Inconel X-750 UNS N07750 Nickel Alloy Pipe VS nickel alloy 600 Steel Pipe
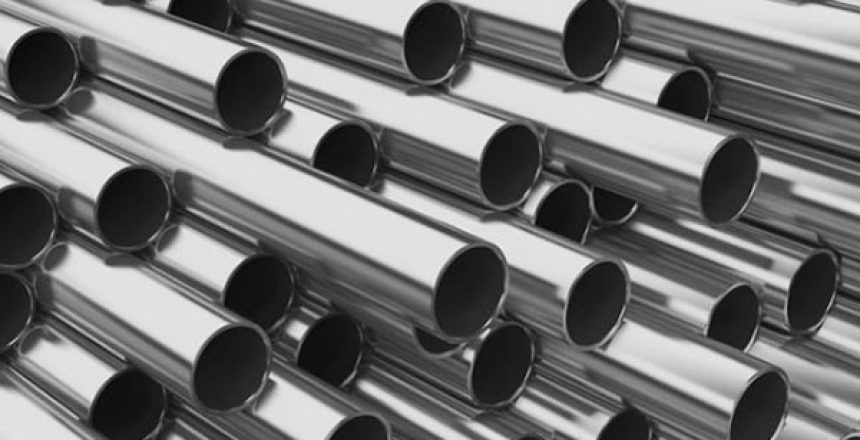
Inconel® X-750 UNS N07750 Nickel Alloy Pipe vs. Nickel Alloy 600 Steel Pipe
Inconel® X-750 (UNS N07750) and Nickel Alloy 600 are two widely used nickel-based alloys that exhibit superior properties such as high strength, excellent corrosion resistance, and performance under extreme environments. While both materials belong to the nickel alloy family, they have distinct chemical compositions, mechanical properties, and specific applications. Below, we compare these two alloys in detail to help you understand their differences and ideal applications.
1. Chemical Composition
The chemical composition of these two alloys defines their properties and performance in specific applications.
Inconel® X-750 (UNS N07750)
- Primary Components:
- Nickel (70%)
- Chromium (15-17%)
- Iron (5-9%)
- Other Elements: Aluminum (0.4-1.0%), Titanium (2.25-2.75%), and Niobium
- Key Feature:
Inconel X-750 is precipitation-hardened using aluminum and titanium, giving it excellent strength and stability at high temperatures.
Nickel Alloy 600
- Primary Components:
- Nickel (72%)
- Chromium (14-17%)
- Iron (6-10%)
- Trace amounts of manganese, silicon, and copper.
- Key Feature:
Nickel Alloy 600 is solid-solution strengthened, making it resistant to oxidation and corrosion in a variety of environments, including chemical processing and heat exposure.
Comparison Summary:
- Both alloys have similar amounts of nickel and chromium, but Inconel X-750 includes aluminum, titanium, and niobium for precipitation hardening, providing enhanced strength and creep resistance.
- Nickel Alloy 600 has a simpler composition and relies more on its inherent toughness and corrosion resistance.
2. Mechanical Properties
Inconel® X-750
- Yield Strength: 620–830 MPa (depending on heat treatment and aging conditions)
- Tensile Strength: 950–1350 MPa
- Elongation: 15–25%
- Operating Temperature: Up to 980°C (1800°F)
- Notable Feature:
Precipitation hardening makes Inconel X-750 ideal for high-stress, high-temperature environments.
Nickel Alloy 600
- Yield Strength: 240–450 MPa (depending on processing)
- Tensile Strength: 550–690 MPa
- Elongation: 40–55%
- Operating Temperature: Up to 1093°C (2000°F)
- Notable Feature:
While it has lower strength compared to Inconel X-750, its ductility and toughness are superior, making it easier to machine and weld.
Comparison Summary:
- Inconel X-750 exhibits higher tensile and yield strength due to its precipitation-hardening mechanism. It is better suited for applications requiring high strength and structural stability at elevated temperatures.
- Nickel Alloy 600 offers greater ductility and toughness, making it versatile and easier to process in less-demanding applications.
3. Corrosion Resistance
Inconel® X-750
- Excellent resistance to oxidation and corrosion at elevated temperatures.
- Suitable for both oxidizing and reducing environments.
- Performs well in stress-corrosion cracking conditions, especially in nuclear applications.
- Resistant to chloride-ion stress corrosion cracking.
Nickel Alloy 600
- Outstanding resistance to a wide range of corrosive environments, including:
- Chloride-ion stress corrosion.
- High-temperature oxidation.
- Sulfuric, hydrochloric, and nitric acids.
- Performs well in both oxidizing and reducing conditions, as well as alkaline environments.
Comparison Summary:
- Both alloys offer excellent corrosion resistance, but Nickel Alloy 600 is slightly more versatile for general chemical and corrosion resistance in a broader range of applications.
- Inconel X-750, with its higher strength, performs better in extreme stress and temperature conditions that involve corrosion.
4. High-Temperature Performance
Inconel® X-750
- Engineered specifically for high-temperature applications.
- Maintains strength and oxidation resistance up to 980°C (1800°F).
- Excellent for prolonged exposure to extreme temperatures due to creep resistance.
- Commonly used in gas turbines, jet engines, and nuclear reactor springs.
Nickel Alloy 600
- Withstands temperatures up to 1093°C (2000°F).
- Retains excellent corrosion resistance and oxidation resistance at high temperatures but has lower mechanical strength than Inconel X-750.
- Commonly used in furnace components, heat exchangers, and chemical reactors.
Comparison Summary:
- Inconel X-750 is better suited for high-stress environments with prolonged exposure to extreme temperatures due to its superior mechanical strength and creep resistance.
- Nickel Alloy 600 offers excellent resistance to oxidation and corrosion at higher temperatures but may not sustain high mechanical loads.
5. Weldability and Machinability
Inconel® X-750
- Difficult to machine due to work-hardening properties.
- Requires specialized tools and machining parameters.
- Weldability is limited and challenging due to its precipitation-hardening mechanism, requiring pre- and post-weld heat treatments to prevent cracking.
Nickel Alloy 600
- Easier to machine compared to Inconel X-750.
- Excellent weldability with no requirement for pre- or post-weld heat treatment.
- Commonly used in applications requiring fabricated components.
Comparison Summary:
- Nickel Alloy 600 is more machinable and weldable, making it a preferred choice for applications where complex fabrications are required.
- Inconel X-750, while harder to process, offers superior performance in high-stress applications.
6. Applications
Inconel® X-750
- Gas turbine blades, nozzles, and combustors.
- Springs and fasteners in nuclear reactors.
- Aerospace engine components requiring high strength and fatigue resistance.
- Components in industrial furnaces and high-temperature fixtures.
Nickel Alloy 600
- Heat exchangers, chemical reactors, and furnace components.
- Tubing in steam generators.
- Components in food processing, marine environments, and petrochemical industries.
- General-purpose applications where corrosion resistance is critical but extreme mechanical strength is not required.
Comparison Summary:
- Inconel X-750 is designed for highly demanding applications involving stress, high temperatures, and fatigue resistance.
- Nickel Alloy 600 is more suitable for general-purpose corrosion-resistant applications in chemical and high-temperature environments.
7. Cost and Availability
Inconel® X-750
- Generally more expensive due to its complex composition and precipitation-hardening process.
- Availability may be limited to specific suppliers specializing in aerospace or nuclear-grade alloys.
Nickel Alloy 600
- More cost-effective compared to Inconel X-750.
- Readily available from a wide range of suppliers due to its extensive use in industrial and commercial applications.
Comparison Summary:
- Nickel Alloy 600 is more affordable and easier to source, making it a practical choice for general industrial use.
- Inconel X-750, while more costly, justifies its price with superior performance in critical, high-temperature environments.
Key Differences at a Glance
Property | Inconel X-750 (UNS N07750) | Nickel Alloy 600 |
---|---|---|
Composition | Precipitation-hardened with aluminum and titanium | Solid-solution strengthened |
Tensile Strength | Higher (950–1350 MPa) | Moderate (550–690 MPa) |
Corrosion Resistance | Excellent, especially in nuclear applications | Versatile in chemical and marine environments |
High-Temperature Limit | Up to 980°C (1800°F) | Up to 1093°C (2000°F) |
Machinability | Difficult to machine | Easier to machine |
Weldability | Limited | Excellent |
Applications | Aerospace, nuclear, gas turbines | Chemical processing, heat exchangers |
Cost | Higher | Lower |