Drill Collar | Slick & Spiral Type , Non-magnetic Drill Collar
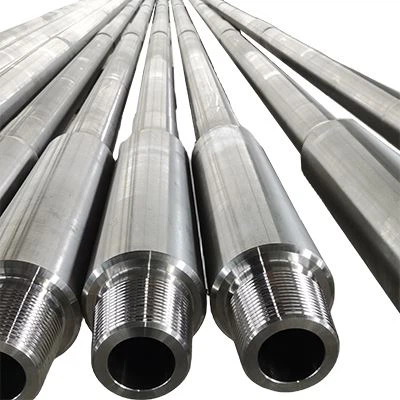
Drill Collar: An Essential Component in Drilling Operations
Introduction
A drill collar is a thick-walled tubular piece of drilling equipment used in the bottom hole assembly (BHA) of a drill string. It is critical for providing weight on the bit (WOB) and ensuring the stability and direction of the drilling process. This article explores the characteristics, types, applications, and benefits of drill collars in drilling operations.
Characteristics of Drill Collars
Material
Drill collars are typically made from high-strength alloy steel or non-magnetic materials. The steel used is often AISI 4145H-modified, which offers excellent mechanical properties and resistance to fatigue and wear.
Product Names
- Drill Collars
- Spiral Drill Collar
- Non-magnetic Drill Collar
- Drill Collar and Drill Stem Accessories
Sizes
- Outer Diameter: 3 1/8″ – 11″
Lengths
- Standard Lengths: 30 ft, 31 ft, 43 ft
- Range: R1 to R3
Connection Types
- NC (Numbered Connections)
- REG (Regular)
- FH (Full Hole)
- IF (Internal Flush)
Thread Types
- NC26
- NC31
- NC38
- NC40
- NC46
- NC50
- 5 1/2 FH
Materials
- Stainless Steel
- Alloy Steel (including AISI 4145H)
- Carbon Steel
Standards
- API 5DP
- API Spec 7-1
Applications
- Oil and Gas Well Drilling
- Oilfield Drilling
Dimensions
- Length: Standard lengths are usually 30 feet, but they can vary depending on the specific requirements of the drilling operation.
- Outer Diameter (OD): Common OD sizes range from 3.5 inches to 11 inches.
- Inner Diameter (ID): The ID is designed to accommodate the passage of drilling fluids and varies based on the OD and wall thickness.
Product Type
1. Drill Collars
Drill collars are essential components in drilling operations, used primarily to provide weight on the bit for effective drilling through rock formations. They are solid bars made from either plain carbon steel or non-magnetic steel alloys, with a central bore to allow the passage of drilling fluids. Typically, drill collars are 31 feet (9.45 meters) long and feature threaded ends to enable connection with other drill collars.
2. Slick Drill Collar
- Material: Modified alloy steel, quenched and tempered for required mechanical properties.
- Surface Finish: As-rolled or spiraled.
- Function: Provides the necessary weight on the bit and stabilizes the drilling assembly.
- Features: Slick drill collars have a smooth outer surface, while spiral drill collars have grooves to facilitate fluid flow and reduce differential sticking.
3. Spiral Drill Collar
- Material: AISI 4145H alloy steel, non-magnetic steel.
- Shape: Features three dextrogyrate spiral grooves to reduce contact friction with the well wall.
- Usage: Positioned between the drill head and drill pipe to ensure smooth operation and maintain drilling trajectory.
- Standards: Manufactured according to API Spec 7-1 or SY/T5144.
- Inspection & Tests: Comprehensive traceability and serial numbers stamped on each piece. Inspections and tests are conducted throughout the manufacturing process.
4. Non-magnetic Drill Collar
- Material: Chrome manganese low carbon austenitic alloy.
- Characteristics:
- Magnetic Permeability: Low, ensuring minimal interference with electronic instruments.
- Mechanical Properties: High strength and excellent resistance to stress corrosion cracking.
- Surface: Non-galling, preventing surface damage during operations.
- Usage: Ideal for directional drilling and environments where magnetic interference must be minimized.
Weight
Drill collars are significantly heavier than other components of the drill string, with weights ranging from a few hundred to several thousand pounds, depending on their size and material.
Applications of Drill Collars
Weight on Bit (WOB)
Drill collars provide the necessary weight to the drill bit, allowing it to penetrate the rock formations effectively. This weight helps in achieving the desired rate of penetration (ROP).|
Stability and Directional Control
By adding mass to the bottom hole assembly, drill collars help stabilize the drill string and maintain the desired direction of the wellbore. This is particularly important in directional and horizontal drilling operations.
Vibration Dampening
The heavy mass of drill collars helps dampen vibrations and reduces the risk of drill string failure due to fatigue. This contributes to smoother drilling operations and prolongs the life of the drill string components.
Differential Sticking Prevention
Spiral drill collars, with their grooved design, help prevent differential sticking by improving the circulation of drilling fluids and cuttings removal. This reduces the risk of the drill string getting stuck in the wellbore.
Drill Collar Material and Technical Specifications
Drill collars are critical components of the drill string, providing the necessary weight, stability, and strength for effective drilling operations. The material and technical specifications of drill collars are essential for their performance and reliability. This article outlines the common materials used, along with detailed technical specifications.
Technical Specifications
-
Chemical composition
Drill Collor Number*Outside Diameter,
in.Inside Diameter,
in.Length,
ftApproximate Weight,
lb/ftTypical Bending
Strength RatioNC 23-313-1/81-1/430222.57:1NC 26-35 (2-3/8 IF)3-1/21-1/230272.42:1NC 31-41 (2-7/8 IF)4-1/8230 or 31342.43:1NC 35-474-3 /4230 or 31472.58:1NC 38-50 (3-1/2 IF)52-1/430 or 31542.38:1NC 44-6062-1/430 or 31832.49:1NC 44-6062-13 /1630 or 31762.84:1NC 44-626-1/42-1/430 or 31912.91:1NC 46-62 (4 IF)6-1/42-13 /1630 or 31842.63:1NC 46-65 (4 IF)6-1/22-1/430 or 311002.76:1NC 46-65 (4 IF)6-1/22-13 /1630 or 31933.05:1NC 46-67 (4 IF)6-3 /42-1/430 or 311093.18:1NC 50-70 (4-1/2 IF)72-1/430 or 311182.54:1NC 50-70 (4-1/2 IF)72-13 /1630 or 311112.73:1NC 50-72 (4-1/2 IF)7-1/42-13 /1630 or 311203.12:1NC 56-777-3 /42-13 /1630 or 311402.70:1NC 56-8082-13 /1630 or 311513.02:16-5/8 API Reg8-1/42-13 /1630 or 311622.93:1NC 61-9092-13 /1630 or 311963.17:17-5/8 API Reg9-1/2330 or 312172.81:1NC 70-979-3 /4330 or 312302.57:1NC 70-10010330 or 312432.81:18-5/8 API Reg11330 or 313002.84:1O.D. cutting depth Lead ±25.4 mm in A(mm) B(mm) mm 86 3.375 3.5±0.79 / 679 98.4 3.875 4.0±0.79 / 914 101.6~111.1 4~4 1/8 4.8±0.79 / 914 114.3~130.2 4 1/2~5 1/8 5.6±0.79 / 965 133.4~146.1 5 1/4~5 3/4 6.4±0.79 / 1067 149.2~161.9 5 7/8~6 3/8 7.1±1.59 / 1067 165.1~177.8 6 1/2~7 7.9±1.59 / 1168 181.0~200.0 7 1/8~7 7/8 8.7±1.59 5.6±0.79 1626 203.2~225.4 8~8 7/8 9.5±1.59 6.4±0.79 1727 228.6~250.8 9~9 7/8 10.3±2.37 7.1±1.59 1829 254.0~276.2 10~10 7/8 11.1±2.37 7.9±1.59 1930 279.4 11 11.9±2.37 8.7±1.59 2032 Typically Size of Spiral Grooving
OD(In.) Screw depth(In.) Screw Leadin 4~4 3/8 6/32±1/32 36±1 4 1/2~5 1/8 7/32±1/32 38±1 5 1/4~5 3/4 1/4±1/32 42±1 5 7/8~6 3/8 9/32±1/16 42±1 6 1/2~7 5/16±1/16 46±1 7 1/8~7 7/8 11/32±1/16 64±1 8~8 7/8 3/8±1/16 68±1 9~9 7/8 13/32±3/32 72±1 Mechanical Performance OD Yield Strength Tensile Strength σb Elongation Reduction of are Impact Size σ0.2 Mpa(psi) δ4% % Ft.1b Mpa(psi) 3 1/8~6 3/4 ≥758 ≥827 ≥18 50 ≥50 -110,000 -120,000 7~10 ≥689 ≥758 ≥20 -100,000 -110,000 Sreel Mark Chemical Composition % C Si Mn P S Cr Mo Cu Al 4145H 0.42~0.48 0.15~0.35 0.90~1.20 ≤0.03 ≤0.03 0.90~1.20 0.15~0.25 ≤0.2 0.025~0.045 Other Elements:N≤0.015,Ni≤0.5 Size O.D(mm) I.D.(mm) Code Thread Length(mm) Weight(kg) 3-1/8 79.4 31.8(1-1/4) NC23-31 NC23 9140 298 3-1/2 88.9 38.1(1-1/2) NC26-35 NC26 9140 364 4-1/8 104.8 50.8(2) NC31-41 NC31 9140/9450 474/490 4-3/4 120.6 50.8(2) NC35-47 NC35 9140/9450 674/697 5 127.0 57.2(2-1/4) NC38-50 NC38 9140/9450 725/749 6 152.4 57.2(2-1/4) NC44-60 NC44 9140/9450 1125/1163 71.4(2-13/16) NC44-60 9140/9450 1022/1056 6-1/4 158.8 57.2(2-1/4) NC44-62 NC44 9140/9450 1237/1279 71.4(2-13/16) NC46-62 9140/9450 1134/1172 6-1/2 165.1 57.2(2-1/4) NC46-65 NC46 9140/9450 1352/1398 71.4(2-13/16) NC46-65 NC50 9140/9450 1249/1291 6-3/4 171.4 57.2(2-1/4) NC46-67 NC46 9140/9450 1471/1521 7 177.8 57.2(2-1/4) NC50-70 NC50 9140/9450 1597/1651 71.4(2-13/16) NC50-70 9140/9450 1494/1545 7-1/4 184.2 71.4(2-13/16) NC50-72 NC50 9140/9450 1625/1680 7-3/4 196.8 71.4(2-13/16) NC56-77 NC56 9140/9450 1895/1960 8 203.2 71.4(2-13/16) NC56-80 NC56/6-5/8REG 9140/9450 2040/2109 8-1/4 209.6 71.4(2-13/16) 6-5/8REG 6-5/8REG 9140/9450 2188/2263 9 228.6 71.4(2-13/16) NC61-90 NC61 9140/9450 2658/2748 9-1/2 241.3 76.2(2-13/16) 7-5/8REG 7-5/8REG 9140/9450 2954/3054 9-3/4 247.6 76.2(3) NC70-97 NC70 9140/9450 3127/3234 10 254.0 76.2(3) NC70-100 NC70 9140/9450 3308/3421 11 279.4 76.2(3) 8-5/8REG 8-5/8REG 9140/9450 4072/4210 Mechanical properties:<7 inch Drill Collar:Yield Strength≥758MPa,Tensile Strength≥965MPa,Four times elongation≥13%,Impact energy Ak≥54J,(Single impact work≥47J,Average≥54J)Hardness range 285HB~341HB≥7inch Drill Collar:Yield Strength≥689MPa,Tensile Strength≥931MPa,Four times elongation≥13%,Impact energy Ak≥54J,(Single impact work≥47J,Average≥54J) Hardness range 285HB~341HB
-
Production Process
- Packaing
Drill collars are equipped with threaded connections to join them with other components of the drill string.
- API Rotary Shouldered Connections: Standardized connections such as API NC38, NC50, and 6 5/8″ Reg.
- Premium Connections: Proprietary connections designed for enhanced performance, such as Hydril and VAM types.
Surface Finish
- Surface Hardening: Techniques like carburizing or nitriding may be applied to enhance surface hardness and wear resistance.
- Surface Finish Quality: Typically, a surface roughness of 63 microinches (1.6 microns) or smoother is maintained to reduce friction and wear.
Optional Features
- Spiral Grooves: For spiral drill collars, grooves are machined into the outer surface to reduce differential sticking.
- Stress Relief Features: Stress relief grooves or undercuts may be added to critical areas to reduce stress concentrations and enhance fatigue life.
Conclusion
Drill collars are indispensable in drilling operations, providing the weight, stability, and directional control necessary for efficient and effective drilling. Understanding the materials and technical specifications of drill collars is crucial for selecting the right components for specific drilling conditions.
Key Takeaways
- Material Selection: AISI 4145H-modified steel is common for its strength and durability, while non-magnetic materials are essential for directional drilling, and Inconel is used in highly corrosive environments.
- Mechanical Properties: High tensile and yield strength, along with adequate elongation and hardness, are critical for drill collar performance.
- Dimensional Accuracy: Precise dimensions ensure compatibility and optimal performance.
- Customized Features: Options like spiral grooves and stress relief features enhance functionality and reduce operational risks.
By adhering to these detailed specifications, drilling operations can achieve better efficiency, reduced wear on equipment, and improved overall performance.