Difference Between 3LPP and 3PE Steel Pipeline Coatings
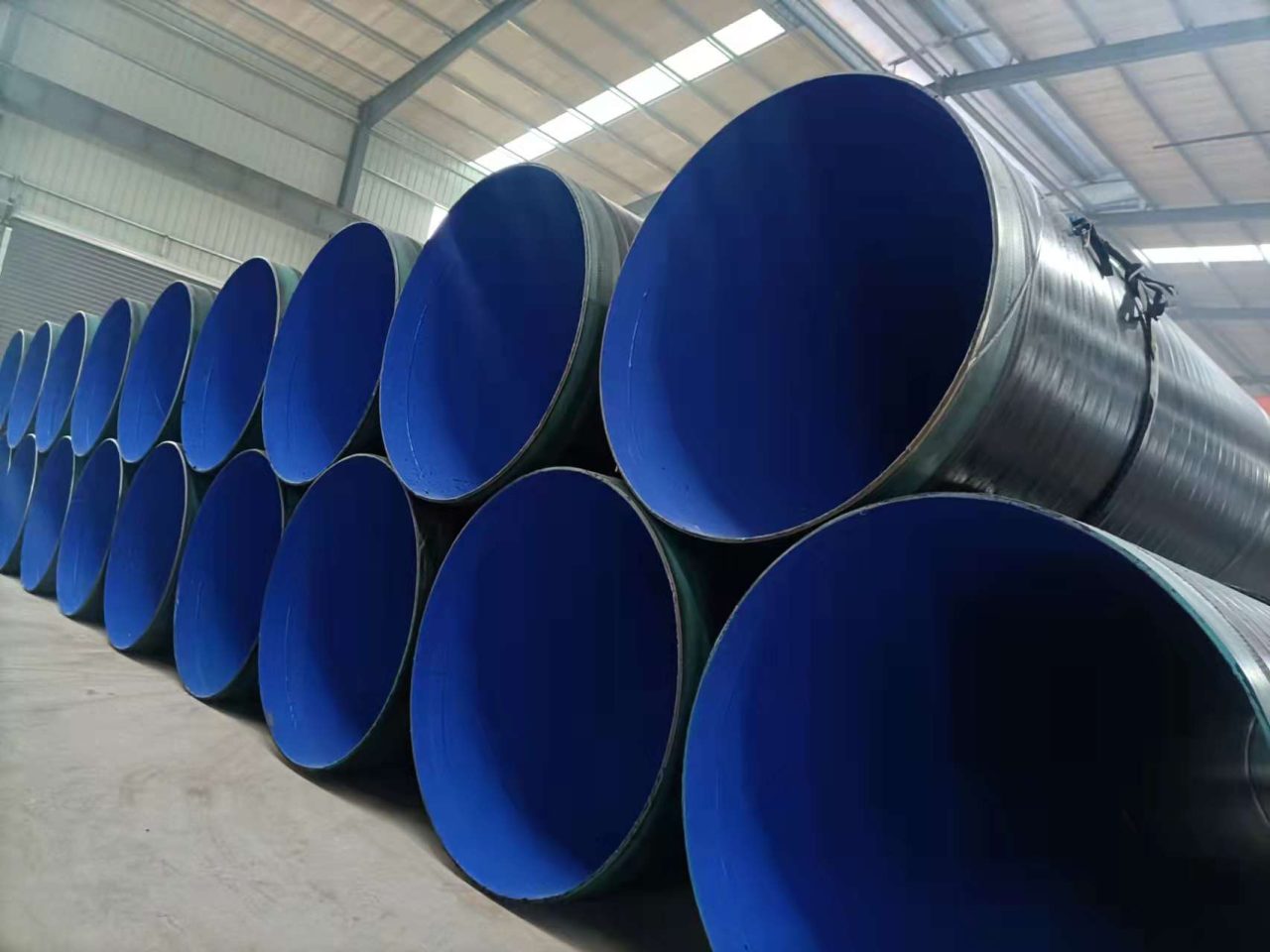
Difference Between 3LPP and 3PE Steel Pipeline Coatings
Introduction
Steel pipelines are widely used in industries such as oil and gas, water distribution, and chemical processing for transporting fluids over long distances. To ensure the longevity and integrity of these pipelines, they are often coated with protective layers that prevent corrosion, abrasion, and mechanical damage. Two of the most common coating systems used for steel pipelines are 3LPP (Three-Layer Polypropylene) and 3PE (Three-Layer Polyethylene).
Both 3LPP and 3PE coatings provide excellent protection against corrosion and environmental factors, but they have distinct differences in terms of material composition, performance characteristics, and applications. In this article, we will explore the differences between 3LPP and 3PE coatings, their advantages, and the specific conditions under which each coating is preferred.
Table of Contents
- What Is 3LPP Coating?
- What Is 3PE Coating?
- Key Differences Between 3LPP and 3PE Coatings
- Applications of 3LPP and 3PE Coatings
- Advantages of 3LPP and 3PE Coatings
- Frequently Asked Questions (FAQ)
- Conclusion
What Is 3LPP Coating? {#what-is-3lpp-coating}
3LPP (Three-Layer Polypropylene) is a three-layer coating system that is used to protect steel pipelines from corrosion, mechanical damage, and abrasion. The 3LPP system consists of the following layers:
- Fusion Bonded Epoxy (FBE) Layer: This is the first layer, which provides excellent adhesion to the steel surface and acts as a primary corrosion protection barrier. The FBE layer also offers good resistance to chemical attack and cathodic disbondment.
- Adhesive Layer: The second layer is a copolymer adhesive that bonds the FBE layer to the outer polypropylene layer. This adhesive ensures strong adhesion between the layers and enhances the overall durability of the coating.
- Polypropylene (PP) Layer: The outermost layer is made of polypropylene, which provides excellent resistance to mechanical damage, abrasion, and high temperatures. Polypropylene is known for its high tensile strength and impact resistance, making it ideal for pipelines exposed to harsh environmental conditions.
Key Features of 3LPP Coating:
- High-temperature resistance: 3LPP coatings can withstand temperatures up to 110°C or higher, making them suitable for pipelines transporting hot fluids.
- Excellent mechanical protection: The polypropylene layer provides superior resistance to abrasion, impact, and mechanical stresses.
- Long-term corrosion protection: The FBE layer offers excellent protection against corrosion and chemical attack, ensuring the longevity of the pipeline.
What Is 3PE Coating? {#what-is-3pe-coating}
3PE (Three-Layer Polyethylene) is another three-layer coating system used to protect steel pipelines from corrosion and mechanical damage. The 3PE system consists of the following layers:
- Fusion Bonded Epoxy (FBE) Layer: Similar to 3LPP, the first layer in the 3PE system is a fusion bonded epoxy that provides excellent adhesion to the steel surface and acts as a primary corrosion protection barrier.
- Adhesive Layer: The second layer is a copolymer adhesive that bonds the FBE layer to the outer polyethylene layer. This adhesive ensures strong adhesion between the layers and enhances the overall durability of the coating.
- Polyethylene (PE) Layer: The outermost layer is made of polyethylene, which provides good resistance to mechanical damage, abrasion, and corrosion. Polyethylene is known for its flexibility and low-temperature resistance, making it suitable for pipelines in colder environments.
Key Features of 3PE Coating:
- Moderate temperature resistance: 3PE coatings can typically withstand temperatures up to 80°C, making them suitable for pipelines transporting moderately hot fluids.
- Good mechanical protection: The polyethylene layer provides adequate resistance to abrasion and mechanical stresses, though it is not as strong as polypropylene.
- Corrosion protection: The FBE layer in 3PE coatings offers excellent protection against corrosion, ensuring the long-term performance of the pipeline.
Key Differences Between 3LPP and 3PE Coatings {#key-differences-between-3lpp-and-3pe-coatings}
While both 3LPP and 3PE coatings provide excellent protection for steel pipelines, they differ in several key aspects, including temperature resistance, mechanical strength, and flexibility.
1. Temperature Resistance
- 3LPP: The polypropylene outer layer in 3LPP coatings provides high-temperature resistance, typically up to 110°C or higher. This makes 3LPP suitable for pipelines transporting hot fluids or operating in high-temperature environments.
- 3PE: The polyethylene outer layer in 3PE coatings offers moderate temperature resistance, typically up to 80°C. This makes 3PE suitable for pipelines transporting moderately hot fluids or operating in temperate environments.
2. Mechanical Strength
- 3LPP: The polypropylene layer in 3LPP coatings provides superior mechanical strength, including resistance to impact, abrasion, and mechanical stresses. This makes 3LPP ideal for pipelines exposed to harsh environmental conditions or mechanical loads.
- 3PE: The polyethylene layer in 3PE coatings provides good mechanical protection, but it is not as strong as polypropylene. 3PE is more suitable for pipelines in environments with less mechanical stress.
3. Flexibility
- 3LPP: Polypropylene is a rigid material, which means that 3LPP coatings are less flexible than 3PE coatings. This makes 3LPP more suitable for straight pipelines or applications where flexibility is not a primary concern.
- 3PE: Polyethylene is a more flexible material compared to polypropylene, making 3PE coatings ideal for pipelines that require flexibility, such as those in bending or curved sections.
4. Cost
-
- 3LPP: Due to its higher temperature resistance and superior mechanical properties, 3LPP coatings are generally more expensive than 3PE coatings. However, the additional cost is justified in applications where high performance is required.
- 3PE: 3PE coatings are typically more cost-effective than 3LPP coatings, making them a popular choice for pipelines in moderate environments where extreme temperatures or mechanical loads are not a concern.
5. Applications
- 3LPP: 3LPP coatings are preferred for pipelines in high-temperature environments, such as oil and gas pipelines transporting hot fluids, or in areas where mechanical protection is critical, such as offshore pipelines.
- 3PE: 3PE coatings are commonly used in pipelines operating in moderate environments, such as water distribution systems, natural gas pipelines, and onshore pipelines where temperature and mechanical stress are lower.
Applications of 3LPP and 3PE Coatings {#applications-of-3lpp-and-3pe-coatings}
Both 3LPP and 3PE coatings are widely used in various industries, but their specific applications depend on the operating conditions and environmental factors.
Common Applications of 3LPP Coatings:
- Oil and gas pipelines: 3LPP coatings are ideal for oil and gas pipelines that transport hot fluids or operate in high-temperature environments.
- Offshore pipelines: Due to its superior mechanical strength and abrasion resistance, 3LPP is commonly used in offshore pipelines where the pipeline is exposed to harsh environmental conditions and mechanical loads.
- High-temperature applications: 3LPP is suitable for pipelines that operate at temperatures up to 110°C or higher, such as steam lines or hot water pipelines.
Common Applications of 3PE Coatings:
- Water distribution pipelines: 3PE coatings are commonly used in water distribution systems, where the pipeline operates at moderate temperatures and requires protection against corrosion and mechanical damage.
- Natural gas pipelines: 3PE is widely used in natural gas pipelines due to its cost-effectiveness and good corrosion resistance.
- Onshore pipelines: 3PE coatings are suitable for onshore pipelines where the operating conditions are less demanding in terms of temperature and mechanical stress.
Advantages of 3LPP and 3PE Coatings {#advantages-of-3lpp-and-3pe-coatings}
Advantages of 3LPP Coatings:
- High-temperature resistance: 3LPP coatings can withstand temperatures up to 110°C or higher, making them ideal for pipelines transporting hot fluids.
- Superior mechanical protection: The polypropylene layer provides excellent resistance to abrasion, impact, and mechanical damage, ensuring the longevity of the pipeline.
- Long-term corrosion protection: The FBE layer offers excellent protection against corrosion, ensuring the pipeline’s durability in aggressive environments.
Advantages of 3PE Coatings:
- Cost-effective: 3PE coatings are generally more affordable than 3LPP coatings, making them a popular choice for pipelines in moderate environments.
- Good flexibility: The polyethylene layer provides greater flexibility, making 3PE suitable for pipelines that require bending or curved sections.
- Adequate corrosion protection: The FBE layer in 3PE coatings offers good protection against corrosion, ensuring the pipeline’s long-term performance.
Frequently Asked Questions (FAQ) {#faq}
1. What is the main difference between 3LPP and 3PE coatings?
The main difference between 3LPP and 3PE coatings is the outer layer material. 3LPP uses polypropylene, which provides higher temperature resistance and superior mechanical protection, while 3PE uses polyethylene, which offers moderate temperature resistance and greater flexibility.
2. Which coating is better for high-temperature applications?
3LPP is better suited for high-temperature applications, as it can withstand temperatures up to 110°C or higher. 3PE, on the other hand, is limited to temperatures of around 80°C.
3. Is 3LPP more expensive than 3PE?
Yes, 3LPP coatings are generally more expensive than 3PE coatings due to their higher performance in terms of temperature resistance and mechanical strength.
4. Can 3PE coatings be used in offshore pipelines?
While 3PE coatings can be used in offshore pipelines, 3LPP is often preferred due to its superior mechanical protection and ability to withstand harsh environmental conditions.
5. What are the typical applications of 3PE coatings?
3PE coatings are commonly used in water distribution systems, natural gas pipelines, and onshore pipelines where the operating conditions are less demanding in terms of temperature and mechanical stress.