Alloy 400 Nickel Tube • UNS N04400 • WNR 2.436
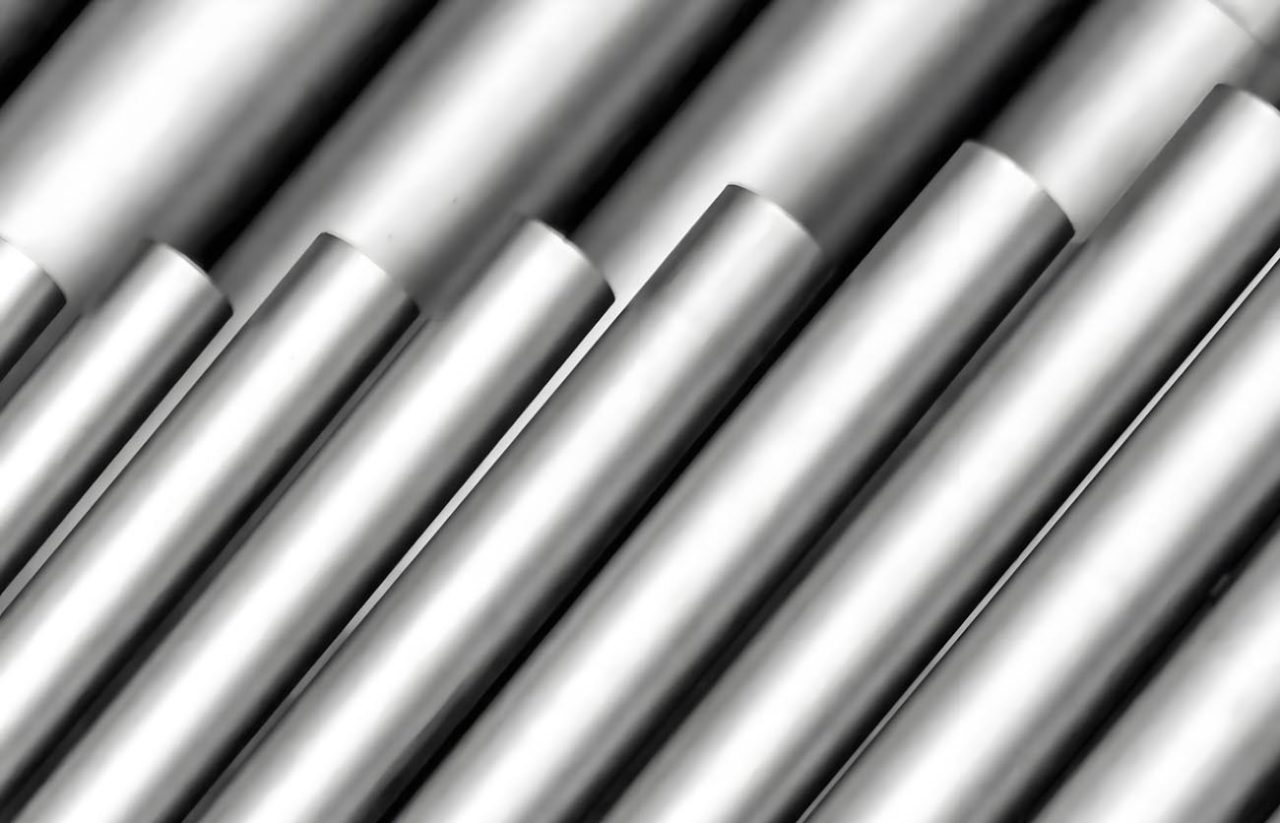
Alloy 400 Nickel Pipe and Tube • UNS N04400 • WNR 2.436
Alloy 400, also known as Monel 400, is a nickel-copper alloy renowned for its exceptional resistance to a wide range of corrosive environments, making it suitable for numerous applications.
This alloy consists of approximately 63% nickel and 28-34% copper, along with small amounts of other elements such as iron, manganese, and silicon. As one of the first nickel-copper alloys developed, Alloy 400 continues to be popular due to its unique combination of properties.
Alloy 400 is particularly known for its excellent resistance to seawater, various acids (including sulfuric and hydrochloric), alkaline solutions, and many other chemicals. These properties make it an ideal choice for applications in the marine, chemical processing, and oil and gas industries.
Specifications
- UNS Number: N04400
- Werkstoff Number (WNR): 2.4360
Chemical Composition
The typical chemical composition of Alloy 400 includes:
- Nickel (Ni): 63.0 min
- Copper (Cu): 28.0 – 34.0
- Iron (Fe): 2.5 max
- Manganese (Mn): 2.0 max
- Carbon (C): 0.3 max
- Silicon (Si): 0.5 max
- Sulfur (S): 0.024 max
Mechanical Properties
- Tensile Strength: 550 MPa (80 ksi) min
- Yield Strength (0.2% Offset): 240 MPa (35 ksi) min
- Elongation: 35% min
- Hardness: 70 HRB max
Physical Properties
- Density: 8.80 g/cm³
- Melting Point: 1350 – 1390 °C (2460 – 2530 °F)
- Specific Heat: 427 J/kg-°C (0.102 Btu/lb-°F)
- Thermal Conductivity: 21.8 W/m-°C (151 Btu-in/ft²-h-°F)
Applications
Alloy 400 is widely used in various industries due to its excellent performance in corrosive environments and its ability to maintain mechanical properties across a broad temperature range. Common applications include:
- Marine Engineering: Components exposed to seawater, such as valves, pumps, and propeller shafts.
- Chemical and Hydrocarbon Processing: Equipment such as heat exchangers, reactors, and distillation towers.
- Oil and Gas: Components for drilling and production, including pump shafts and other downhole equipment.
- Power Generation: Steam generators and other critical components.
- Aerospace: Structural components requiring high strength and corrosion resistance.
Corrosion Resistance
Alloy 400 is renowned for its excellent resistance to a variety of corrosive environments, including:
- Seawater and Brine: Outstanding resistance to seawater corrosion, both in flowing and stagnant conditions.
- Acids: Good resistance to sulfuric and hydrofluoric acids, especially in reducing conditions.
- Alkalies: Excellent performance in caustic alkalies.
- Chlorides: Resistant to stress-corrosion cracking in chlorinated environments.
Fabrication and Welding
Alloy 400 is easy to fabricate using standard techniques:
- Forming: Can be readily hot and cold formed.
- Machining: Machining should be performed at lower speeds with appropriate cutting fluids.
- Welding: Can be welded using conventional welding methods such as TIG, MIG, and resistance welding. Filler metals of matching composition are recommended.
Standards and Specifications
- ASTM: B163, B165 (tubes); B127 (plates, sheets, and strips); B164 (bars and rods)
- ASME: SB163, SB165 (tubes); SB127 (plates, sheets, and strips); SB164 (bars and rods)
- DIN: 17750 (tubes), 17751 (plates, sheets, and strips), 17752 (bars and rods)
- ISO: 6208
Summary
Alloy 400 is a versatile nickel-copper alloy that offers a combination of excellent corrosion resistance and high mechanical strength. Its ability to withstand harsh environments, including seawater, acids, and alkaline solutions, makes it a preferred choice for a wide range of applications in marine engineering, chemical processing, oil and gas, power generation, and aerospace industries.