ASTM A335 P5 Alloy Steel Pipe Welded Joints Investigations on Corrosion Behaviour
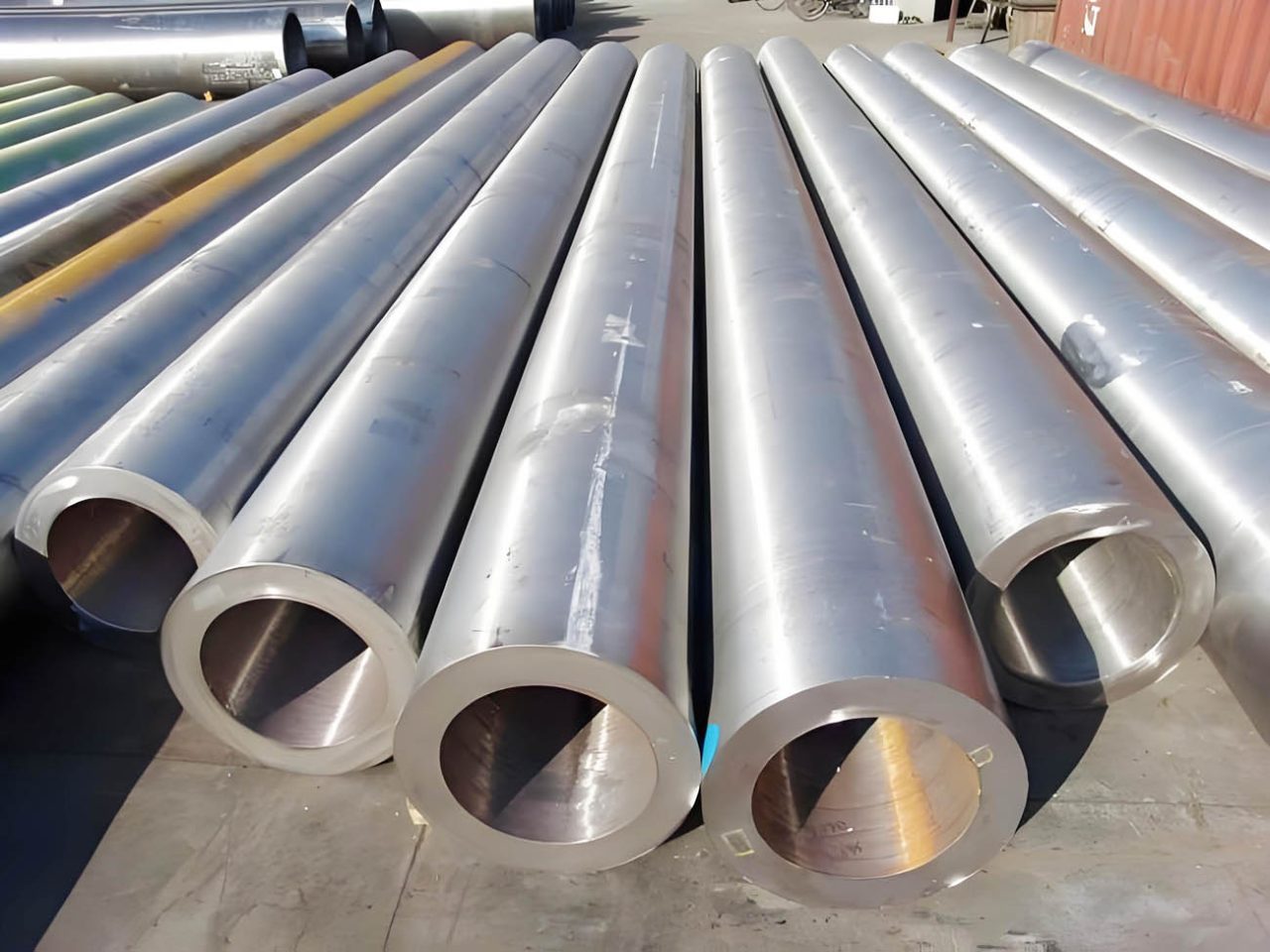
Investigations on Corrosion Behaviour of Welded Joints in ASTM A335 P5 Alloy Steel Pipe
Introduction
Corrosion is one of the most critical challenges in the performance and longevity of welded joints, especially in high-temperature and high-pressure applications such as those involving alloy steel pipes. ASTM A335 P5 alloy steel, known for its excellent high-temperature strength and resistance to oxidation, is widely used in industries like power generation, petrochemical, and oil & gas. However, the welding process can introduce vulnerabilities that affect the corrosion resistance of the material. This article delves into the corrosion behavior of welded joints in ASTM A335 P5 alloy steel pipes, exploring the factors that influence corrosion, the types of corrosion observed, and methods to mitigate these effects.
Overview of ASTM A335 P5 Alloy Steel
Composition and Properties
ASTM A335 P5 is a chromium-molybdenum alloy steel designed for high-temperature service. Its chemical composition typically includes:
- Chromium (Cr): 4.0-6.0%
- Molybdenum (Mo): 0.45-0.65%
- Carbon (C): 0.15% max
- Silicon (Si): 0.50% max
- Manganese (Mn): 0.30-0.60%
The addition of chromium provides resistance to oxidation and corrosion, while molybdenum enhances the material’s strength and resistance to high-temperature creep. These properties make ASTM A335 P5 ideal for use in environments where both mechanical strength and corrosion resistance are required.
Applications
Common applications of ASTM A335 P5 alloy steel pipes include:
- Steam pipelines in power plants
- Petrochemical refineries
- Heat exchangers
- High-pressure boilers
Welding of ASTM A335 P5 Alloy Steel
Welding Techniques
Welding ASTM A335 P5 alloy steel requires careful consideration of the welding technique and post-weld heat treatment (PWHT) to preserve the material’s mechanical properties and corrosion resistance. Common welding techniques include:
- Gas Tungsten Arc Welding (GTAW): Also known as TIG welding, this method is often used for precision welding of alloy steels.
- Shielded Metal Arc Welding (SMAW): This method is commonly used for field welding and repair work.
- Submerged Arc Welding (SAW): Used for large-diameter pipes, SAW provides deep penetration and high deposition rates.
Post-Weld Heat Treatment (PWHT)
PWHT is crucial for welded joints in ASTM A335 P5 alloy steel. It helps relieve residual stresses induced by welding and restores the material’s mechanical properties. PWHT also plays a vital role in mitigating the risk of stress corrosion cracking (SCC) and other forms of corrosion.
Corrosion Behavior of Welded Joints
Types of Corrosion
Welded joints in ASTM A335 P5 alloy steel pipes are susceptible to various types of corrosion, depending on the service environment and the quality of the weld. The most common forms of corrosion include:
- Pitting Corrosion: Localized corrosion that results in small pits or holes in the material. This is often caused by the breakdown of the protective oxide layer on the surface of the steel.
- Intergranular Corrosion: Occurs along the grain boundaries of the material, particularly in areas affected by welding. This type of corrosion is often associated with improper heat treatment or sensitization.
- Stress Corrosion Cracking (SCC): A combination of tensile stress and a corrosive environment can lead to SCC, which is particularly dangerous as it can cause sudden failure of the material.
- Crevice Corrosion: Occurs in areas where there is a gap or crevice, such as between the weld and the base metal. This type of corrosion is often exacerbated by stagnant conditions and the presence of chlorides.
Factors Influencing Corrosion
Several factors influence the corrosion behavior of welded joints in ASTM A335 P5 alloy steel pipes:
- Weld Quality: Defects such as porosity, incomplete fusion, and slag inclusions can act as initiation sites for corrosion.
- Heat-Affected Zone (HAZ): The HAZ is the area of the base metal that is thermally affected by the welding process. Changes in microstructure in the HAZ can make it more susceptible to corrosion.
- Post-Weld Heat Treatment (PWHT): Inadequate or improper PWHT can lead to residual stresses and microstructural changes that increase the risk of corrosion.
- Service Environment: The presence of corrosive agents such as chlorides, sulfur compounds, and moisture can accelerate the corrosion of welded joints.
Investigative Methods for Corrosion Behavior
Electrochemical Testing
Electrochemical testing methods, such as potentiodynamic polarization and electrochemical impedance spectroscopy (EIS), are used to evaluate the corrosion resistance of welded joints. These tests provide insights into the corrosion potential, corrosion rate, and passivation behavior of the material.
Metallographic Analysis
Metallographic analysis involves examining the microstructure of the welded joint, particularly the heat-affected zone (HAZ) and the weld metal. This analysis helps identify microstructural changes that may contribute to corrosion, such as grain boundary sensitization or carbide precipitation.
Salt Spray Testing
Salt spray testing is a common method for evaluating the resistance of welded joints to pitting and crevice corrosion. The welded samples are exposed to a saline mist for a specified period, and the extent of corrosion is assessed.
Stress Corrosion Cracking (SCC) Testing
SCC testing involves subjecting welded joints to a combination of tensile stress and a corrosive environment to evaluate their susceptibility to stress corrosion cracking. This test is particularly important for applications involving high-pressure steam or corrosive chemicals.
Mitigation Strategies for Corrosion
Proper Welding Techniques
Using appropriate welding techniques and ensuring the quality of the weld are critical to preventing corrosion. This includes selecting the right filler material, maintaining proper heat input, and avoiding welding defects.
Post-Weld Heat Treatment (PWHT)
Conducting proper PWHT is essential for reducing residual stresses and restoring the material’s corrosion resistance. The PWHT process should be carefully controlled to ensure that the material’s microstructure is optimized for corrosion resistance.
Corrosion-Resistant Coatings
Applying corrosion-resistant coatings, such as epoxy coatings or metallic coatings, can provide an additional layer of protection for welded joints. These coatings help prevent the exposure of the base metal to corrosive agents.
Cathodic Protection
Cathodic protection is a technique used to prevent corrosion by making the welded joint the cathode of an electrochemical cell. This method is commonly used in pipelines and other buried or submerged structures.
Conclusion
Welded joints in ASTM A335 P5 alloy steel pipes are susceptible to various forms of corrosion, particularly in harsh environments. The welding process, heat-affected zone, and post-weld heat treatment all play critical roles in determining the corrosion behavior of the material. By employing proper welding techniques, conducting adequate PWHT, and using corrosion-resistant coatings, the risk of corrosion can be significantly mitigated. Understanding the factors that influence corrosion and implementing appropriate mitigation strategies are essential for ensuring the long-term performance and reliability of welded joints in ASTM A335 P5 alloy steel pipes.
FAQ
What is ASTM A335 P5 alloy steel used for?
ASTM A335 P5 alloy steel is commonly used in high-temperature and high-pressure applications, such as steam pipelines, petrochemical refineries, and power plants.
Why is post-weld heat treatment (PWHT) important for ASTM A335 P5?
PWHT is essential for relieving residual stresses and restoring the material’s mechanical properties and corrosion resistance after welding.
What types of corrosion can affect welded joints in ASTM A335 P5?
Welded joints in ASTM A335 P5 can be affected by pitting corrosion, intergranular corrosion, stress corrosion cracking (SCC), and crevice corrosion.
How can the corrosion of welded joints be mitigated?
Corrosion can be mitigated by using proper welding techniques, conducting adequate PWHT, applying corrosion-resistant coatings, and using cathodic protection.
What testing methods are used to investigate the corrosion behavior of welded joints?
Common testing methods include electrochemical testing, metallographic analysis, salt spray testing, and stress corrosion cracking (SCC) testing.