Drilling, casing, tubing: The process of oil drilling
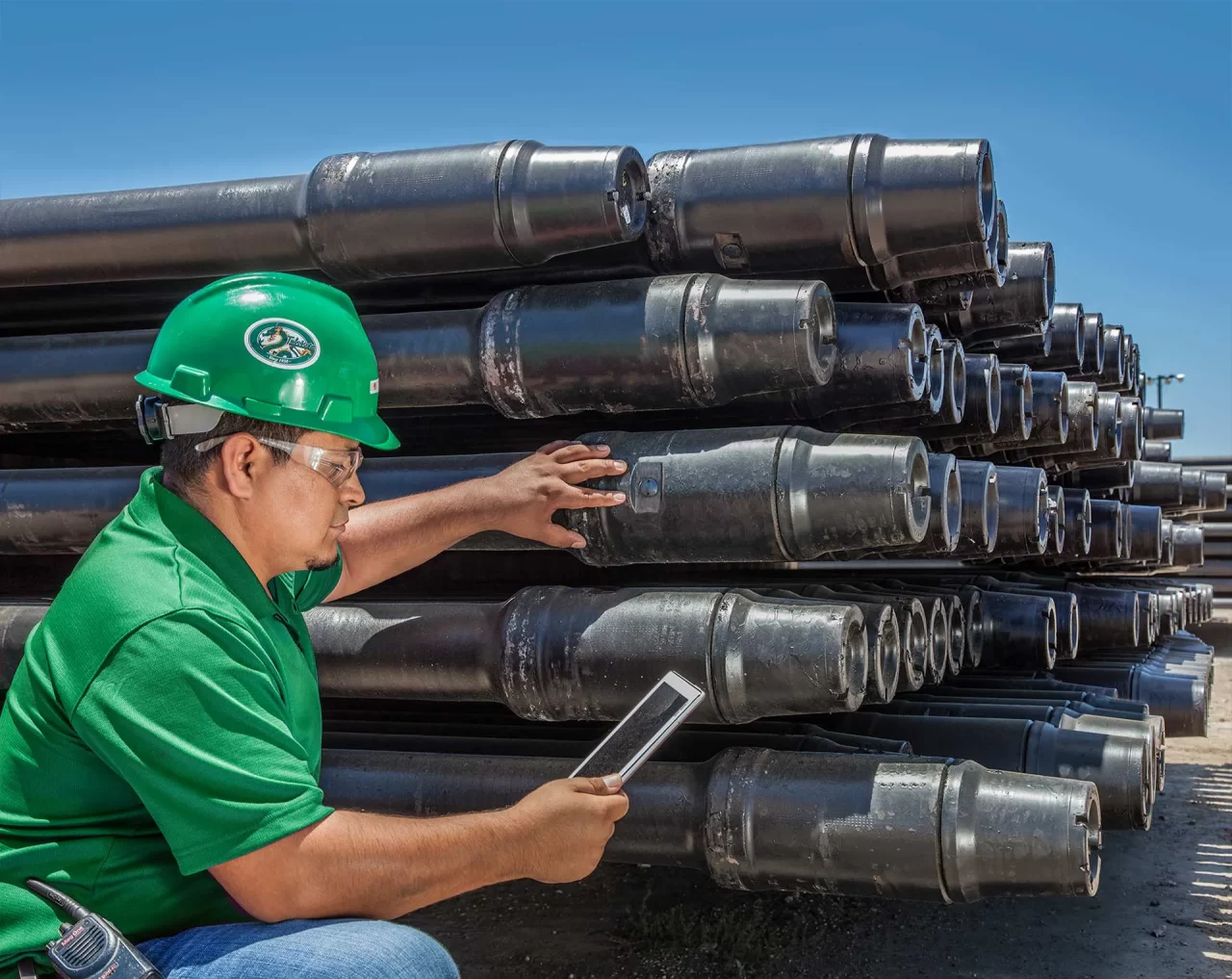
The journey of extracting oil or gas from beneath the Earth’s surface is indeed a complex and resource-intensive process. Yet, at its core, every wellbore undergoes three fundamental phases: drilling, casing, and tubing. Each phase plays a crucial role in ensuring the safe and efficient production of hydrocarbons. Let’s explore these phases in detail.
Phase 1: Drilling
Objective: The drilling phase is all about creating a path to the oil or gas reservoir. This involves penetrating the Earth’s surface and reaching the targeted underground formation where hydrocarbons are trapped.
- Process:
- Site Preparation: Before drilling begins, the site is prepared, which includes setting up the drilling rig and ensuring environmental and safety measures are in place.
- Drilling the Wellbore: A drill bit attached to a rotating drill string is used to bore through the earth. The bit is designed to cut through various rock formations, and drilling fluid (or mud) is circulated to cool the bit, carry cuttings to the surface, and maintain pressure.
- Directional Drilling: In many cases, wells are not drilled vertically. Directional drilling techniques are used to reach reservoirs that are not directly beneath the drilling rig.
- Challenges: Drilling must navigate through complex geological formations, manage pressure changes, and avoid hazards such as blowouts.
Phase 2: Casing
Objective: Casing involves lining the wellbore with steel pipe to stabilize it, prevent contamination of groundwater, and isolate different underground formations.
- Process:
- Running the Casing: After drilling to a certain depth, steel casing is inserted into the wellbore. The casing is typically installed in sections, with each section cemented in place.
- Cementing: Cement is pumped between the casing and the wellbore wall to secure the casing and prevent fluid migration between formations.
- Pressure Testing: Once the casing is in place, pressure tests are conducted to ensure its integrity and the effectiveness of the cementing.
- Types of Casing:
- Conductor Casing: The first casing set, providing structural support and preventing surface sediments from caving in.
- Surface Casing: Protects freshwater aquifers and provides a foundation for the blowout preventer.
- Intermediate Casing: Isolates unstable formations and zones with abnormal pressures.
- Production Casing: The final casing that runs through the production zone.
Phase 3: Tubing
Objective: Tubing is installed inside the casing to provide a conduit for oil or gas to flow to the surface. It is designed to withstand the pressures and temperatures of the produced fluids.
- Process:
- Running the Tubing: Tubing is smaller in diameter than casing and is inserted into the wellbore. It is typically removable and replaceable.
- Completion: This involves installing equipment such as packers, which seal the space between the tubing and casing, and perforating the casing in the production zone to allow hydrocarbons to enter the wellbore.
- Flow Testing: After completion, the well is tested to ensure it can produce hydrocarbons at the desired rate.
- Considerations:
- Material Selection: Tubing materials must be selected based on the corrosive nature of the fluids and the operating conditions.
- Well Control: Tubing facilitates well control operations, allowing for the safe management of well pressures.