Perforated Casing Pipe for Oil & Gas and Water Wells
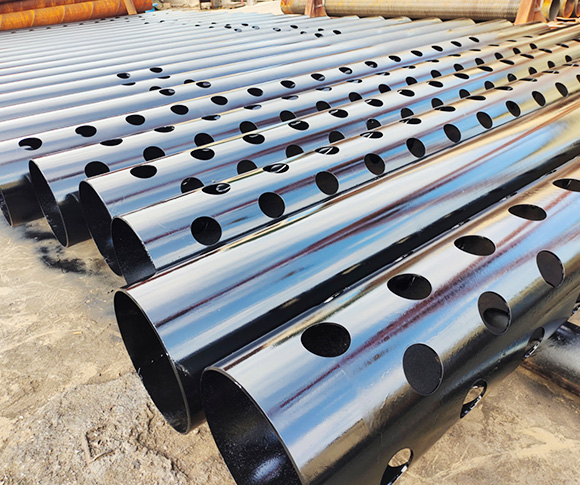
1. Introduction to Perforated Casing Pipes
Perforated casing pipes are designed to allow fluid flow into or out of the wellbore, specifically in oil & gas and water well applications. These pipes are typically made from steel, stainless steel, or carbon steel, and they are perforated with multiple holes or slots along their length. The perforations ensure that the casing can filter water or oil and allow for the safe passage of fluids while preventing unwanted particles from entering the well.
Applications of Perforated Casing Pipes
- Oil & Gas Wells: Used to allow oil or gas to flow into the well from the surrounding rock formations.
- Water Wells: Designed to allow groundwater to flow into the well without letting sediment or sand clog the wellbore.
2. Materials and Specifications
The choice of material for perforated casing pipes depends on the specific well conditions, such as temperature, pressure, and the chemical composition of the fluids involved. Common materials used include carbon steel, stainless steel, and alloy steel.
2.1. Materials for Perforated Casing Pipes
- Carbon Steel: Commonly used for standard applications due to its cost-effectiveness. It is typically used in freshwater wells and lower-temperature environments.
- Stainless Steel: Preferred for high-corrosion environments, such as seawater and oil production wells. Stainless steel alloys, such as 304 and 316, provide excellent resistance to rust and oxidation.
- Alloy Steel: Used for high-temperature and high-pressure applications, offering enhanced strength and resistance.
2.2. Common Specifications
Perforated casing pipes come in a variety of specifications, depending on the well requirements.
Specification | Description |
---|---|
Material | Carbon Steel, Stainless Steel (304/316), Alloy Steel |
Outside Diameter | 2 3/8” to 20” (60.3 mm to 508 mm) |
Wall Thickness | 0.188” to 0.500” (4.78 mm to 12.7 mm) |
Length | Customizable, typically 20 feet (6.1 meters) or longer |
Perforation Size | 1/8” to 1” (3.2 mm to 25.4 mm) depending on the sand/gravel size |
Perforation Type | Round, slotted, or triangular holes |
Grade | API 5CT, ASTM A53, ASTM A106, or custom grades for special applications |
2.3. Types of Perforation Patterns
- Round Perforations: Common for standard applications, used to allow efficient fluid flow.
- Slotted Perforations: Provides larger surface area and is commonly used in oil wells to increase permeability.
- Triangular or Other Shapes: Specially designed for specific applications, such as providing better resistance to clogging.
3. Perforated Casing Pipe Design and Features
The design of perforated casing pipes ensures that the perforations are strategically placed for optimal flow and structural integrity. Several factors influence the design, including:
3.1. Hole Size and Slot Width
- The hole size and slot width are designed based on the flow requirements and the type of fluid being extracted (e.g., oil, gas, or groundwater). Typically, the slot width is narrow enough to prevent the entry of unwanted sand and particles.
- Smaller slots are used for fine sands, while larger slots are used for coarser sands or gravel.
3.2. Perforation Spacing
- The perforations are spaced along the casing pipe to allow for optimal fluid flow while maintaining the integrity of the casing. The spacing will depend on the formation type, flow requirements, and material strength.
3.3. Pipe Strength and Pressure Rating
- The pipe strength must be sufficient to withstand external pressures, such as from the surrounding formation or the weight of the fluid inside the well. The pressure rating of the casing pipe ensures that the casing will hold up under high-pressure conditions, such as those encountered in deep oil and gas wells.
4. Mechanical Properties of Perforated Casing Pipes
The mechanical properties of perforated casing pipes are critical to ensuring their durability and ability to withstand environmental stressors such as high pressure, temperature, and corrosion. Some of the key mechanical properties include:
Property | Value |
---|---|
Tensile Strength | 50,000 to 80,000 psi (345 to 550 MPa) |
Yield Strength | 30,000 to 50,000 psi (207 to 345 MPa) |
Hardness | Rockwell B: 80-100 |
Elongation | 20-30% |
Impact Strength | 20-40 J (depending on material type) |
Corrosion Resistance | Excellent for stainless steel; good for carbon steel in freshwater environments |
5. Applications of Perforated Casing Pipes
Perforated casing pipes are used in a variety of applications in oil & gas and water wells:
5.1. Oil & Gas Wells
- Oil Production: Perforated casing pipes allow for the efficient flow of oil from the surrounding rock formations into the well. The perforations ensure that only the desired oil and gas are extracted, while preventing the influx of sand or debris.
- Gas Wells: In gas extraction, perforated casing pipes allow the flow of natural gas into the well from the surrounding geological formation.
5.2. Water Wells
- Water Extraction: In water wells, perforated casing pipes allow groundwater to flow into the well while preventing sand, silt, and other debris from entering the wellbore.
- Groundwater Monitoring: Perforated casing pipes are also used in environmental monitoring wells to allow for the collection of water samples without contamination from surrounding materials.
5.3. Geothermal Wells
- Geothermal Energy Production: In geothermal applications, perforated casing pipes allow for the efficient flow of heated groundwater or steam, which is used to generate power.
6. Benefits of Perforated Casing Pipes
- Increased Fluid Flow: The perforations allow for efficient fluid movement into the well, minimizing the need for additional equipment.
- Protection of Wellbore: Prevents the wellbore from collapsing by allowing fluid to flow freely without excessive pressure buildup.
- Customizable Design: Perforated casing pipes can be manufactured to meet specific size, perforation, and material requirements for a given well application.
- Durability: Corrosion-resistant materials like stainless steel ensure the longevity of the casing pipe, even in aggressive environments.
- Cost-Effective: Using perforated casing pipes helps prevent clogging and reduces the need for frequent maintenance or replacement.
7. Installation and Maintenance of Perforated Casing Pipes
7.1. Installation
- Site Preparation: Before installation, the well site must be properly prepared, with the casing pipe chosen based on the required diameter, strength, and perforation pattern.
- Casing Run: The perforated casing pipe is typically lowered into the well using specialized equipment, with proper alignment to ensure that the perforations are positioned to allow optimal fluid flow.
7.2. Maintenance
- Cleaning: Regular cleaning and maintenance of perforated casing pipes are essential, particularly in water wells, to prevent clogging from debris or mineral buildup.
- Inspection: Regular inspection ensures that the casing pipe is intact and the perforations are functioning as intended.
Conclusion
Perforated casing pipes are critical components for oil & gas and water well applications, enabling efficient fluid extraction while protecting the wellbore. The design and materials used in these pipes ensure they can withstand the pressures and environmental conditions within a well, whether it’s used for oil production, groundwater extraction, or geothermal energy generation. With customizable features and excellent mechanical properties, perforated casing pipes provide a reliable and cost-effective solution for well construction and maintenance.