Liquid-Epoxy Coatings and Linings for Steel Water Pipes and Fittings
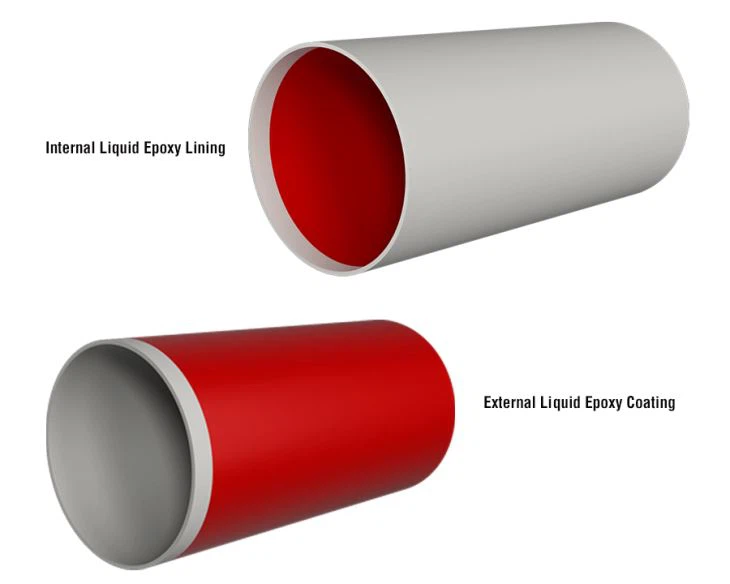
Comprehensive Outline: Liquid-Epoxy Coatings and Linings for Steel Water Pipes and Fittings
Main Topic | Subtopics |
---|---|
H1: Introduction to Liquid-Epoxy Coatings and Linings | – Importance of coatings and linings for steel water pipes – Overview of liquid-epoxy coatings – Applications in water infrastructure |
H2: Materials Used in Liquid-Epoxy Coatings | – Primary components of liquid-epoxy coatings – Chemical composition and benefits – Standards and certifications (AWWA, NSF, etc.) |
H2: Types of Liquid-Epoxy Coatings for Steel Pipes | – Single-component epoxy coatings – Two-component epoxy coatings – Specialty epoxy coatings for harsh environments |
H2: Application Process for Liquid-Epoxy Coatings | – Surface preparation methods (sandblasting, chemical cleaning) – Application techniques (spray, brush, or dip) – Curing and drying times |
H3: Surface Preparation Requirements | – Why surface preparation is critical – Common standards (e.g., SSPC, NACE) – Handling rust, scale, and contaminants |
H3: Application Equipment and Tools | – Spray equipment for liquid-epoxy coatings – Tools for small fittings and tight spaces – Safety equipment for handling epoxy |
H2: Inspection and Quality Control | – Visual inspections during and after application – Thickness measurement standards (e.g., dry film thickness) – Adhesion testing methods |
H2: Testing Requirements for Liquid-Epoxy Coatings | – Laboratory testing (chemical resistance, tensile strength) – Field testing methods (e.g., holiday testing) – Standards for testing (ASTM, ISO) |
H2: Performance Requirements of Coatings and Linings | – Long-term corrosion resistance – Water quality compatibility (NSF certifications) – Resistance to mechanical damage |
H3: Environmental and Regulatory Considerations | – Compliance with environmental standards (VOC limits, LEED credits) – Safe disposal of unused material |
H2: Packaging and Storage Requirements | – Proper packaging of liquid-epoxy coatings to prevent contamination – Storage temperature and humidity controls – Shelf life and expiration considerations |
H2: Advantages of Using Liquid-Epoxy Coatings | – Durability and long service life – Reduced maintenance costs – Eco-friendly options compared to traditional coatings |
H2: Challenges and Limitations of Liquid-Epoxy Coatings | – Sensitivity to application errors – Cost considerations for large-scale projects – Performance under extreme conditions |
H2: Common Applications in Water Systems | – Coating large-diameter steel water mains – Use in potable water systems – Applications for wastewater infrastructure |
H2: Innovations in Liquid-Epoxy Technology | – Recent advancements in epoxy formulations – Faster curing times – Improved resistance to chemical exposure |
H2: Cost Considerations for Liquid-Epoxy Coatings | – Material and labor costs – Factors influencing cost (pipe size, surface condition) – Comparing epoxy coatings to alternative options |
H2: Industry Standards and Certifications | – Key certifications for water system coatings (AWWA, ISO, NSF) – Adhering to government and industry requirements – Importance of third-party testing and certification |
H2: Frequently Asked Questions (FAQs) | – How long do liquid-epoxy coatings last on steel water pipes? – Are liquid-epoxy coatings safe for potable water systems? – How are epoxy coatings tested for durability? – Can epoxy coatings be repaired if damaged? – What is the cost of applying liquid-epoxy coatings? – Are epoxy coatings eco-friendly? |
LE Liquid Epoxy Coating and Lining, this application uses a two-part liquid epoxy paint system applied in a single coat in anticorrosion protection for steel pipes. The first process the pipes go through are cleaned & blasted. Then liquid epoxy is applied to the pipe surface by spray guns, forming a uniform single layer epoxy which cures after application.
The codes and standards for Liquid-Epoxy Coating is AWWA C210, SHELL DEP 31.40.30.35, EN 10301, ISO 15741, API RP 5L2
AWWA C210 Standard for Liquid-Epoxy Coating Systems for the Interior and Exterior of Steel Water Pipelines
SHELL DEP 31.40.30.35 Internal coating of line pipe for non-corrosive gas transmission service
EN 10301:2006 STEEL TUBES AND FITTINGS FOR ON AND OFFSHORE PIPELINES – INTERNAL COATING FOR THE REDUCTION OF FRICTION FOR CONVEYANCE OF NON-CORROSIVE GAS
ISO 15741:2016 Paints and varnishes — Friction-reduction coatings for the interior of on- and offshore steel pipelines for non-corrosive gases
Long-Form Article: Liquid-Epoxy Coatings and Linings for Steel Water Pipes and Fittings
H1: Introduction to Liquid-Epoxy Coatings and Linings
In the realm of water infrastructure, protecting steel water pipes and fittings from corrosion and environmental wear is critical. Liquid-epoxy coatings and linings have emerged as one of the most effective solutions for safeguarding water systems. These coatings provide a durable, corrosion-resistant barrier that ensures the longevity and efficiency of steel pipes used for potable water, wastewater, and industrial applications.
This article delves into the materials, application methods, inspection protocols, testing requirements, and performance standards associated with liquid-epoxy coatings for steel water pipes. Whether you’re a project manager, engineer, or contractor, understanding the intricacies of this technology is vital for maintaining water system integrity.
H2: Materials Used in Liquid-Epoxy Coatings
Liquid-epoxy coatings are formulated with high-performance materials designed to withstand water exposure, temperature fluctuations, and environmental stresses. The primary components include:
- Epoxy Resin: The main binder responsible for adhesion and chemical resistance.
- Curing Agents: These activate the hardening process, ensuring durability and strength.
- Additives: Enhance properties like UV resistance, flexibility, or anti-corrosion capabilities.
- Pigments: Provide color and additional UV protection.
To ensure quality, epoxy coatings must meet standards such as AWWA C210 for potable water systems and NSF/ANSI 61 for safe use in drinking water applications.
H2: Types of Liquid-Epoxy Coatings for Steel Pipes
- Single-Component Epoxy Coatings: Ready-to-use formulations requiring no mixing. Ideal for smaller projects or touch-ups.
- Two-Component Epoxy Coatings: Require precise mixing of resin and hardener. These are the most widely used for large-scale projects due to their superior durability.
- Specialty Epoxy Coatings: Engineered for extreme environments, such as high-temperature or chemically aggressive conditions.
H2: Application Process for Liquid-Epoxy Coatings
The performance of liquid-epoxy coatings depends heavily on proper application. The key steps include:
- Surface Preparation: The steel surface must be free from rust, scale, and contaminants. Abrasive blasting to a near-white metal finish is often required to meet SSPC-SP10/NACE No. 2 standards.
- Application: Using spray, brush, or dip methods, the coating is applied evenly across the surface. Thickness is crucial and must comply with the specifications outlined in standards like ISO 2808.
- Curing: Adequate curing time ensures the coating achieves its full strength and adhesion properties.
H3: Surface Preparation Requirements
Surface preparation is vital for ensuring the coating adheres effectively. The process involves:
- Cleaning: Removing oil, grease, and other contaminants.
- Abrasive Blasting: Achieving the required profile for the epoxy to bond securely.
- Inspection: Ensuring all rust and debris have been eliminated.
H2: Inspection and Quality Control
Inspection plays a crucial role in guaranteeing the performance of epoxy coatings. The process includes:
- Visual Inspection: Checking for defects like pinholes or uneven coverage.
- Dry Film Thickness (DFT) Measurement: Ensuring the coating meets the specified thickness, typically measured in microns.
- Adhesion Testing: Evaluating how well the coating bonds to the steel surface.
H2: Testing Requirements for Liquid-Epoxy Coatings
To verify the effectiveness of the coating, several tests are conducted:
- Holiday Testing: Detects pinholes and voids in the coating.
- Chemical Resistance Testing: Measures the coating’s ability to resist water, acids, and other substances.
- Impact Resistance Testing: Ensures the coating can withstand mechanical stress during installation and use.
H2: Performance Requirements of Coatings and Linings
Liquid-epoxy coatings are designed to provide:
- Corrosion Resistance: Protecting steel from rust and chemical attack.
- Water Quality Safety: Ensuring no leaching of harmful substances into potable water.
- Durability: Withstanding mechanical damage and environmental stresses.
H2: Packaging and Storage Requirements
To maintain the quality of liquid-epoxy coatings:
- Packaging: Materials must be sealed in moisture-proof containers.
- Storage: Kept in temperature-controlled environments, typically between 10°C and 30°C.
- Shelf Life: Ensuring the material is used within the manufacturer’s specified timeframe.
H2: Advantages of Using Liquid-Epoxy Coatings
Liquid-epoxy coatings offer numerous advantages, making them a preferred choice for steel water pipes and fittings. These include:
-
Superior Corrosion Resistance:
Epoxy coatings create a robust barrier that prevents rust and degradation, ensuring a long lifespan for steel pipes. -
Durability in Harsh Environments:
Liquid-epoxy coatings withstand extreme temperatures, chemical exposure, and mechanical stress, making them suitable for a wide range of applications. -
Reduced Maintenance Costs:
With a service life of up to 50 years, these coatings minimize the need for frequent maintenance and repairs, saving both time and money. -
Eco-Friendly Options:
Modern formulations feature low volatile organic compound (VOC) content, which reduces environmental impact and complies with strict environmental regulations. -
Ease of Application:
Epoxy coatings can be applied using simple methods such as spraying, brushing, or dipping, making them versatile for different project sizes and conditions. -
Safe for Potable Water Systems:
Certified coatings (e.g., NSF/ANSI 61) are non-toxic and safe for use in drinking water pipelines.
H2: Challenges and Limitations of Liquid-Epoxy Coatings
Despite their many benefits, liquid-epoxy coatings do have some challenges and limitations:
-
Application Sensitivity:
Proper surface preparation and precise application are essential to achieve optimal performance. Inadequate preparation can lead to coating failure. -
Cost Considerations:
While epoxy coatings offer long-term savings, their upfront costs can be higher than alternative coatings. -
Limited Performance in Extreme UV Exposure:
Some epoxy formulations may degrade when exposed to prolonged sunlight unless UV-resistant additives are included. -
Curing Time Constraints:
Epoxy coatings require sufficient time to cure fully. In cold or humid environments, curing times may increase, potentially delaying projects. -
Potential for Cracking:
In applications subject to significant structural movement or thermal expansion, epoxy coatings may be prone to cracking if not formulated with flexibility in mind.
H2: Common Applications in Water Systems
Liquid-epoxy coatings and linings are widely used in various water system applications, including:
-
Potable Water Pipelines:
Ensuring water safety and preventing corrosion in drinking water systems. -
Wastewater Infrastructure:
Providing protection against chemical exposure and abrasion in wastewater treatment plants. -
Large-Diameter Steel Pipes:
Coating pipelines for water distribution and transmission to extend their lifespan. -
Fittings and Valves:
Epoxy coatings protect smaller components such as fittings, couplings, and valves from corrosion and wear. -
Underground Pipelines:
Offering resistance against soil corrosion and mechanical damage during installation.
H2: Innovations in Liquid-Epoxy Technology
The field of liquid-epoxy coatings continues to evolve with new advancements aimed at improving performance and sustainability. Recent innovations include:
-
Faster Curing Times:
New formulations have been developed to significantly reduce curing time, allowing for faster project completion. -
Improved Chemical Resistance:
Advances in epoxy chemistry have enhanced resistance to aggressive chemicals, making these coatings ideal for industrial applications. -
Self-Healing Coatings:
Cutting-edge technology is being developed to create coatings that can “heal” minor damage, ensuring long-term performance without repair. -
Eco-Friendly Formulations:
Modern epoxy coatings feature low-VOC or VOC-free formulations, meeting stringent environmental standards while maintaining high performance. -
Smart Coatings:
These coatings incorporate sensors or indicators to detect issues like corrosion or damage, enabling proactive maintenance.
H2: Cost Considerations for Liquid-Epoxy Coatings
The cost of liquid-epoxy coatings depends on several factors:
-
Material Costs:
The type and quality of epoxy coating can affect pricing. Specialty coatings for extreme environments are typically more expensive. -
Surface Preparation:
Proper surface preparation, such as abrasive blasting, adds to the overall cost but is essential for achieving optimal results. -
Labor Costs:
The application process requires skilled workers to ensure compliance with industry standards, which can increase labor expenses. -
Scale of the Project:
Large-scale pipeline projects may benefit from economies of scale, reducing the cost per unit of coated surface. -
Comparison with Alternatives:
While epoxy coatings may have a higher upfront cost compared to other coatings, their long-term durability and low maintenance requirements often make them more cost-effective.
H2: Industry Standards and Certifications
To ensure the quality and performance of liquid-epoxy coatings, it is essential to comply with industry standards and certifications. Key certifications include:
-
AWWA Standards:
The American Water Works Association (AWWA) provides guidelines for the application and performance of epoxy coatings, such as AWWA C210. -
NSF/ANSI 61 Certification:
This certification ensures that epoxy coatings are safe for use in potable water systems. -
ISO Standards:
International standards, such as ISO 12944, outline requirements for corrosion protection and coating performance. -
ASTM Standards:
ASTM International provides testing standards, such as ASTM D4541 for adhesion testing and ASTM G14 for impact resistance.
Compliance with these standards ensures that coatings meet the rigorous demands of water infrastructure applications.
Advantages of Liquid Epoxy Coatings
Liquid epoxy coatings have revolutionized the steel water pipe industry by offering superior performance and durability. Here are the key benefits:
- Corrosion Resistance
Epoxy coatings prevent rust and corrosion by isolating steel from water and oxygen, ensuring long-term structural integrity. - Longevity
These coatings can extend the life of steel water pipes by several decades, minimizing maintenance and replacement costs. - Safe for Water Systems
Epoxy coatings certified under NSF/ANSI 61 are safe for potable water applications, ensuring no harmful chemicals leach into the water supply. - Improved Water Flow
The smooth, frictionless surface of epoxy linings reduces pressure losses and improves flow efficiency in pipelines. - Versatility
Applicable for both internal linings and external coatings, they are suitable for diverse environmental conditions.
Application Process
Applying liquid epoxy coatings requires precision and adherence to industry standards to ensure effectiveness.
1. Surface Preparation
Proper surface preparation is crucial for achieving adhesion and coating durability:
Method | Purpose |
---|---|
Abrasive Blasting | Removes rust, contaminants, and old coatings while roughening the surface for adhesion. |
Cleaning with Solvents | Eliminates grease, oil, and dirt to ensure a clean substrate. |
Drying | Ensures no moisture remains, as it can affect the curing process. |
2. Coating Application
Application Method | Details |
---|---|
Spraying | Ensures uniform application over large areas. |
Brushing or Rolling | Suitable for small areas or touch-up work. |
Multiple Coats | Applied to achieve the required dry film thickness (DFT). |
3. Curing Process
Curing transforms the liquid epoxy into a hardened, protective barrier. Controlled temperature and humidity are essential for proper curing. Accelerated curing methods may involve external heat sources.
Inspection and Testing Procedures
Inspection ensures that epoxy coatings meet performance requirements. Common tests include:
Inspection Type | Purpose |
---|---|
Visual Inspection | Checks for defects like pinholes, uneven coverage, and air bubbles. |
Dry Film Thickness (DFT) | Measures the coating thickness to meet project specifications. |
Adhesion Testing | Assesses how well the coating adheres to the steel surface. |
Holiday Testing | Detects voids or pinholes using a high-voltage spark tester. |
Inspection Frequency
- During and after application to ensure compliance with standards like ISO 12944 or AWWA C213.
Performance Standards for Epoxy Coatings
Epoxy coatings must meet stringent standards to perform effectively.
Standard | Description |
---|---|
AWWA C210 | Governs liquid epoxy coatings for steel water pipes. |
NSF/ANSI 61 | Certifies coatings safe for potable water use. |
ISO 12944 | Outlines corrosion protection requirements for industrial coatings. |
ASTM D4541 | Specifies pull-off strength testing for adhesion evaluation. |
Packaging and Storage Requirements
Proper handling and storage are essential to maintain the quality of liquid epoxy coatings.
Requirement | Details |
---|---|
Packaging | Coatings are stored in sealed containers to prevent contamination and evaporation. |
Storage Conditions | Store in cool, dry areas away from direct sunlight and extreme temperatures. |
Shelf Life | Follow manufacturer’s guidelines to avoid using expired products. |
Transport Requirements | Ensure proper handling to avoid spills or exposure to air. |
Challenges and Solutions in Application
Challenge | Solution |
---|---|
Poor Adhesion | Improve surface preparation and ensure surfaces are clean and dry before application. |
Uneven Coating Thickness | Use advanced spray equipment and monitor application closely. |
Environmental Conditions | Control temperature and humidity during application and curing. |
Compliance Issues | Ensure applicators are trained and coatings meet industry certifications. |
H2: Frequently Asked Questions (FAQs)
1. How long do liquid-epoxy coatings last on steel water pipes?
Properly applied and maintained liquid-epoxy coatings can last anywhere from 20 to 50 years, depending on environmental conditions and usage.
2. Are liquid-epoxy coatings safe for potable water systems?
Yes, most liquid-epoxy coatings are certified to NSF/ANSI 61, making them safe for use in drinking water systems.
3. How are epoxy coatings tested for durability?
Common tests include holiday testing for pinholes, chemical resistance testing, and adhesion testing to ensure long-term performance.
4. Can epoxy coatings be repaired if damaged?
Yes, epoxy coatings can be repaired through localized surface preparation and re-application of the coating material.
5. What is the cost of applying liquid-epoxy coatings?
Costs vary depending on factors such as the size of the project, surface preparation requirements, and coating type. While initially higher, they offer long-term savings due to their durability.
6. Are epoxy coatings eco-friendly?
Many modern epoxy coatings have low-VOC or VOC-free formulations, making them environmentally friendly and compliant with strict regulations.