API 5CT P110 Casing Tubing
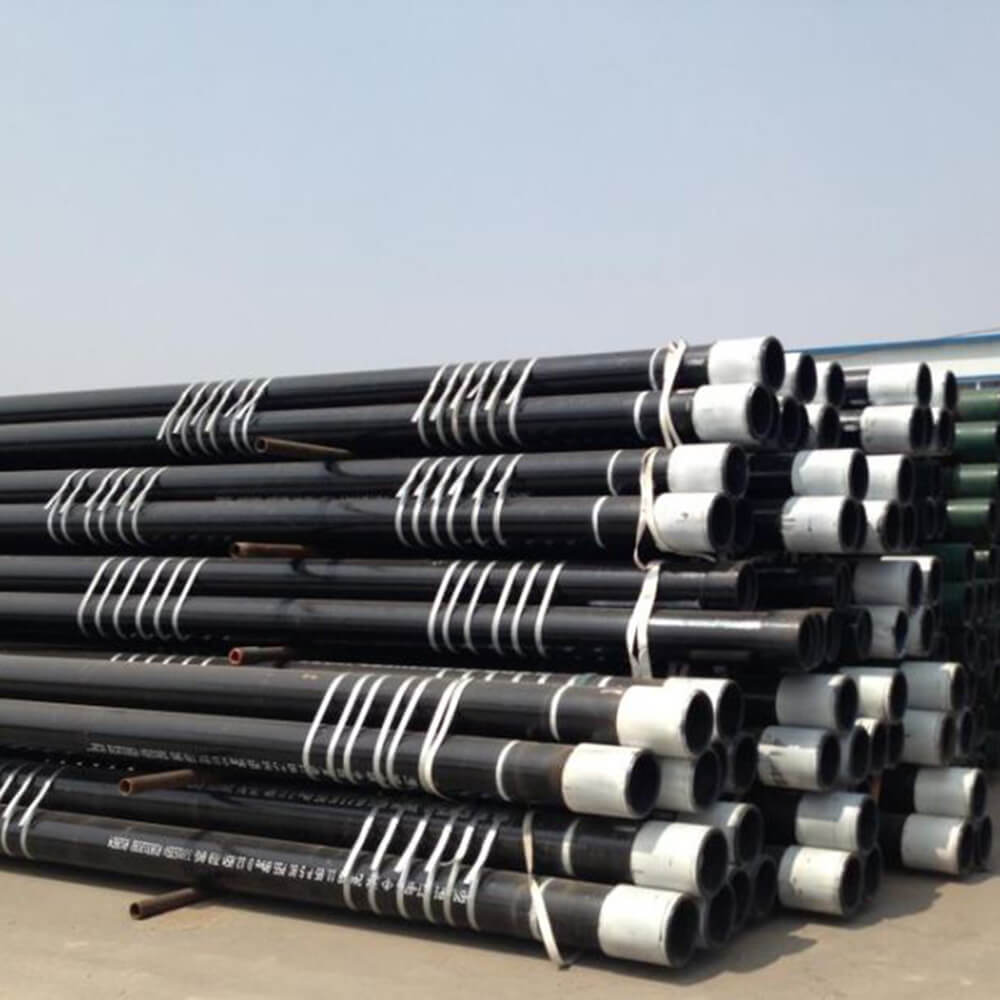
API 5CT P110 Casing Tubing
Introduction
API 5CT is a specification developed by the American Petroleum Institute (API) for casing and tubing materials used in the oil and gas industry. It includes various grades with different mechanical properties and chemical compositions. One of the high-strength grades specified under API 5CT is P110, which is commonly used in high-pressure and high-temperature environments.
Key Features and Grades
API 5CT P110 is designed for use in demanding environments where high strength and durability are crucial. P110 casing and tubing are typically used in deep well drilling operations due to their ability to withstand high pressures.
Chemical Composition
The chemical composition of API 5CT P110 is designed to provide excellent mechanical properties and toughness.
- Carbon (C): 0.22%
- Manganese (Mn): 1.40%
- Phosphorus (P): ≤ 0.025%
- Sulfur (S): ≤ 0.010%
- Silicon (Si): 0.20 – 0.45%
- Chromium (Cr): 0.30%
- Molybdenum (Mo): 0.25%
Mechanical Properties
API 5CT P110 casing and tubing offer high strength and toughness, making them suitable for challenging environments.
- Tensile Strength: 758 – 965 MPa (110,000 – 140,000 psi)
- Yield Strength: 758 MPa (110,000 psi) minimum
- Elongation: ≥ 15%
Manufacturing Process
Seamless and Welded Tubing
API 5CT P110 casing and tubing can be manufactured using either seamless or welded processes, each offering specific advantages depending on the application.
Seamless Process
- Billet Preparation: A solid steel billet is heated and pierced to create a hollow shell.
- Hot Rolling: The hollow shell is rolled to reduce its diameter and wall thickness.
- Cold Drawing (Optional): The tube is cold drawn to achieve precise dimensions and surface finish.
- Heat Treatment: The tube undergoes heat treatment to achieve the required mechanical properties.
- Straightening and Cutting: The tube is straightened and cut to the desired length.
Welded Process
- Strip Preparation: Steel strips are slit to the required width.
- Forming: The strips are formed into a cylindrical shape.
- Welding: The edges of the formed strip are welded together.
- Heat Treatment: The welded tube undergoes heat treatment to achieve the required mechanical properties.
- Sizing and Cutting: The tube is sized and cut to the required length.
Heat Treatment
Heat treatment is crucial to achieve the desired mechanical properties. For P110 grade, the typical heat treatments include:
- Quenching and Tempering: Heating the tube to a high temperature, then rapidly cooling (quenching) and reheating to a lower temperature (tempering) to achieve the desired strength and toughness.
Testing Requirements
API 5CT specifies rigorous testing requirements to ensure the quality and performance of P110 casing and tubing:
- Tensile Test: Measures tensile strength, yield strength, and elongation.
- Hardness Test: Ensures the material meets specified hardness levels.
- Impact Test: Assesses the material’s toughness at various temperatures.
- Hydrostatic Test: Ensures the tube can withstand internal pressure without leaking.
- Non-Destructive Testing: Includes ultrasonic, magnetic particle, and radiographic testing to detect any defects.
- Sour Service Testing: Ensures resistance to sulfide stress cracking (SSC) for use in sour environments.
API 5CT P110 Casing Tubing Type of Casing:
- short round thread casing(SC)
- long round thread casing(LC)
- buttress thread casing(BC)
API 5CT P110 Casing Tubing Chemical Composition:
Chemical Composition, Mass Fraction (%) | ||||||||||||||
Grade | C | Mn | Mo | Cr | Ni | Cu | P | S | Si | |||||
Type | min | max | min | max | min | max | min | max | max | max | max | max | max | |
1 | 2 | 3 | 4 | 5 | 6 | 7 | 8 | 9 | 10 | 11 | 12 | 13 | 14 | 15 |
H40 | — | — | — | — | — | — | — | — | — | — | — | — | 0.03 | — |
J55 | — | — | — | — | — | — | — | — | — | — | — | — | 0.03 | — |
K55 | — | — | — | — | — | — | — | — | — | — | — | — | 0.03 | — |
N80 | 1 | — | — | — | — | — | — | — | — | — | — | 0.03 | 0.03 | — |
N80 | Q | — | — | — | — | — | — | — | — | — | — | 0.03 | 0.03 | — |
R95 | — | — | 0.45 c | — | 1.9 | — | — | — | — | — | — | 0.03 | 0.03 | 0.45 |
L80 | 1 | — | 0.43 a | — | 1.9 | — | — | — | — | 0.25 | 0.35 | 0.03 | 0.03 | 0.45 |
L80 | 9Cr | — | 0.15 | 0.3 | 0.6 | 0.9 | 1.1 | 8 | 10 | 0.5 | 0.25 | 0.02 | 0.03 | 1 |
L80 | 13Cr | 0.15 | 0.22 | 0.25 | 1 | — | — | 12 | 14 | 0.5 | 0.25 | 0.02 | 0.03 | 1 |
C90 | 1 | — | 0.35 | — | 1.2 | 0.25 b | 0.85 | — | 1.5 | 0.99 | — | 0.02 | 0.03 | — |
T95 | 1 | — | 0.35 | — | 1.2 | 0.25 b | 0.85 | 0.4 | 1.5 | 0.99 | — | 0.02 | 0.03 | — |
C110 | — | — | 0.35 | — | 1.2 | 0.25 | 1 | 0.4 | 1.5 | 0.99 | — | 0.02 | 0.03 | — |
P110 | e | — | — | — | — | — | — | — | — | — | — | 0.030 e | 0.030 e | — |
Q125 | 1 | — | 0.35 | 1.35 | — | 0.85 | — | 1.5 | 0.99 | — | 0.02 | 0.01 | — | |
NOTE Elements shown shall be reported in product analysis. | ||||||||||||||
a The carbon content for L80 may be increased up to 0.50 % maximum if the product is oil-quenched or polymer-quenched. | ||||||||||||||
b The molybdenum content for Grade C90 Type 1 has no minimum tolerance if the wall thickness is less than 17.78 mm. | ||||||||||||||
c The carbon content for R95 may be increased up to 0.55 % maximum if the product is oil-quenched. | ||||||||||||||
d The molybdenum content for T95 Type 1 may be decreased to 0.15 % minimum if the wall thickness is less than 17.78 mm. | ||||||||||||||
e For EW Grade P110, the phosphorus content shall be 0.020 % maximum and the sulfur content 0.010 % maximum. |
API 5CT P110 Casing Tubing Mechanical Properties:
Tensile and Hardness Requirements | |||||||||
Grade | Yield Strength MPa | Tensile Strength | Hardness a,c | Specified Wall Thickness | Allowable Hardness Variation b | ||||
Type | Total Elongation Under Load | min MPa | max | ||||||
min | max | HRC | HBW | mm | HRC | ||||
1 | 2 | 3 | 4 | 5 | 6 | 7 | 8 | 9 | 10 |
H40 | — | 0.5 | 276 | 552 | 414 | — | — | — | — |
J55 | — | 0.5 | 379 | 552 | 517 | — | — | — | — |
K55 | — | 0.5 | 379 | 552 | 655 | — | — | — | — |
N80 | 1 | 0.5 | 552 | 758 | 689 | — | — | — | — |
N80 | Q | 0.5 | 552 | 758 | 689 | — | — | — | — |
R95 | — | 0.5 | 655 | 758 | 724 | — | — | — | — |
L80 L80 | 1 | 0.5 | 552 | 655 | 655 | 23 | 241 | — | — |
L80 | 9Cr 13Cr | 0.5 | 552 | 655 | 655 | 23 | 241 | — | — |
0.5 | 552 | 655 | 655 | 23 | 241 | — | — | ||
C90 | 1 | 0.5 | 621 | 724 | 689 | 25.4 | 255 | £12.70 | 3 |
12.71 to 19.04 | 4 | ||||||||
19.05 to 25.39 | 5 | ||||||||
³ 25.40 | 6 | ||||||||
T95 | 1 | 0.5 | 655 | 758 | 724 | 25.4 | 255 | £12.70 | 3 |
12.71 to 19.04 | 4 | ||||||||
19.05 to 25.39 | 5 | ||||||||
³ 25.40 | 6 | ||||||||
C110 | — | 0.7 | 758 | 828 | 793 | 30 | 286 | £12.70 | 3 |
12.71 to 19.04 | 4 | ||||||||
19.05 to 25.39 | 5 | ||||||||
³ 25.40 | 6 | ||||||||
P110 | — | 0.6 | 758 | 965 | 862 | — | — | — | — |
Q125 | 1 | 0.65 | 862 | 1034 | 931 | b | — | £12.70 | 3 |
12.71 to 19.04 19.05 | 4 | ||||||||
5 | |||||||||
a In case of dispute, laboratory Rockwell C hardness testing shall be used as the referee method. | |||||||||
b No hardness limits are specified, but the maximum variation is restricted as a manufacturing control in accordance with 7.8 and 7.9. | |||||||||
c For through-wall hardness tests of Grades L80 (all types), C90, T95 and C110, the requirements stated in HRC scale are for maximum mean hardness number. |
API 5CT P110 Casing Tubing Range Lengths | |||
Range 1 | Range 2 | Range 3 | |
CASING (PE/T and C/SF) | |||
Total range length, inclusive Permissible variation, max a | 4.88 to 7.62 1.83 | 7.62 to 10.36 | 10.36 to 14.63 1.83 |
1.52 | |||
TUBING AND CASING USED AS TUBING | |||
(PE/T and C/SF) | |||
Total range length, inclusive Permissible variation, max a | 6.10 to 7.32 b | 8.53 to 9.75 c | 11.58 to 12.80 d |
0.61 | 0.61 | 0.61 | |
INTEGRAL TUBING CONNECTIONS (including IJ/PE | |||
and IJ/SF) | |||
Total range length, inclusive Permissible variation, max a | 6.10 to 7.92 e | 8.53 to 10.36 | 11.58 to 13.72 0.61 |
0.61 | 0.61 | ||
PUP JOINTS | Lengths: 0.61; 0.91; 1.22; 1.83; 2.44; 3.05 and 3.66 e | ||
Tolerance: ±0.076 | |||
a Length variation applies to rail car shipment to the point of use and does not apply to order items of less than 18,144 kg of Pipe. | |||
b By agreement between purchaser and manufacturer, the maximum length may be increased to 8.57 m. | |||
c By agreement between purchaser and manufacturer, the maximum length may be increased to 10.76 m. | |||
d By agreement between purchaser and manufacturer, the maximum length may be increased to 17.72 m.0.61 m pup joints may be furnished up to 0.91 m long by agreement between purchaser and manufacturer, and lengths other than those listed may be furnished by agreement between purchaser and manufacturer. |
Applications
API 5CT P110 casing and tubing are used in various high-pressure and high-temperature environments, including:
- Oil and Gas Wells: Casing to protect the wellbore and tubing to transport hydrocarbons.
- Deep Well Drilling: High-strength casing and tubing for deep drilling operations.
- Geothermal Wells: Tubing for high-temperature and high-pressure geothermal applications.
- Offshore Drilling: High-strength casing and tubing for deep-water drilling operations.
Advantages and Limitations
Advantages
- High Strength: Suitable for high-pressure and high-temperature environments.
- Durability: High toughness ensures durability in challenging conditions.
- Versatility: Available in both seamless and welded forms.
- Reliability: High mechanical properties ensure reliability in demanding applications.
Limitations
- Cost: Higher cost compared to lower-grade materials due to alloying elements and heat treatment processes.
- Manufacturing Complexity: Requires precise control over chemical composition and heat treatment.
- Availability: Specific grades and sizes may have longer lead times.
Conclusion
API 5CT P110 casing and tubing are essential for high-pressure and high-temperature applications in the oil and gas industry. Their superior mechanical properties, combined with rigorous manufacturing and testing processes, ensure they meet the demanding requirements of various environments. Understanding the detailed specifications, grades, and applications of API 5CT P110 helps engineers and designers select the right materials for their projects, ensuring safety and efficiency in challenging drilling and production operations.
By examining the chemical composition, mechanical properties, manufacturing processes, and applications, this analysis provides a comprehensive overview of API 5CT P110 casing and tubing, highlighting their significance in high-performance industrial applications.