2205 Duplex Steel Plate Welding Flange HG/T 20592 DN40 PN10 PLRF
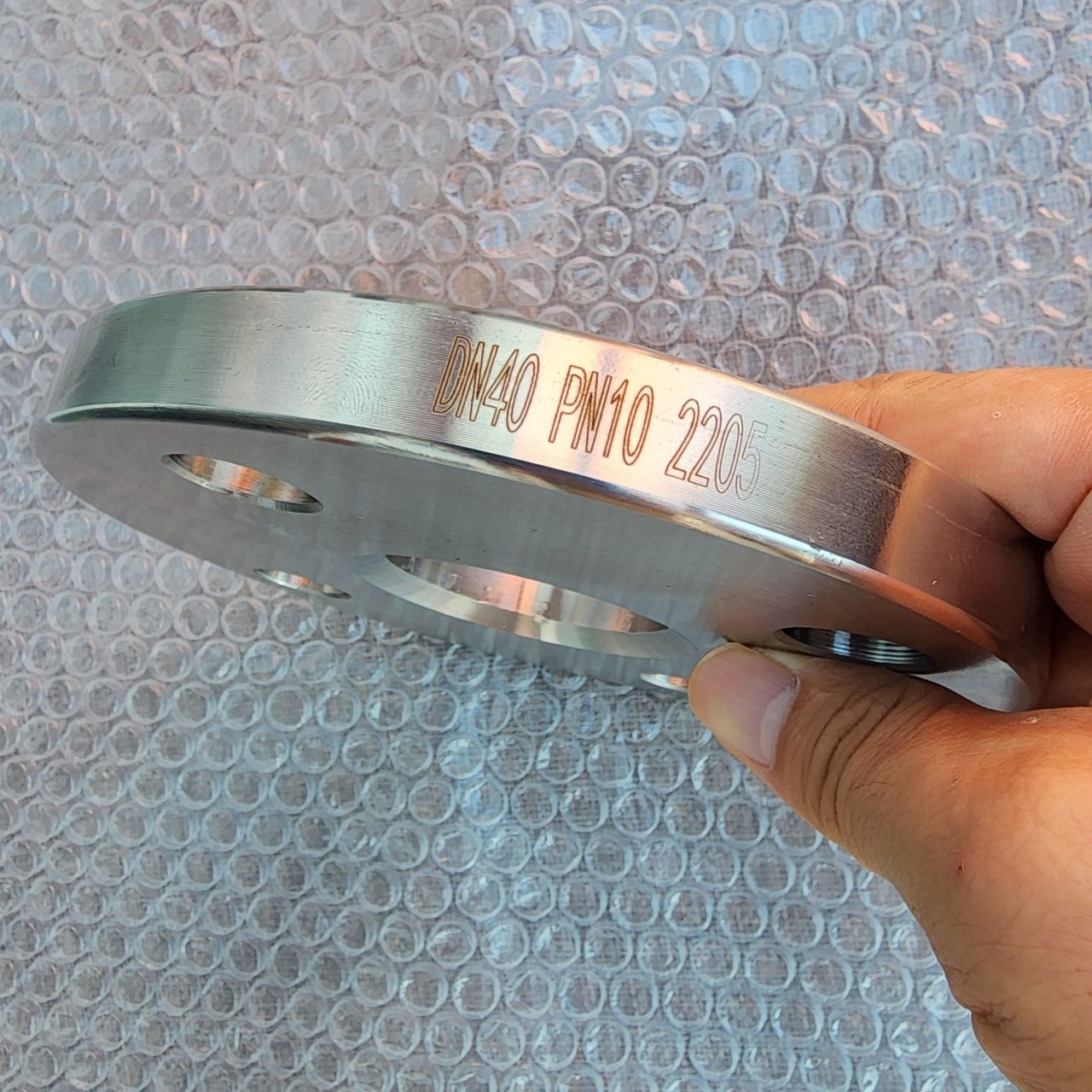
Material properties of 2205 duplex steel
2205 Duplex Steel is a high-strength, corrosion-resistant stainless steel material whose chemical composition mainly includes 22% chromium, 2.5% molybdenum and 4.5% nickel-nitrogen alloy. This material has the following main characteristics:
- High strength and high yield strength : The yield strength of 2205 duplex steel is twice that of ordinary austenitic stainless steel, usually between 450-600MPa, which makes it possible to reduce weight and save materials when designing products.
- Good corrosion resistance : 2205 duplex steel performs well in acidic and alkaline environments, with strong resistance to pitting and stress corrosion cracking. It is particularly effective in chloride-containing environments and can resist chloride ion stress corrosion cracking.
- Excellent impact toughness and welding performance : 2205 duplex steel has good impact toughness and welding performance, suitable for applications under high pressure and high load conditions. The heat input and interlayer temperature need to be strictly controlled during welding to avoid the precipitation of harmful intermetallic phases.
- Good resistance to stress corrosion : 2205 duplex steel has strong resistance to pitting and crevice corrosion in oxidizing and acidic solutions, and also exhibits excellent resistance to stress corrosion cracking under certain conditions.
- Physical properties : The density of 2205 duplex steel is 7.8g/cm³, the thermal conductivity is 19.0W/(m·K), and magnetism exists, but its magnetic properties can be changed by heat treatment.
- Application fields : 2205 duplex steel is widely used in marine engineering, petrochemical industry, natural gas pipelines, paper industry, food processing, pharmaceuticals and biotechnology. It is particularly suitable for pipelines in neutral chloride environments, oil refining industry, oil and gas industry and chemical industry.
- Processing characteristics : 2205 duplex steel has good processing performance, but cutting is more difficult than 316L. Heat input and interlayer temperature need to be strictly controlled during welding to avoid precipitation of harmful intermetallic phases. It is recommended to use ER2209 as weld filler metal and perform solution annealing to restore corrosion resistance.
In summary, 2205 duplex steel has been widely used in many industrial fields due to its high strength, excellent corrosion resistance and good processing performance.
Structural definition of plate type flat welding flange
Plate type flat welding flange is a common pipe connector, and its structure is defined as follows:
- Composition : Plate type flat welding flange is mainly composed of flange cover, flange ring and bolts. The flange cover is usually round with threaded holes on it, which is used to fix the flange cover and pipes or other connectors. The flange ring (also called sealing ring) is located between the two flange covers to seal and prevent medium leakage. Bolts are used to fix the two flange covers and flange ring together.
- Features :
- Simple structure : The design of the plate flat welding flange is relatively simple, consisting of a flange and a welding neck. It has no complex structural design and is easy to manufacture and install.
- Small size : Due to its simple structure, the plate type flat welding flange is relatively compact and suitable for occasions with limited space.
- Lower cost : Due to the relatively simple manufacturing process, the cost of plate flat welding flange is low.
- Sealing surface form : The sealing surface of the plate type flat welding flange can be a flat surface (FF) or a raised surface (RF), and the specific choice depends on the application requirements.
- Scope of application : Plate flat welding flanges are widely used in the connection of medium and low pressure containers and pipelines. They are suitable for industrial pipeline systems with low pressure, pressure fluctuations, vibrations and shocks.
- Material : Common materials include carbon steel, stainless steel, alloy steel and brass, etc. The specific selection is based on the working medium, environmental conditions and special needs.
- Manufacturing process : The manufacturing process of plate type flat welding flange includes material preparation, flange cover processing, flange ring making, surface treatment, assembly and welding.
In summary, plate flat welding flange is a kind of pipe connector with simple structure, low cost and wide application, which is suitable for various industrial fields.
Specific requirements for flanges in HG/T 20592 standard
According to HG/T 20592-2009 standard, the specific requirements for flanges are as follows:
- Nominal size and nominal pressure :
- The standard applies to steel pipe flanges and flange covers with nominal pressures of PN2.5 to PN160. The nominal pressure grades are expressed in PN, including nine grades: PN2.5, PN6, PN10, PN16, PN25, PN32, PN40, PN63, PN100, and PN160.
- Material :
- The flange material should comply with the requirements of Chapter 4 of the standard. Commonly used materials include Q235A, Q235B, 12CrMo, 2Cr13, 18Cr4NiMoV, 1Cr18Ni9Ti, etc.
- Flange type and sealing surface :
- Flange types include raised face, concave/convex face and grooved face. The sealing surface type shall comply with the provisions of Article 3.2.2 of the standard.
- The hardness of the sealing surface should be higher than the hardness of the matching metal ring gasket.
- Dimensional tolerance :
- When the nominal size of the flange is less than DN100, the dimensional tolerance is ±0.5mm; when the nominal size is greater than or equal to DN100, the dimensional tolerance is ±0.8mm.
- Appearance inspection :
- The flange surface should be smooth and free of defects, and sand and oxide scale should be removed. The machined surface should be free of burrs, scratches and other defects that affect strength and reliability.
- Marking method :
- The flange marking should include the standard number, flange type code, nominal size, applicable steel pipe outer diameter series, nominal pressure level, sealing surface type code, material brand, etc.
- Inspection and Acceptance :
- The flange welding joint and groove dimensions, testing, inspection, acceptance and other requirements shall be implemented in accordance with the provisions of Chapter 9 to Chapter 14 of the standard.
- Packaging and Shipping :
- Flanges should be packaged according to specifications and models, and accompanied by product quality certification documents. The outer cylindrical surface must be stamped with standard number, flange type code, nominal size, applicable steel pipe outer diameter series, nominal pressure level, sealing surface type code, material grade and wall thickness, etc.
- Other requirements :
- The maximum allowable working pressure of the flange shall comply with the requirements of Table 7.2 of the standard.
- Neck flanges should be made of forgings or castings, and should not be made of steel plates, welding or coiling.
The above content is a synthesis of multiple sources of evidence to ensure the accuracy and comprehensiveness of the information.
What is the meaning of DN40 in the nominal diameter of HG/T 20592 standard?
In the HG/T 20592 standard, the nominal diameter of DN40 refers to the standardized size of the pipe, which is usually used to indicate the inner diameter of the pipe or the size close to the inner diameter. According to the evidence, the nominal diameter of DN40 is 40 mm, but the actual inner diameter may vary slightly due to different wall thicknesses. For example, the outer diameter of a DN40 pipe with ordinary wall thickness is 47 mm and the inner diameter is 40 mm; the outer diameter of a DN40 pipe with thickened wall thickness is 48.5 mm and the inner diameter is about 40 mm.
The nominal diameter of DN40 is a standardized size in piping systems to ensure that fittings and pipes produced by different manufacturers can be interchanged and connected.
The meaning of PN10 pressure level in HG/T 20592 standard
According to HG/T 20592-2009 standard, PN10 indicates the pressure level with a nominal pressure of 1.0MPa. In this standard, PN10 is one of the nine pressure levels of steel pipe flanges (PN series), and is applicable to steel pipe flanges and flange covers with a nominal pressure range of PN2.5 to PN160.
What are the specific application scenarios of PN10 in the HG/T 20592 standard?
The specific application scenarios of PN10 in the HG/T 20592 standard mainly involve steel pipe flanges in the chemical industry. According to the HG/T 20592-2009 standard, PN10 is suitable for steel pipe flanges and flange covers with a nominal pressure of 10 bar, and is widely used in industries such as petrochemicals, water treatment, and food. These flanges are usually used to connect pipelines to ensure the normal flow and pressure control of fluids in the pipeline system.
Specifically, PN10 steel pipe flanges can be used in the following scenarios:
- Chemical equipment connection : such as pipeline connection of reactors, storage tanks, heat exchangers and other equipment.
- Water treatment system : such as the piping system of a water treatment plant, ensuring the stability and safety of water quality.
- Food industry : such as pipeline connections of food processing equipment to ensure hygiene and safety during food processing.
- Other industrial applications : such as pipeline systems in industries such as oil, gas, and electricity.
In addition, the specific specifications and dimensions of PN10 flanges are listed in detail in the standard, including nominal size, nominal pressure, material, sealing surface, tolerance, etc., which provides an important reference for selecting and installing suitable pipe flanges.
What is the temperature range corresponding to PN10?
The temperature range corresponding to PN10 varies in different application scenarios and materials. The following are some specific temperature ranges:
- Chengdu Kaiyuan Fluid Control Engineering Co., Ltd. ‘s flange straight-through valves have a pressure rating of PN10 and a temperature range of -10°C to 80°C.
- IBP Group ‘s valves have a nominal pressure of PN10 and a medium temperature range of 5°C to 95°C.
- Zhejiang Linuo Valve Co., Ltd. ‘s wafer-type ball valve has a pressure rating of PN10 and a temperature range of -29°C to 200°C (medium temperature) and 29°C to 425°C (high temperature).
- Suzhou Antway Industrial Valve Co., Ltd. ‘s metal hard seal ball valve has a pressure rating of PN10 and a temperature range of -196°C to 600°C.
- The national standard gate valves of Shanghai Hugong Valve Manufacturing Co., Ltd. have a pressure range of PN10 to 160MPa and an operating temperature range of -29°C to +600°C.
- The slow closing check valve from Fuller Valve & Fittings Co., Ltd. has a pressure rating of PN10 and a temperature range of -20°C to 80°C.
- Wuhan Boster Valve Group Co., Ltd. ‘s Z41W valve has a pressure range of PN10 to PN420 and an operating temperature range of -15°C to +120°C.
Based on the above information, the temperature range corresponding to PN10 is usually between -29°C and 80°C, but in specific application scenarios, it can reach a higher temperature range, such as -196°C to 600°C. The specific temperature range depends on the material, design and use environment of the valve.
PLRF flange type definition in HG/T 20592 standard
In the HG/T 20592 standard, PLRF represents the flange type with a raised face (RF) as the sealing surface of a flat welding flange (PL). Specifically:
- PL : Indicates that the flange type is Plated Lap Welding Flange, which is suitable for pipeline systems with welding connections.
- RF : Indicates that the sealing surface is a raised face. This sealing surface design helps to improve sealing performance.
Therefore, the definition of PLRF in HG/T 20592 standard is: a flat welding flange with a raised face sealing surface, suitable for pipeline connection scenarios requiring higher sealing performance.
Comprehensive analysis of “2205 duplex steel plate flat welding flange HG/T 20592 DN40 PN10 PLRF”
1. Material properties: 2205 duplex steel
2205 duplex steel (UNS S32205/S31803, 1.4462) is an austenitic-ferritic duplex stainless steel with both high strength and excellent corrosion resistance.
- Chemical composition
- Main components: Cr 21-24%, Ni 4.5-6.5%, Mo 2.5-3.5%, N 0.08-0.2%, carbon content ≤0.03%.
- Typical composition example: C 0.025%, Si 0.6%, Mn 1.5%, Cr 22.5%, Ni 5.8%, Mo 3.0%, N 0.16%.
- Mechanical properties
- Tensile strength ≥620 MPa, yield strength ≥450 MPa, elongation ≥25%, Brinell hardness ≤320.
- The yield strength is twice that of ordinary austenitic stainless steel (such as 316L), which can reduce material consumption and reduce costs.
- Corrosion resistance
- In corrosive environments such as chloride ions and seawater, its resistance to pitting corrosion, crevice corrosion and stress corrosion is better than that of 316L/317L and close to that of high-alloy austenitic stainless steel.
- Applicable temperature range: -50°C to +600°C (above 475°C, brittle phase precipitation must be avoided).
- Processing and welding
- Welding requires controlled heat input and cooling rate to maintain a ferrite-austenite phase balance (approximately 50:50).
- Cold forming requires greater external force and has a higher springback rate; tool life during machining may be reduced due to material hardness.
2. Flange structure: Plate type flat welding flange (PL)
Slip-on Plate Flange is a type of flange connected to the pipe through a fillet weld, with a simple structure and low cost.
- Structural features
- Composition: flange (with bolt holes) and welded neck, no complex structure.
- Applicable pressure level: low pressure (PN2.5-PN16), especially suitable for PN10 and below working conditions.
- Sealing face type: Raised face (RF) or flat face (FF). The “PLRF” in the user’s question indicates a raised face seal.
- Pros and Cons
- Advantages: small size, light weight, easy installation and strong economy.
- Limitations: Poor rigidity, not suitable for piping systems with high pressure, high temperature or severe vibration.
- Application
- Medium and low pressure containers, common industrial pipelines (such as water treatment, chemical low pressure pipelines).
- Prohibited scenarios: flammable and explosive media, high vacuum or high pressure (such as PN40 and above) environment.
3. Standard analysis: HG/T 20592
HG/T 20592-2009 is a Chinese chemical industry standard that specifies the technical requirements for PN series steel pipe flanges.
- Pressure level PN10
- PN10 corresponds to a nominal pressure of 1.0 MPa (10 bar), and the applicable temperature range depends on the temperature resistance of the material (2205 duplex steel up to 600°C).
- Nominal diameter DN40
- DN40 means the nominal diameter is 40 mm, and the outer diameter of the steel pipe is usually 47 mm (normal wall thickness) or 48.5 mm (thickened).
- The flange size must comply with the parameters such as the outer diameter (D) and bolt hole center distance (K) corresponding to DN40 in the standard (the specific values must be checked in the standard table).
- Flange marking rules
- Example marking: PLRF DN40-PN10 2205, where:
- PL: Plate type flat welding flange type code.
- RF: Raised face seal type.
- DN40: nominal diameter 40 mm.
- PN10: nominal pressure 1.0 MPa.
- 2205: The material is duplex steel S32205.
- Material requirements
- Flange materials must comply with the provisions of Chapter 4 of HG/T 20592, and 2205 duplex steel must provide material grade certification (such as S32205).
IV. Application suggestions and precautions
- Applicable scenarios
- Medium and low pressure pipeline connection for corrosive media (such as seawater, chlorine-containing solutions).
- Equipment that needs to reduce weight or cost (taking advantage of the high strength properties of 2205).
- Selection and installation
- Sealing gasket selection: It is recommended to use flexible graphite or PTFE gaskets to avoid chloride ion corrosion.
- Bolt tightening: Apply force evenly to avoid leakage of raised face seal due to uneven stress.
- Processing and maintenance
- When welding, special duplex steel welding materials (such as ER2209) must be used, and the interlayer temperature must be controlled to ≤150°C.
- During long-term use, the sealing surface needs to be checked regularly to prevent the precipitation of σ phase from affecting toughness.