API 5CT Casing and Tubing
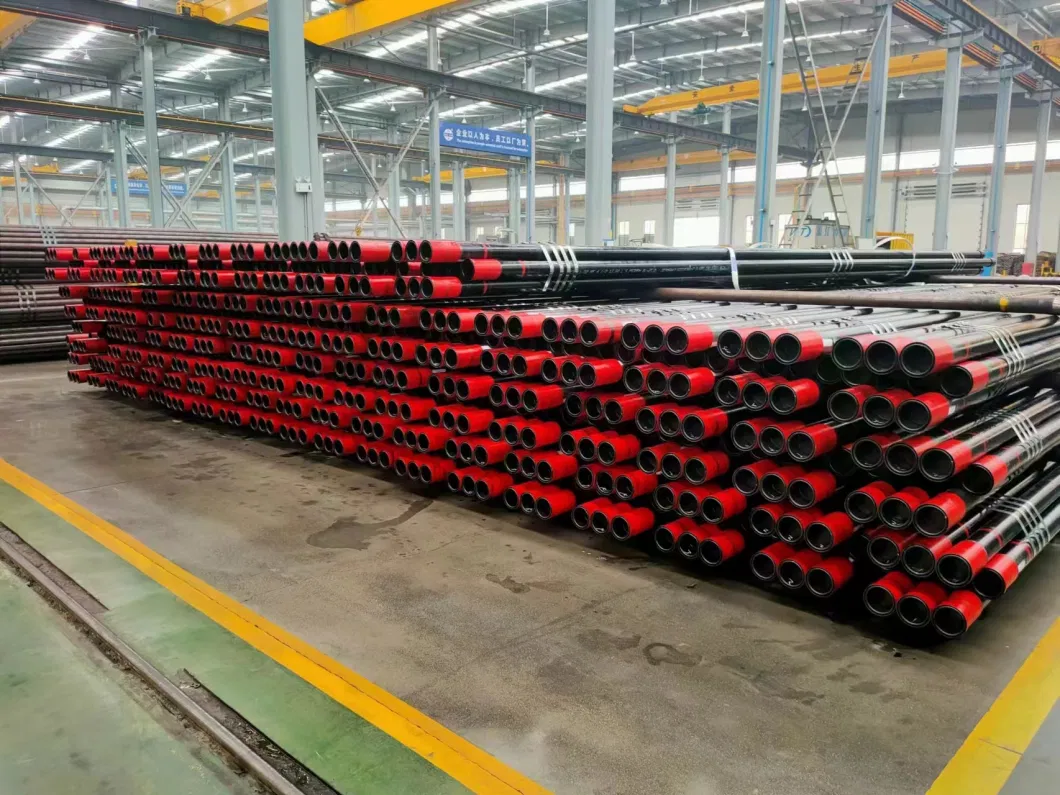
API 5CT Casing and Tubing
Introduction
API 5CT is a specification developed by the American Petroleum Institute (API) for casing and tubing materials used in the oil and gas industry. It covers a range of steel grades designed to meet various operational and environmental challenges. These materials are critical for drilling and production operations, providing structural integrity and transport pathways within the wellbore.
Key Components
Casing
Casing is a large-diameter pipe inserted into a drilled well and cemented in place to provide structural integrity and isolate different subsurface zones.
- Conductor Casing: The first casing run to protect the well from surface water.
- Surface Casing: Prevents caving and isolates shallow water zones.
- Intermediate Casing: Isolates formations and stabilizes the well.
- Production Casing: Ensures the integrity of the well during the production phase.
Tubing
Tubing is a smaller-diameter pipe placed inside the casing to transport hydrocarbons from the reservoir to the surface.
- Production Tubing: Conveys oil and gas to the surface.
- Injection Tubing: Used for injecting fluids into the well.
Standards and Grades
API 5CT specifies various grades of casing and tubing, each tailored for different environmental and operational conditions. Key grades include:
- H40, J55, K55: Basic grades for standard drilling operations.
- N80, L80, C90: Higher strength grades for deeper and more challenging wells.
- T95, P110, Q125: High-strength grades for ultra-deep and high-pressure environments.
- V150: The highest strength grade for the most extreme conditions.
O.D: 4 1/2″-20″
Length: R1, R2, R3
Connection: STC, LTC, BTC, Premium Connection (VAM TOP, NEW VAM, PH-6)
Casing Pipe Data Table
Labels a | OD mm |
Nominal Linear Mass b,c T&C kg/m |
WT t mm |
Type of end-finish d | ||||||||
H40 | J55 K55 |
M65 | L80 R95 |
N80 Type 1, Q |
C90 T95 |
P110 | Q125 | |||||
1 | 2 | |||||||||||
1 | 2 | 3 | 4 | 5 | 6 | 7 | 8 | 9 | 10 | 11 | 12 | 13 |
4-1/2 4-1/2 4-1/2 4-1/2 4-1/2 |
9.50 10.50 11.60 13.50 15.10 |
114.30 114.30 114.30 114.30 114.30 |
14.14 15.63 17.26 20.09 22.47 |
5.21 5.69 6.35 7.37 8.56 |
PS – – – – |
PS PSB PSLB – – |
PS PSB PLB PLB – |
– – PLB PLB – |
– – PLB PLB – |
– – PLB PLB – |
– – PLB PLB PLB |
– – – – PLB |
5 5 5 5 5 5 5 |
11.50 13.00 15.00 18.00 21.40 23.20 24.10 |
127.00 127.00 127.00 127.00 127.00 127.00 127.00 |
17.11 19.35 22.32 26.79 31.85 34.53 35.86 |
5.59 6.43 7.52 9.19 11.10 12.14 12.70 |
– – – – – – – |
PS PSLB PSLBE – – – – |
PS PSLB PLB PLB PLB – – |
– – PLB PLB PLB PLB PLB |
– – PLB PLB PLB PLB PLB |
– – PLB PLB PLB PLB PLB |
– – PLB PLB PLB PLB PLB |
– – – PLB PLB PLB PLB |
5-1/2 5-1/2 5-1/2 5-1/2 5-1/2 5-1/2 5-1/2 5-1/2 5-1/2 5-1/2 5-1/2 5-1/2 |
14.00 15.50 17.00 20.00 23.00 26.80 29.70 32.60 35.30 38.00 40.50 43.10 |
139.70 139.70 139.70 139.70 139.70 139.70 139.70 139.70 139.70 139.70 139.70 139.70 |
20.83 23.07 25.30 29.76 34.23 39.88 44.20 48.51 52.53 56.55 60.27 61.14 |
6.20 6.98 7.72 9.17 10.54 12.70 14.27 15.88 17.45 19.05 20.62 22.22 |
PS – – – – – – – – – – – |
PS PSLBE PSLBE – – – – – – – – – |
PS PSLB PLB PLB PLB – – – – – – – |
– – PLBE PLBE PLBE – – – – – – – |
– – PLBE PLBE PLBE – – – – – – – |
– – PLBE PLBE PLBE P P P P P P P |
– – PLBE PLBE PLBE – – – – – – – |
– – – – PLBE – – – – – – – |
6-5/8 6-5/8 6-5/8 6-5/8 |
20.00 24.00 28.00 32.00 |
168.28 168.28 168.28 168.28 |
29.76 35.72 41.67 47.62 |
7.32 8.94 10.59 12.06 |
PS – – – |
PSLB PSLBE – – |
PSLB PLB PLB – |
– PLBE PLBE PLBE |
– PLBE PLBE PLBE |
– PLBE PLBE PLBE |
– PLBE PLBE PLBE |
– – – PLBE |
7 7 7 7 7 7 7 |
17.00 20.00 23.00 26.00 29.00 32.00 35.00 |
177.80 177.80 177.80 177.80 177.80 177.80 177.80 |
25.30 29.76 34.23 38.69 43.16 47.62 52.09 |
5.87 6.91 8.05 9.19 10.36 11.51 12.65 |
PS PS – – – – – |
– PS PSLBE PSLBE – – – |
– PS PLB PLB PLB PLB – |
– – PLB PLB PLB PLB PLB |
– – PLB PLB PLB PLB PLB |
– – PLB PLB PLB PLB PLB |
– – – PLB PLB PLB PLBE |
– – – – – – PLB |
7 7 7 7 7 7 |
38.00 42.70 46.40 50.10 53.60 57.10 |
177.80 177.80 177.80 177.80 177.80 177.80 |
56.55 63.54 69.05 74.56 79.77 84.97 |
13.72 15.88 17.45 19.05 20.62 22.22 |
– – – – – – |
– – – – – – |
– – – – – – |
PLB – – – – – |
PLB – – – – – |
PLB P P P P P |
PLB – – – – – |
PLB – – – – – |
7-5/8 7-5/8 7-5/8 7-5/8 7-5/8 7-5/8 7-5/8 7-5/8 7-5/8 7-5/8 |
24.00 26.40 29.70 33.70 39.00 42.80 45.30 47.10 51.20 55.30 |
193.68 193.68 193.68 193.68 193.68 193.68 193.68 193.68 193.68 193.68 |
35.72 39.29 44.20 50.15 58.04 63.69 67.41 70.09 76.19 82.30 |
7.62 8.33 9.52 10.92 12.70 14.27 15.11 15.88 17.45 19.05 |
PS – – – – – – – – – |
– PSLB – – – – – – – – |
– PSLB PLB PLB – – – – – – |
– PLB PLB PLB PLB PLB PLB PLB – – |
– PLB PLB PLB PLB PLB PLB PLB – – |
– PLB PLB PLB PLB PLB PLB PLB P P |
– – PLB PLB PLB PLB PLB PLB – – |
– – – – PLB PLB PLB PLB – – |
7-3/4 | 46.10 | 196.85 | 68.60 | 15.11 | – | – | – | P | P | P | P | P |
8-5/8 8-5/8 8-5/8 8-5/8 8-5/8 8-5/8 8-5/8 |
24.00 28.00 32.00 36.00 40.00 44.00 49.00 |
219.08 219.08 219.08 219.08 219.08 219.08 219.08 |
35.72 41.67 47.62 53.57 59.53 65.48 72.92 |
6.71 7.72 8.94 10.16 11.43 12.70 14.15 |
– PS PS – – – – |
PS PS – PSLB PSLB PLB – |
PS PS PSLB PSLB PLB – – |
– – – PLB PLB PLB PLB |
– – – PLB PLB PLB PLBE |
– – – PLBE PLBE PLBE PLBE |
– – – PLB PLB PLB |
– – – – – PLB |
9-5/8 9-5/8 9-5/8 9-5/8 9-5/8 9-5/8 9-5/8 9-5/8 9-5/8 9-5/8 9-5/8 |
32.30 36.00 40.00 43.50 47.00 53.50 58.40 59.40 64.90 70.30 75.60 |
244.48 244.48 244.48 244.48 244.48 244.48 244.48 244.48 244.48 244.48 244.48 |
48.07 53.57 59.53 64.73 69.94 79.62 86.91 88.40 96.58 104.62 112.50 |
7.92 8.94 10.03 11.05 11.99 13.84 15.11 15.47 17.07 18.64 20.24 |
PS PS – – – – – – – – – |
– PSLB PSLB – – – – – |
– PSLB PSLB PLB PLB – – – – – |
– – PLB PLB PLB PLB PLB – – – – |
– – PLB PLB PLB PLB PLB – – – |
– – PLB PLB PLB PLB PLB P P P P |
– – – PLB PLB PLB PLB – – – – |
– – – – PLB PLB PLB – – – – |
10-3/4 10-3/4 10-3/4 10-3/4 10-3/4 10-3/4 10-3/4 10-3/4 10-3/4 10-3/4 |
32.75 40.50 45.50 51.00 55.50 60.70 65.70 73.20 79.20 85.30 |
273.05 273.05 273.05 273.05 273.05 273.05 273.05 273.05 273.05 273.05 |
48.74 60.27 67.71 75.90 82.59 90.33 97.77 108.93 117.86 126.94 |
7.09 8.89 10.16 11.43 12.57 13.84 15.11 17.07 18.64 20.24 |
PS PS – – – – – – – – |
– PSB PSB PSB – – – – – – |
– PSB PSB PSB PSB – – – – – |
– – – PSB PSB – – – – – |
– – – PSB PSB – – – – – |
– – – PSB PSB PSB PSB P P P |
– – – PSB PSB PSB PSB – – – |
– – – – – PSB PSB – – – |
11-3/4 11-3/4 11-3/4 11-3/4 11-3/4 11-3/4 |
42.00 47.00 54.00 60.00 65.00 71.00 |
298.45 298.45 298.45 298.45 298.45 298.45 |
62.50 69.94 80.36 89.29 96.73 105.66 |
8.46 9.53 11.05 12.42 13.56 14.78 |
PS – – – – – |
– PSB PSB PSB – – |
– PSB PSB PSB – – |
– – – PSB P P |
– – – PSB P P |
– – – PSB P P |
– – – PSB P P |
– – – PSB P P |
13-3/8 13-3/8 13-3/8 13-3/8 13-3/8 |
48.00 54.50 61.00 68.00 72.00 |
339.72 339.72 339.72 339.72 339.72 |
71.43 81.10 90.78 101.19 107.15 |
8.38 9.65 10.92 12.19 13.06 |
PS – – – – |
– PSB PSB PSB – |
– PSB PSB PSB – |
– – – PSB PSB |
– – – PSB PSB |
– – – PSB PSB |
– – – PSB PSB |
– – – – PSB |
16 16 16 16 |
65.00 75.00 84.00 109.00 |
406.40 406.40 406.40 406.40 |
96.73 111.61 125.01 162.21 |
9.53 11.13 12.57 16.66 |
PS – – – |
– PSB PSB P |
– PSB PSB – |
– – – P |
– – – P |
– – – – |
– – – P |
– – – P |
18-5/8 | 87.50 | 473.08 | 130.21 | 11.05 | PS | PSB | PSB | – | – | – | – | – |
20 20 20 |
94.00 106.50 133.00 |
508.00 508.00 508.00 |
139.89 158.49 197.93 |
11.13 12.70 16.13 |
PSL – – |
PSLB PSLB PSLB |
PSLB PSLB – |
– – – |
– – – |
– – – |
– – – |
– – – |
P=Plain end; S=short round thread; L=Long round thread; B–Buttress thread; | ||||||||||||
a: Labels are for information and assistance in ordering.
b: Nominal linear masses (col. 4) are shown for information only.
c: The densities of martensitic chromium steels (L80 Types 9Cr and 13Cr) are different from carbon steels. The masses shown are therefore not accurate for martensitic chromium steels. A mass correction factor of 0.989 may be used.
d: Buttress casing i s available with regualr, special clearance coupings or special clearance couplings with special bevel.
|
API 5CT Chemical Composition and Mechanical Properties
Group | Grade | Type | C | Mn | Mo | Cr | Ni
max |
Cu
max |
P
max |
S
max |
Si
max |
||||
---|---|---|---|---|---|---|---|---|---|---|---|---|---|---|---|
min | max | min | max | min | max | min | max | ||||||||
1 | 2 | 3 | 4 | 5 | 6 | 7 | 8 | 9 | 10 | 11 | 12 | 13 | 14 | 15 | 16 |
1
|
H40
|
–
|
–
|
–
|
–
|
–
|
–
|
–
|
–
|
–
|
–
|
–
|
0.03
|
0.03
|
–
|
J55
|
–
|
–
|
–
|
–
|
–
|
–
|
–
|
–
|
–
|
–
|
–
|
0.03
|
0.03
|
–
|
|
K55
|
–
|
–
|
–
|
–
|
–
|
–
|
–
|
–
|
–
|
–
|
–
|
0.03
|
0.03
|
–
|
|
N80
|
1
|
–
|
–
|
–
|
–
|
–
|
–
|
–
|
–
|
–
|
–
|
0.03
|
0.03
|
–
|
|
N80
|
Q
|
–
|
–
|
–
|
–
|
–
|
–
|
–
|
–
|
–
|
–
|
0.03
|
0.03
|
–
|
|
R95
|
–
|
–
|
0.45 c
|
–
|
1.9
|
–
|
–
|
–
|
–
|
–
|
–
|
0.03
|
0.03
|
0.45
|
|
2
|
M65
|
–
|
–
|
–
|
–
|
–
|
–
|
–
|
–
|
–
|
–
|
–
|
0.03
|
0.03
|
–
|
L80
|
1
|
–
|
0.43 a
|
–
|
1.9
|
–
|
–
|
–
|
–
|
0.25
|
0.35
|
0.03
|
0.03
|
0.45
|
|
L80
|
9Cr
|
–
|
0.15
|
0.3
|
0.6
|
0.9
|
1.1
|
8
|
10
|
0.5
|
0.25
|
0.02
|
0.01
|
1
|
|
L80
|
13Cr
|
0.15
|
0.22
|
0.25
|
1
|
–
|
–
|
12
|
14
|
0.5
|
0.25
|
0.02
|
0.01
|
1
|
|
C90
|
1
|
–
|
0.35
|
–
|
1.2
|
0.25 b
|
0.85
|
–
|
1.5
|
0.99
|
–
|
0.02
|
0.01
|
–
|
|
T95
|
1
|
–
|
0.35
|
–
|
1.2
|
0.25 d
|
0.85
|
0.4
|
1.5
|
0.99
|
–
|
0.02
|
0.01
|
–
|
|
C110
|
–
|
–
|
0.35
|
–
|
1.2
|
0.25
|
1
|
0.4
|
1.5
|
0.99
|
–
|
0.02
|
0.005
|
–
|
|
3
|
P110
|
e
|
–
|
–
|
–
|
–
|
–
|
–
|
–
|
–
|
–
|
–
|
0.030 e
|
0.030 e
|
–
|
4
|
Q125
|
1
|
–
|
0.35
|
1.35
|
–
|
0.85
|
–
|
1.5
|
0.99
|
–
|
0.02
|
0.01
|
–
|
|
a The carbon content for L80 may be increased up to 0.50 % maximum if the product is oil-quenched. b The molybdenum content for Grade C90 Type 1 has no minimum tolerance if the wall thickness is less than 17.78 mm. c The carbon content for R95 may be increased up to 0.55 % maximum if the product is oil-quenched. d The molybdenum content for T95 Type 1 may be decreased to 0.15 % minimum if the wall thickness is less than 17.78 mm. e For EW Grade P110, the phosphorus content shall be 0.020 % maximum and the sulfur content 0.010 % maximum. NL = no limit. Elements shown shall be reported in product analysis. |
CASING PIPE MATERIALS – MECHANICAL PROPERTIES
Group | Grade | Type | Total
elongation under load % |
Yield
strength MPa |
Tensile
strength min. MPa |
Hardness a
max. |
Specified
wall thickness mm |
Allowable
hardness variation b HRC |
||
---|---|---|---|---|---|---|---|---|---|---|
min | max | HRC | HBW | |||||||
1 | 2 | 3 | 4 | 5 | 6 | 7 | 8 | 9 | 10 | 11 |
1 |
H40
|
–
|
0.5
|
276
|
552
|
414
|
–
|
–
|
–
|
–
|
J55
|
–
|
0.5
|
379
|
552
|
517
|
–
|
–
|
–
|
–
|
|
K55
|
–
|
0.5
|
379
|
552
|
655
|
–
|
–
|
–
|
–
|
|
N80
|
1
|
0.5
|
552
|
758
|
689
|
–
|
–
|
–
|
–
|
|
N80
|
Q
|
0.5
|
552
|
758
|
689
|
–
|
–
|
–
|
–
|
|
R95
|
–
|
0.5
|
655
|
758
|
724
|
–
|
–
|
–
|
–
|
|
2 |
M65
|
–
|
0.5
|
448
|
586
|
586
|
22
|
235
|
–
|
–
|
L80
|
1
|
0.5
|
552
|
655
|
655
|
23
|
241
|
–
|
–
|
|
L80
|
9Cr
|
0.5
|
552
|
655
|
655
|
23
|
241
|
–
|
–
|
|
L80
|
13Cr
|
0.5
|
552
|
655
|
655
|
23
|
241
|
–
|
–
|
|
C90
|
1
|
0.5
|
621
|
724
|
689
|
25.4
|
255
|
≤ 12.70
12.71 to 19.04 19.05 to 25.39 ≥ 25.40 |
3.0 4.0 5.0 6.0
|
|
T95
|
1
|
0.5
|
655
|
758
|
724
|
25.4
|
255
|
≤ 12.70
12.71 to 19.04 19.05 to 25.39 ≥ 25.40 |
3.0 4.0 5.0 6.0
|
|
C110
|
–
|
0.7
|
758
|
828
|
793
|
30
|
286
|
≤ 12.70
12.71 to 19.0 19.05 to 25.39 ≥ 25.40 |
3.0 4.0 5.0 6.0
|
|
3 |
P110
|
–
|
0.6
|
758
|
965
|
862
|
–
|
–
|
–
|
–
|
4 |
Q125
|
1
|
0.65
|
862
|
1034
|
931
|
b
|
–
|
≤ 12.70
12.71 to 19.04 ≥ 19.05 |
3.0 4.0 5.0
|
a In case of dispute, laboratory Rockwell C hardness testing shall be used as the referee method. b No hardness limits are specified, but the maximum variation is restricted as a manufacturing control in accordance with 7.8 and 7.9 of API Spec. 5CT. |
Manufacturing Processes
Seamless and Welded Tubing
API 5CT casing and tubing can be manufactured using either seamless or welded processes.
Seamless Process
- Billet Preparation: A solid steel billet is heated and pierced to create a hollow shell.
- Hot Rolling: The hollow shell is rolled to reduce its diameter and wall thickness.
- Cold Drawing (Optional): The tube is cold drawn to achieve precise dimensions and surface finish.
- Heat Treatment: The tube undergoes heat treatment to achieve the required mechanical properties.
- Straightening and Cutting: The tube is straightened and cut to the desired length.
Welded Process
- Strip Preparation: Steel strips are slit to the required width.
- Forming: The strips are formed into a cylindrical shape.
- Welding: The edges of the formed strip are welded together.
- Heat Treatment: The welded tube undergoes heat treatment to achieve the required mechanical properties.
- Sizing and Cutting: The tube is sized and cut to the required length.
Heat Treatment
Heat treatment processes such as quenching and tempering are crucial for achieving the desired mechanical properties.
- Quenching and Tempering: Heating the tube to a high temperature, rapidly cooling (quenching), and reheating to a lower temperature (tempering) to achieve the desired strength and toughness.
Testing Requirements
API 5CT specifies rigorous testing requirements to ensure the quality and performance of casing and tubing:
- Tensile Test: Measures tensile strength, yield strength, and elongation.
- Hardness Test: Ensures the material meets specified hardness levels.
- Impact Test: Assesses the material’s toughness at various temperatures.
- Hydrostatic Test: Ensures the tube can withstand internal pressure without leaking.
- Non-Destructive Testing: Includes ultrasonic, magnetic particle, and radiographic testing to detect any defects.
- Sour Service Testing: Ensures resistance to sulfide stress cracking (SSC) for use in sour environments.
Applications
API 5CT casing and tubing are used in various drilling and production environments, including:
- Standard Oil and Gas Wells: Basic grades for conventional wells.
- Deep Oil and Gas Wells: Higher strength grades for deeper wells.
- High-Pressure, High-Temperature (HPHT) Reservoirs: Ultra-high strength grades for extreme conditions.
- Geothermal Wells: Tubing for high-temperature and high-pressure geothermal applications.
- Offshore Drilling: High-strength casing and tubing for deep-water drilling operations.
Advantages and Limitations
Advantages
- Versatility: Wide range of grades to suit different environments.
- Strength: High mechanical properties ensure reliability in demanding applications.
- Durability: Toughness ensures long-term performance in harsh conditions.
- Availability: Available in both seamless and welded forms.
Limitations
- Cost: Higher grades may be more expensive due to alloying elements and heat treatment processes.
- Manufacturing Complexity: Requires precise control over chemical composition and heat treatment.
- Lead Time: Specific grades and sizes may have longer lead times.
Conclusion
API 5CT casing and tubing are essential components in the oil and gas industry, providing structural integrity and transport pathways within the wellbore. Understanding the detailed specifications, grades, and applications of API 5CT casing and tubing helps engineers and designers select the right materials for their projects, ensuring safety and efficiency in challenging drilling and production operations.
By examining the chemical composition, mechanical properties, manufacturing processes, and applications, this analysis provides a comprehensive overview of API 5CT casing and tubing, highlighting their significance in high-performance industrial applications.