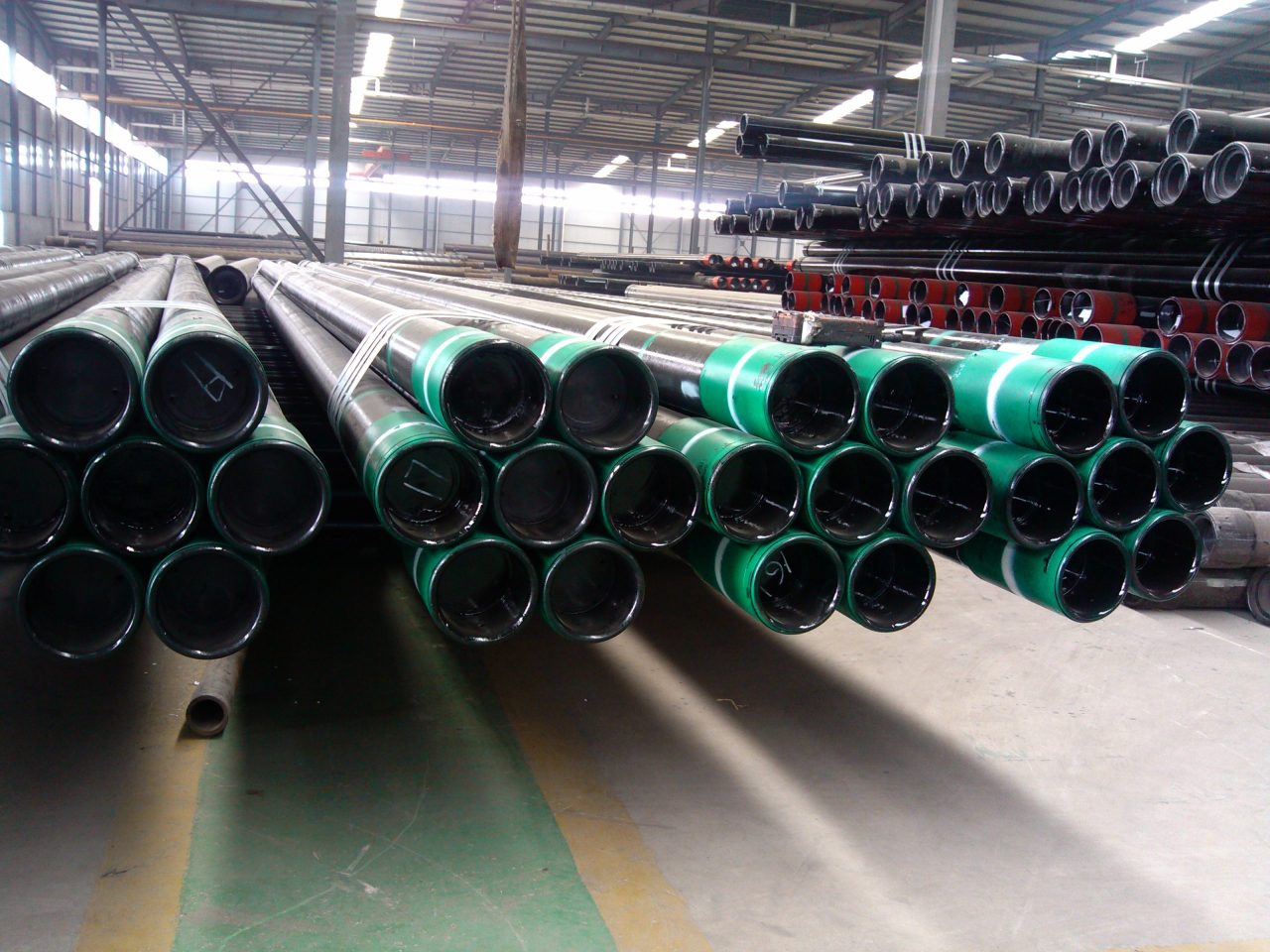
K55 Casing Tubing
Introduction
K55 casing tubing is a type of steel pipe used primarily in the oil and gas industry for the extraction of hydrocarbons. It serves as a conduit to transport oil and gas from the underground reservoirs to the surface. K55 is a grade within the API 5CT specification, known for its balance of strength and cost-effectiveness, making it suitable for medium-depth wells and moderate-pressure environments.
API Specifications
Scope
API 5CT specifies the requirements for casing and tubing used in oil and gas wells. K55 casing tubing is designed to meet these standards, ensuring it can withstand the operational pressures and environmental conditions encountered during drilling and production.
Chemical Composition
The chemical composition of K55 casing tubing ensures a balance of strength, toughness, and weldability. The typical chemical composition includes:
Element | Composition (%) |
---|---|
Carbon (C) | 0.28 max |
Manganese (Mn) | 1.20 max |
Phosphorus (P) | 0.030 max |
Sulfur (S) | 0.030 max |
Silicon (Si) | 0.55 max |
Mechanical Properties
The mechanical properties of K55 casing tubing are designed to ensure durability and reliability under various operational conditions. The typical mechanical properties include:
- Tensile Strength: 655-758 MPa (95-110 ksi)
- Yield Strength: Minimum 379 MPa (55 ksi)
- Elongation: Minimum 19% in 2 inches
Pipe Sizes
K55 casing tubing is available in a range of sizes to accommodate different wellbore diameters and depths. Standard sizes are specified by their outside diameter (OD) and wall thickness. Common sizes include:
- Outside Diameter (OD): 4 1/2 inches to 20 inches
- Wall Thickness: Varies based on application requirements (e.g., 0.224 inches, 0.250 inches, etc.)
Technical Details, Dimensions, and Tolerances
Dimensions
The dimensions of K55 casing tubing are specified by their outside diameter (OD) and wall thickness. Standard sizes adhere to API 5CT requirements. Common dimensions include:
- Outside Diameter (OD): 4 1/2 inches to 20 inches
- Wall Thickness: Varies based on application requirements.
Tolerances
API 5CT outlines precise tolerances to ensure the pipes meet quality and performance standards. These tolerances include:
- Outside Diameter (OD): ±1% of the specified OD
- Wall Thickness: ±12.5% of the specified wall thickness
- Weight: ±10% of the nominal weight per unit length
Wall Thickness & Tolerance
The wall thickness of K55 casing tubing is critical for its performance in drilling and production operations. Tolerances on wall thickness ensure consistent performance. The standard tolerances include:
- Wall Thickness Tolerance: ±12.5% of the specified wall thickness.
- Minimum Wall Thickness: The minimum wall thickness must not be less than 87.5% of the specified nominal wall thickness.
API CASING/ API 5CT K55 CASING TUBING SPECIFICATIONS
– Specification & Size of API 5CT K55 Tubing
DN | O. D. | Weight | W. T. | End Processing | |||||||||
---|---|---|---|---|---|---|---|---|---|---|---|---|---|
Non-upset coupling-thread | Upset coupling-thread | Steel Grade | |||||||||||
in | mm | lb./ft. | lb./ft. | in | mm | H40 | J55 | L80 | N80 | C90 | T95 | P110 | |
2 3/8 | 2.38 | 60.3 | 4 | – | 0.167 | 4.24 | PU | PN | PN | PN | PN | PN | – |
4.6 | 4.7 | 0.19 | 4.83 | PNU | PNU | PNU | PNU | PNU | PNU | PNU | |||
5.8 | 5.95 | 0.254 | 6.45 | – | – | PNU | PNU | PNU | PNU | PNU | |||
6.6 | – | 0.295 | 7.49 | – | – | P | – | P | P | – | |||
7.35 | 7.45 | 0.336 | 8.53 | – | – | PU | – | PU | PU | – | |||
2 7/8 | 2.88 | 73 | 6.4 | 6.5 | 0.217 | 5.51 | PNU | PNU | – | – | – | – | – |
7.8 | 7.9 | 0.276 | 7.01 | – | – | – | – | – | – | – | |||
8.6 | 8.7 | 0.308 | 7.82 | – | – | PLB | PLB | PLBE | – | PLB | |||
9.35 | 9.45 | 0.34 | 8.64 | – | – | PLB | PLB | PLBE | – | PLB | |||
10.5 | – | 0.392 | 9.96 | – | – | PLB | PLB | PLB | – | PLB | |||
11.5 | – | 0.44 | 11.18 | – | – | – | – | PLB | – | ||||
3 1/2 | 3.5 | 88.9 | 7.7 | – | 0.216 | 5.49 | PN | PN | PN | PN | PN | PN | – |
9.2 | 9.3 | 0.254 | 6.45 | PNU | PNU | PNU | PNU | PNU | PNU | PNU | |||
10.2 | – | 0.289 | 7.34 | PN | PN | PN | PN | PN | PN | – | |||
12.7 | 12.95 | 0.375 | 9.52 | – | – | PNU | PNU | PNU | PNU | PNU | |||
14.3 | – | 0.43 | 10.92 | – | – | P | – | P | P | – | |||
15.5 | – | 0.476 | 12.09 | – | – | P | – | P | P | – | |||
17 | – | 0.53 | 13.46 | – | – | P | – | P | P | – | |||
4 | 4 | 102 | 9.5 | – | 0.226 | 5.74 | PN | PN | PN | PN | PN | PN | – |
– | 11 | 0.262 | 6.65 | PU | PU | PU | PU | PU | PU | – | |||
13.2 | – | 0.33 | 8.38 | – | – | P | – | P | P | – | |||
16.1 | – | 0.415 | 10.54 | – | – | P | – | P | P | – | |||
18.9 | – | 0.5 | 12.7 | – | – | P | – | P | P | – | |||
22.2 | – | 0.61 | 15.49 | – | – | P | – | P | P | – | |||
4 1/2 | 4.5 | 114 | 12.6 | 12.75 | 0.271 | 6.88 | PNU | PNU | PNU | PNU | PNU | PNU | – |
15.2 | – | 0.337 | 8.56 | – | – | P | – | P | P | – | |||
17 | – | 0.38 | 9.65 | – | – | P | – | P | P | – | |||
18.9 | – | 0.43 | 10.92 | – | – | P | – | P | P | PLB | |||
21.5 | – | 0.5 | 12.7 | – | – | P | – | P | P | PLB | |||
23.7 | – | 0.56 | 14.22 | – | – | P | – | P | P | PLB | |||
26.1 | – | 0.63 | 16 | – | – | P | – | P | P | PLB | |||
P——Plain;N—— Non-upset coupling-thread;U—— Upset coupling-thread; L——Integral |
– Specification & Size of API 5CT K55 Casing
DN | O. D. | Weight | W. T. | End Machining Form | ||||||||
---|---|---|---|---|---|---|---|---|---|---|---|---|
Steel Grade | ||||||||||||
in | mm | lb/ft | kg/m | in | mm | H40 | J55 | L80 | N80 | C90 | P110 | |
K55 | T95 | |||||||||||
4 1/2 | 4.500 | 114.3 | 9.5 | 14.14 | 0.205 | 5.21 | PS | PS | – | – | – | – |
10.5 | 15.63 | 0.224 | 5.69 | – | PSB | – | – | – | – | |||
11.6 | 17.26 | 0.250 | 6.35 | – | PSLB | PLB | PLB | PLB | PLB | |||
13.5 | 20.09 | 0.290 | 7.37 | – | – | PLB | PLB | PLB | PLB | |||
15.1 | 22.47 | 0.337 | 9.56 | – | – | – | – | – | PLB | |||
5 | 5.000 | 127 | 11.5 | 17.11 | 0.220 | 5.59 | – | PS | – | – | – | – |
13 | 19.35 | 0.253 | 6.43 | – | PSLB | – | – | – | – | |||
15 | 22.32 | 0.296 | 7.52 | – | PSLB | PLB | PLB | PLBE | PLB | |||
18 | 26.79 | 0.362 | 9.19 | – | – | PLB | PLB | PLBE | PLB | |||
21.4 | 31.85 | 0.437 | 11.1 | – | – | PLB | PLB | PLB | PLB | |||
23.2 | 34.53 | 0.478 | 12.14 | – | – | – | – | PLB | – | |||
24.1 | 35.86 | 0.500 | 12.7 | – | – | – | – | PLB | – | |||
5 1/2 | 5.500 | 139.7 | 14 | 20.83 | 0.244 | 6.2 | PS | PS | – | – | – | – |
15.5 | 23.07 | 0.275 | 6.98 | – | PSLB | – | – | – | – | |||
17 | 25.3 | 0.304 | 7.72 | – | PSLB | PLB | PLB | PLBE | PLB | |||
20 | 29.76 | 0.361 | 9.17 | – | – | PLB | PLB | PLBE | PLB | |||
23 | 34.23 | 0.415 | 10.54 | – | – | PLB | PLB | PLBE | PLB | |||
26.8 | 39.88 | 0.500 | 12.7 | – | – | – | – | – | – | |||
29.7 | 44.2 | 0.562 | 14.27 | – | – | – | – | – | – | |||
32.6 | 48.51 | 0.625 | 15.88 | – | – | – | – | – | – | |||
35.3 | 52.53 | 0.687 | 17.45 | – | – | – | – | – | – | |||
38 | 56.55 | 0.750 | 19.05 | – | – | – | – | – | – | |||
40.5 | 60.27 | 0.812 | 20.62 | – | – | – | – | – | – | |||
43.1 | 64.14 | 0.875 | 22.22 | – | – | – | – | – | – | |||
6 5/8 | 6.625 | 168.28 | 20 | 29.76 | 0.288 | 7.32 | PS | PSLB | – | – | – | – |
24 | 35.72 | 0.352 | 8.94 | – | PSLB | PLB | PLB | PLBE | PLB | |||
28 | 41.67 | 0.417 | 10.59 | – | – | PLB | PLB | PLBE | PLB | |||
32 | 47.62 | 0.475 | 12.06 | – | – | PLB | PLB | PLBE | PLB | |||
7 | 7.000 | 177.8 | 17 | 25.3 | 0.231 | 5.87 | PS | – | – | – | – | – |
20 | 29.76 | 0.272 | 6.91 | PS | PS | – | – | – | – | |||
23 | 34.23 | 0.317 | 8.05 | – | PSLB | PLB | PLB | PLBE | – | |||
26 | 38.69 | 0.362 | 9.19 | – | PSLB | PLB | PLB | PLBE | PLB | |||
29 | 43.16 | 0.408 | 10.36 | – | – | PLB | PLB | PLBE | PLB | |||
32 | 47.62 | 0.453 | 11.51 | – | – | PLB | PLB | PLBE | PLB | |||
35 | 52.09 | 0.498 | 12.65 | – | – | PLB | PLB | PLBE | PLB | |||
38 | 56.55 | 0.540 | 13.72 | – | – | PLB | PLB | PLBE | PLB | |||
42.7 | 63.54 | 0.625 | 15.88 | – | – | – | – | – | – | |||
46.4 | 69.05 | 0.687 | 17.45 | – | – | – | – | – | – | |||
50.1 | 74.56 | 0.750 | 19.05 | – | – | – | – | – | – | |||
53.6 | 79.77 | 0.812 | 20.62 | – | – | – | – | – | – | |||
57.1 | 84.97 | 0.875 | 22.22 | – | – | – | – | – | – | |||
7 5/8 | 7.625 | 193.68 | 24 | 35.72 | 0.300 | 7.62 | PS | – | – | – | – | – |
26.4 | 39.29 | 0.328 | 8.33 | – | PSLB | PLB | PLB | PLBE | PLB | |||
29.7 | 44.2 | 0.375 | 9.52 | – | – | PLB | PLB | PLBE | PLB | |||
33.7 | 50.15 | 0.430 | 10.92 | – | – | PLB | PLB | PLBE | PLB | |||
39 | 58.05 | 0.500 | 12.7 | – | – | PLB | PLB | PLBE | PLB | |||
42.8 | 63.69 | 0.562 | 14.27 | – | – | PLB | PLB | PLB | PLB | |||
45.3 | 67.41 | 0.595 | 15.11 | – | – | PLB | PLB | PLB | PLB | |||
47.1 | 70.09 | 0.625 | 15.88 | – | – | PLB | PLB | PLB | PLB | |||
51.2 | 76.19 | 0.687 | 17.45 | – | – | – | – | – | – | |||
55.3 | 80.3 | 0.750 | 19.05 | – | – | – | – | – | – | |||
8 5/8 | 8.625 | 219.08 | 24 | 35.72 | 0.264 | 6.71 | – | PS | – | – | – | – |
28 | 41.62 | 0.304 | 7.72 | PS | – | – | – | – | – | |||
32 | 47.62 | 0.352 | 8.94 | PS | PSLB | – | – | – | – | |||
36 | 53.57 | 0.400 | 10.16 | – | PSLB | PLB | PLB | PLBE | PLB | |||
40 | 59.53 | 0.450 | 11.43 | – | – | PLB | PLB | PLBE | PLB | |||
44 | 65.48 | 0.500 | 12.7 | – | – | PLB | PLB | PLBE | PLB | |||
49 | 72.92 | 0.557 | 14.15 | – | – | PLB | PLB | PLBE | PLB | |||
9 5/8 | 9.625 | 244.48 | 32.3 | 48.07 | 0.312 | 7.92 | PS | – | – | – | – | – |
36 | 53.57 | 0.352 | 8.94 | PS | PSLB | – | – | – | – | |||
40 | 59.53 | 0.395 | 10.03 | – | PSLB | PLB | PLB | PLBE | – | |||
43.5 | 64.73 | 0.435 | 11.05 | – | – | PLB | PLB | PLBE | PLB | |||
47 | 69.94 | 0.472 | 11.99 | – | – | PLB | PLB | PLBE | PLB | |||
53.5 | 79.62 | 0.545 | 13.84 | – | – | PLB | PLB | PLBE | PLB | |||
58.4 | 86.91 | 0.595 | 15.11 | – | – | PLB | PLB | PLB | PLB | |||
59.4 | 88.4 | 0.609 | 15.47 | – | – | – | – | – | – | |||
64.9 | 96.58 | 0.672 | 17.07 | – | – | – | – | – | – | |||
70.3 | 104.62 | 0.734 | 18.64 | – | – | – | – | – | – | |||
75.6 | 112.5 | 0.797 | 20.24 | – | – | – | – | – | – | |||
10 3/4 | 10.750 | 273.05 | 32.75 | 48.74 | 0.279 | 7.09 | PS | – | – | – | – | – |
40.5 | 60.27 | 0.350 | 8.89 | PS | PSB | – | – | – | – | |||
15.5 | 67.71 | 0.400 | 10.16 | – | PSB | – | – | – | – | |||
51 | 75.9 | 0.450 | 11.43 | – | PSB | PSB | PSB | PSBE | PSB | |||
55.5 | 82.59 | 0.495 | 12.57 | – | – | PSB | PSB | PSBE | PSB | |||
60.7 | 90.33 | 0.545 | 13.84 | – | – | – | – | PSBE | PSB | |||
65.7 | 97.77 | 0.595 | 15.11 | – | – | – | – | PSB | PSB | |||
73.2 | 108.93 | 0.672 | 17.07 | – | – | – | – | – | – | |||
79.2 | 117.86 | 0.734 | 18.64 | – | – | – | – | – | – | |||
85.3 | 126.94 | 0.797 | 20.24 | – | – | – | – | – | – | |||
11 3/4 | 11.750 | 42 | 62.5 | 0.333 | 8.46 | PS | – | – | – | – | – | |
47 | 69.94 | 0.375 | 20.24 | – | – | – | – | – | – | |||
54 | 80.36 | 0.435 | 8.46 | – | – | – | – | – | – | |||
60 | 89.29 | 0.489 | 9.53 | – | – | – | – | – | – | |||
65 | 96.73 | 0.534 | 11.05 | – | – | – | – | – | – | |||
71 | 105.66 | 0.582 | 14.42 | – | – | – | – | – | – | |||
13 3/8 | 13.375 | 339.73 | 48 | 71.43 | 0.330 | 8.38 | PS | – | – | – | – | – |
54.5 | 81.1 | 0.380 | 9.65 | – | PSB | – | – | – | – | |||
61 | 90.78 | 0.430 | 10.92 | – | PSB | – | – | – | – | |||
68 | 101.19 | 0.480 | 12.19 | – | PSB | PSB | PSB | PSB | PSB | |||
72 | 107.15 | 0.514 | 13.06 | – | – | PSB | PSB | PSB | PSB | |||
16 | 16.000 | 406.4 | 65 | 96.73 | 0.375 | 9.53 | PS | – | – | – | – | – |
75 | 111.61 | 0.438 | 11.13 | – | PSB | – | – | – | – | |||
84 | 125.01 | 0.495 | 12.57 | – | PSB | – | – | – | – | |||
109 | 162.21 | 0.656 | 16.66 | – | P | P | P | – | P | |||
18 5/8 | 18.625 | 473.08 | 87.5 | 130.21 | 0.435 | 11.05 | PS | PSB | – | – | – | – |
20 | 20.000 | 508 | 94 | 139.89 | 0.438 | 11.13 | PSL | PSLB | – | – | – | – |
106.5 | 158.49 | 0.500 | 12.7 | – | PSLB | – | – | – | – | |||
133 | 197.93 | 0.635 | 16.13 | – | PSLB | – | – | – | – | |||
P——Plain;S——Short-thread;L——Long-thread;B——Buttress thread;E——Extreme thread |
API 5CT K55 TOLERANCE
Item | Allowable Tolerance | |
---|---|---|
Outer diameter | Pipe body | D≤101.60mm±0.79mm |
D≥114.30mm+1.0% | ||
-0.50% |
Materials and Manufacture
Materials
K55 casing tubing is made from carbon steel, providing a balance of strength, toughness, and cost-effectiveness. The material is suitable for applications where moderate strength and resistance to collapse and internal pressure are required.
Manufacture
The manufacturing process for K55 casing tubing involves several steps to ensure quality and performance:
- Steelmaking: High-quality carbon steel is produced through processes such as electric arc furnace (EAF) or basic oxygen furnace (BOF).
- Forming: The steel is formed into cylindrical shapes using processes such as seamless rolling or welding.
- Heat Treatment: The pipes may undergo heat treatment processes such as normalizing or quenching and tempering to enhance their mechanical properties.
- Finishing: The pipes are finished to achieve the desired surface quality, dimensions, and tolerances.
Tests
To ensure the quality and performance of K55 casing tubing, several tests are conducted as per API 5CT requirements:
Hydrostatic Test
A hydrostatic test is performed to verify the pipes’ ability to withstand internal pressure. The pipes are filled with water and pressurized to a specified level to check for leaks and structural integrity.
Nondestructive Testing (NDT)
Nondestructive testing methods are used to detect internal and surface defects without damaging the pipes. Common NDT methods include:
- Ultrasonic Testing: High-frequency sound waves are used to detect internal flaws.
- Magnetic Particle Inspection: Detects surface and near-surface defects using magnetic fields.
Mechanical Tests
Mechanical tests are conducted to verify the pipes’ mechanical properties, including:
- Tensile Test: Measures tensile strength, yield strength, and elongation.
- Hardness Test: Verifies hardness levels to ensure compliance with specified limits.
- Flattening Test: Checks the pipe’s ability to withstand deformation without cracking.
Heat Treatment
Heat treatment processes such as normalizing or quenching and tempering may be applied to K55 casing tubing to enhance their mechanical properties and ensure consistent performance:
Normalizing
Normalizing involves heating the pipes to a temperature above the critical temperature and then cooling them in air. This process refines the grain structure, improving toughness and strength.
Quenching and Tempering
Quenching and tempering involves heating the pipes to a high temperature, quenching them in water or oil to rapidly cool, and then reheating to a lower temperature to relieve stresses and improve toughness.
Conclusion
K55 casing tubing is a crucial component in the drilling and production of oil and gas wells. It is manufactured to meet API 5CT standards, ensuring quality, performance, and reliability. Through rigorous manufacturing processes, precise dimensions and tolerances, and comprehensive testing, K55 casing tubing delivers dependable performance in various drilling and production environments.