Welding of INCONEL 625 nickel-based alloy steel
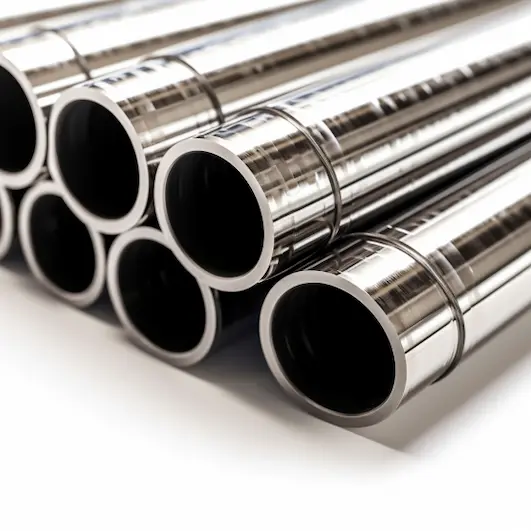
Welding of nickel-based alloy INCONEL 625
Introduction: In petrochemical construction projects, nickel-based alloys are often encountered, because this material has good properties of resistance to active gases, caustic media, and reducing acid media corrosion, and has high strength and good plasticity. , the characteristics of cold and cold deformation, processable molding and welding, are widely used in petrochemical industry. For example: In the gasification section of Liuguo Chemical Ammonia Synthesis Equipment in Tongling, Anhui, there is this material. Its specific name is INCONEL 625, which is used to transport oxygen media.
Keywords: Nickel-based alloy welding thermal cracks
1 The chemical composition and influence on welding properties of INCONEL 625, nickel-based alloy
To study the welding of INCONEL 625, it is necessary to understand the chemical composition of this material. The chemical composition of nickel-based alloy INCONEL 625 is shown in Table 1:
Table 1 Chemical composition of INCONEL 625 of nickel-based alloy (%)
alloying element
|
Ni |
C |
Mn |
Fe |
Cu |
P |
S |
Si |
Cr |
Al |
Ti |
Nb |
Mo |
content |
61.0 |
0.05 |
0.2 |
2.5 |
– |
0.015 |
0.008 |
0.2 |
21.5 |
0.2 |
0.2 |
3.6 |
9.0 |
Adding Al, Cr, Fe, Mo, and Ti to Ni can cause strong solid solution strengthening. Mo can improve the high temperature strength of nickel-based alloys, while Nb can stabilize the structure, refine the grains, and improve material performance. Cr in Ni The solid solution range in the range of about 35% to 40%, while the solid solution range in Ni is about 20%. The addition of alloy materials such as Cr and Mo not only increases their corrosion resistance, but also has no adverse impact on the welding performance of the material. Adding Ti, Mn, and Nb can improve the resistance of the material to thermal cracks and reduce pores. Si is a deoxidant and an antioxidant in steel. The C content is very small, because the presence of Ti and Nb generally does not cause intergranular corrosion.
The weldability of nickel-based alloys is more sensitive to S. S is insoluble in Ni and can form low-melting eutectics during welding solidification, which is prone to thermal cracks. P also increases crack sensitivity in nickel-based alloys.
2 Welding characteristics of nickel-based alloy INCONEL 625
2.1 Welding thermal crack nickel-based alloy INCONEL 625 has high thermal crack sensitivity during welding. Thermal cracks are divided into crystalline cracks, liquefied cracks and high-temperature deplastic cracks. Crystal cracks are most likely to occur in the weld bead arc pit, forming fire opening cracks. Crystallized cracks mostly crack longitudinally along the center line of the weld. Liquefied cracks are prone to appear in the heat-affected zone close to the fusion line, and some are also in the front welds of multi-layer welding. High temperature deplastic cracks may occur in both the heat-affected zone and in the weld. Various thermal cracks are sometimes macro cracks, or macro cracks are accompanied by micro cracks, and sometimes they are just micro cracks. Thermal cracks occur in high temperatures and no longer expand at room temperature.
2.2 The impact of pollutants on the surface of welded parts is a key to ensuring the welding quality of nickel-based alloy INCONEL 625. The contaminants on the surface of the weldment are mainly surface oxidation scale and elements that cause embrittlement. The melting point of the surface oxide scale of the nickel-based alloy INCONEL 625 is much higher than that of the base material, and it is often possible to form slag inclusions or fine discontinuous oxides. S, P, Pb, Sn, Zn, Bi, Sb and As can be used for the The elements that form low melting point eutectics are harmful elements. These harmful elements greatly increase the tendency of thermal cracks during welding of nickel-based alloys. These elements are often found in materials used in prefabrication, such as grease, paint, thermometers and markers, inks often contain these elements. Therefore, it must be completely removed before welding, including within 50mm outside the bevel.
The removal method depends on the type of contaminant. For oils and fats, steam degreasing or cleaning with acetone. For paint substances, they can be cleaned with chloromethane, alkaline liquid, and methanol, or they can be removed by polishing.
2.3 The influence of welding heat input The use of high heat input will cause the weld joint to anneale to a certain extent, and accompany the growth of grains, causing the tissue to undergo phase change and reduce the mechanical properties of the material. In addition, the input of high heat may cause excessive segregation of the crystal phase structure, precipitation and precipitation of carbides, thereby causing thermal cracks and reducing corrosion resistance.
This must be taken into account when choosing welding methods and welding processes. Therefore, it is more reasonable to use small current, narrow welding beads and multi-layer welding in actual operation.
It should be noted that some nickel-based alloys will have adverse effects on the weld structure near the heat-affected zone after welding. For example, after welding, Ni-Mo alloys need to be eliminated by annealing and restored their corrosion resistance. However, for the alloy INCONEL 625, it is a Ni-Cr-Mo alloy. Like austenitic stainless steel, the microstructure of the nickel-based alloy is also austenite, and there is no phase change in the solid state, and the base material and weld metal are The grains of the nickel-based alloy INCONEL 625 do not require heat treatment.
2.4 Welding process characteristics
(1) Liquid weld metal has poor fluidity. The weld metal of nickel-based alloy does not have good fluidity like carbon steel weld metal, but appears to be more “viscosity”. Even increasing the welding current cannot improve its fluidity, which is an inherent characteristic of nickel-based alloys. The welding current exceeds the recommended range not only overheats the molten pool and increases the sensitivity to thermal cracks, but also easily causes the deoxidant in the weld to evaporate and pores. During arc welding of welding rods, a large welding current will also heat the welding core of the welding rod, causing the powder to fall off, and lose protection.
Due to the poor fluidity of the weld metal, it is not suitable to flow to both sides of the weld to better fuse with the base material. Therefore, in order to obtain good weld forming, a swing process is required, but this swing should be a small swing and the swing range should be It is three times the diameter of the welding core or wire, and both sides of the weld should be better fused with the base material. Based on this consideration, this requires that the processing width of the bevel should be appropriate when making the bevel. During the swing of the welding rod, you should pay attention to the joint between the weld and the base material. This place is prone to undercuts, slag inclusions and unfusion. The solution is to run when the welding rod runs to the weld and the base material. The junction should be paused slightly and a short arc operation should be used.
(2) The depth of weld metal is also an inherent characteristic of nickel-based alloys, which requires the thickness of the blunt edge when making the bevel.
2.5 Selection of welding method
According to the welding method recommended by the Welding Society, the following welding methods can be used for materials such as INCONEL 625, SMAW (weld rod arc welding), GTAW (tungsten gas protective arc welding), GMAW (melting electrode gas protective arc welding), and PAW (plasma) Arc welding) and SAW (submerged arc welding), can be selected on site according to actual conditions.
2.6 Selection of welding materials
When using gas protective welding, a welding wire with model ERNiCrMo-3 should be selected, and its chemical compositions are shown in Table 2 respectively.
Table 2 Chemical composition of welding wire ERNiCrMo-3
alloying element |
Ni |
C |
Mn |
Fe |
S |
Si |
Cr |
Al |
Ti |
Nb |
Mo |
content% |
61.0 |
0.05 |
0.2 |
2.5 |
0.008 |
0.2 |
21.5 |
0.2 |
0.2 |
3.6 |
9.0 |
When using welding rod arc welding, welding rods with model ENiCrMo-3 should be selected, and their chemical compositions are shown in Table 3 respectively.
Table 3 Chemical composition of welding rod ENiCrMo-3
alloying element |
Ni |
Cr |
Fe |
Mo |
Mn |
Si |
Nb |
content% |
61.0 |
21.0 |
4.0 |
9.0 |
0.3 |
0.4 |
3.6 |
By comparing Tables 1, 2 and 3, it can be seen that the chemical composition of welding wire and welding rod is relatively close to the chemical composition of the base material, so it can be selected.
3 Welding process
At the construction site, the welding of nickel-based alloy materials is usually done by argon arc welding, welding rod arc welding filling and cover. The following describes its welding process:
3.1 Argon arc welding (tungsten gas protective arc welding)
3.1.1 It is recommended to use argon gas to help remove or reduce pores and protect the weld metal from oxidation.
3.1.2 When the welding specifications are certain, the shape of the electrode affects the melting depth and width of the weld. The pointed tungsten electrode can maintain the stability of the arc and sufficient melting depth. The usually used tungsten electrode cone angle is 30° to 60°, the tip is smoothed and the diameter is about 0.4mm.
3.1.3 Argon arc welding process The welding power supply adopts DC and the electrode is connected to the negative electrode. Welding machines are usually equipped with high-frequency current to ensure arcing and are equipped with current attenuation devices to gradually reduce the fire port size when arcing is closed.
In order to improve the crack resistance of weld metal and reduce pores, alloy elements such as Ti, Mn, Nb are usually added to the welding wire. Therefore, during welding, the weld metal should be ensured that at least 50% of the filler metal from the welding wire is derived. During welding, arcs should be avoided to stir the molten pool to keep the molten pool calm.
During welding, the wire heating end should always be in the protective gas to avoid oxidation of the wire and contamination of the weld metal. The welding wire should enter the molten pool at the front end of the molten pool to avoid contact with the tungsten pole.
The flow of the protective gas should be moderate, because too large gas flow may lead to rapid cooling of the weld metal. Therefore, the flow of the protective gas should be controlled at 4 to 8L/min.
When single-sided welding is formed on double-sided molding (for pipes with D≤600mm), protective gas needs to be input into the pipe.
3.2 Welding rod arc welding technology
The welding rods should be placed in a moisture-proof sealed container and stored in a dry environment. Before use, dry it according to the temperature and time specified in the manufacturing instructions.The welding wire should be placed in a wet-proof sealed container and stored in a dry environment. Before use, dry it according to the temperature and time specified in the manufacturing instructions.
The welding process of nickel-based alloy is similar to that of austenitic stainless steel. Due to the shallow melting depth of nickel-based alloy and the poor fluidity of liquid weld metal, the changes in welding parameters must be strictly controlled during the welding process. When welding nickel-based alloys, DC is generally used, and the welding rod is connected to the positive electrode. Each type and specification of welding rod has an optimal current range. Table 4 shows the welding current reference values for various specifications of nickel-based alloy welding rods:
Table 4 Reference value of nickel-based alloy welding current
|
Φ2.4 |
Φ3.2 |
Φ4.0 |
||||||
|
1.57 |
1.98 |
≥2.36 |
2.77 |
≥3.18 |
3.18 |
3.56 |
3.96 |
≥4.75 |
welding current (A) |
75 |
80 |
85 |
105 |
105 |
110 |
130 |
135 |
150 |
In actual operation, further adjustments should be made according to the thickness of the base material, welding position, joint form, etc. Whether the welding current is appropriate is crucial to ensuring the quality of the weld. If the current is too high, it will cause arc instability, overheating of the welding rod, causing the skin to fall off, and increase the tendency of thermal cracks.
When welding, the weld should be adjusted to a flat welding position as much as possible. The welding process should always maintain a short arc. When vertical welding or overhead welding position must be used, fine welding rods and small currents should be used to control the weld metal well.
The liquid nickel-based alloy has poor fluidity. In order to prevent defects such as unfusion and pores of the weld, the weld rod is required to swing during welding operations. The swing amplitude depends on the specific situation. Generally, the combination of the previous weld and the base material should be fully covered. The wire should not exceed 3 times the diameter of the weld core. Welds that are too wide will also cause poor fusion and uneven surface defects due to excessive heat dispersion. This requires the right width when making the bevel. The welding rod should pause slightly every time it swings to the edge to eliminate defects such as undercuts and slag inclusions and make the weld metal fully integrate with the base material.