Causes of Well Casing Pipe Damage and Repairing Technology
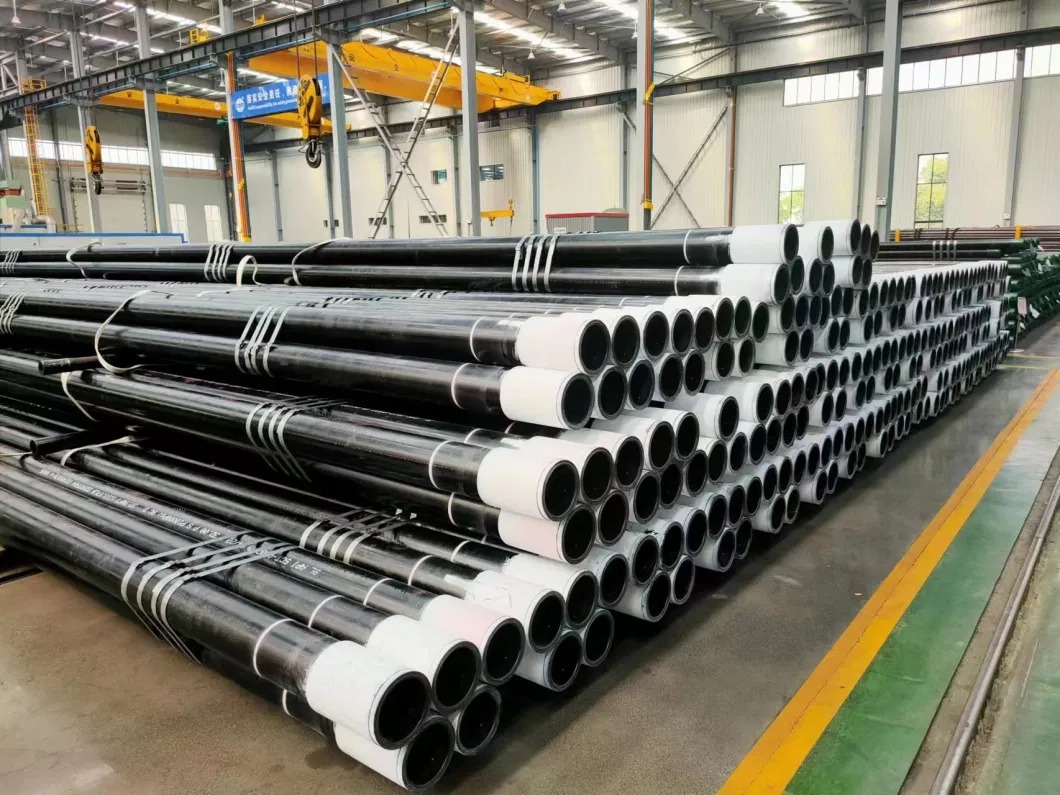
Well casing pipes are critical components in the construction and operation of wells, particularly in the oil and gas industry. They provide structural integrity to the wellbore, prevent contamination of groundwater, and isolate different underground formations. However, these casing pipes can suffer damage due to various factors, which can compromise the efficiency and safety of the well. In this comprehensive exploration, we will delve into the causes of well casing pipe damage and the technologies used to repair them, ensuring the continued functionality and safety of wells.
Causes of Well Casing Pipe Damage
Understanding the causes of well casing pipe damage is essential for implementing effective prevention and repair strategies. Here are some common causes:
- Corrosion:
- Chemical Corrosion: Exposure to corrosive fluids, such as brine or acidic water, can lead to chemical corrosion. This is particularly prevalent in wells that penetrate formations containing corrosive substances.
- Electrochemical Corrosion: Occurs when casing pipes are exposed to electrochemical reactions, often due to the presence of different metals or stray electrical currents.
- Mechanical Stress:
- Overburden Pressure: The weight of the overlying rock layers can exert significant pressure on the casing, leading to deformation or collapse.
- Thermal Stress: Temperature fluctuations, especially in geothermal wells or during thermal recovery processes, can cause expansion and contraction, leading to stress on the casing.
- Improper Installation:
- Poor Cementing: Inadequate cementing can result in gaps between the casing and the wellbore, leading to instability and potential damage.
- Misalignment: Incorrect alignment during installation can cause uneven stress distribution, increasing the risk of damage.
- External Forces:
- Seismic Activity: Earthquakes or other seismic events can cause ground movement, potentially damaging the casing.
- Subsidence: The gradual sinking of the ground can exert additional pressure on the casing, leading to deformation or failure.
- Abrasive Wear:
- Sand and Particulate Matter: The presence of abrasive materials in the fluid being transported can wear down the casing over time, leading to thinning and eventual failure.
- Fatigue:
- Cyclic Loading: Repeated cycles of loading and unloading, such as those experienced during production operations, can lead to fatigue and cracking of the casing material.
Repairing Technologies for Well Casing Pipe Damage
Repairing damaged well casing pipes is crucial for maintaining the integrity and functionality of wells. Various technologies and methods are employed to address different types of damage:
- Casing Patches:
- Slip-On Patches: These are external sleeves that are slipped over the damaged section of the casing. They provide a quick and effective solution for sealing leaks or reinforcing weak areas.
- Expandable Patches: These patches are inserted into the casing and then expanded to fit tightly against the inner wall, providing a secure seal.
- Cement Squeeze:
- Purpose: Used to seal leaks or fill voids in the casing. Cement is pumped into the well and squeezed into the damaged area, creating a solid barrier.
- Application: Effective for repairing small leaks or gaps caused by poor cementing.
- Liner Installation:
- Liner Hangers: A liner is a smaller diameter casing that is hung inside the existing casing. It provides additional support and seals off damaged sections.
- Advantages: Liners can be used to isolate damaged zones without the need to replace the entire casing.
- Resin Injection:
- Epoxy or Polymer Resins: These materials are injected into cracks or voids in the casing to seal leaks and restore structural integrity.
- Benefits: Resins offer good adhesion and can be used in a variety of well conditions.
- Mechanical Repair Tools:
- Casing Expanders: Tools that mechanically expand the casing to restore its original shape and size, often used in conjunction with patches or liners.
- Casing Straighteners: Devices used to realign bent or deformed casing sections.
- Welding and Metal Repair:
- Welding: In some cases, welding can be used to repair cracks or holes in the casing, although this is more challenging in downhole conditions.
- Metal Clamps: Clamps or collars can be used to reinforce damaged sections and prevent further deterioration.
- Advanced Technologies:
- Robotic Inspection and Repair: The use of robotic tools for inspecting and repairing casing damage is becoming more common, offering precision and efficiency.
- Smart Materials: Research into self-healing materials and coatings that can automatically repair minor damage is ongoing, offering potential for future applications.
Preventive Measures and Best Practices
Preventing well casing pipe damage is as important as repairing it. Here are some best practices and preventive measures:
- Material Selection:
- Corrosion-Resistant Alloys: Using materials that are resistant to corrosion can significantly reduce the risk of chemical damage.
- High-Strength Materials: Selecting materials with high tensile strength can help withstand mechanical stress and fatigue.
- Proper Installation:
- Quality Cementing: Ensuring proper cementing during installation can prevent gaps and provide stability to the casing.
- Accurate Alignment: Careful alignment and installation can reduce uneven stress distribution and potential damage.
- Regular Inspection and Maintenance:
- Inspection Tools: Utilizing tools such as calipers, ultrasonic testing, and downhole cameras for regular inspections can help identify early signs of damage.
- Preventive Maintenance: Implementing a maintenance schedule can address minor issues before they escalate into major problems.
- Monitoring and Control:
- Pressure and Temperature Monitoring: Keeping track of pressure and temperature changes can help identify conditions that may lead to casing damage.
- Seismic Monitoring: In areas prone to seismic activity, monitoring ground movement can help anticipate and mitigate potential damage.
- Operational Adjustments:
- Controlled Production Rates: Avoiding sudden changes in production rates can reduce cyclic loading and fatigue.
- Sand Control: Implementing measures to control sand and particulate matter can minimize abrasive wear.