Producción y aplicación de tuberías de acero sin costuras de paredes gruesas de gran diámetro
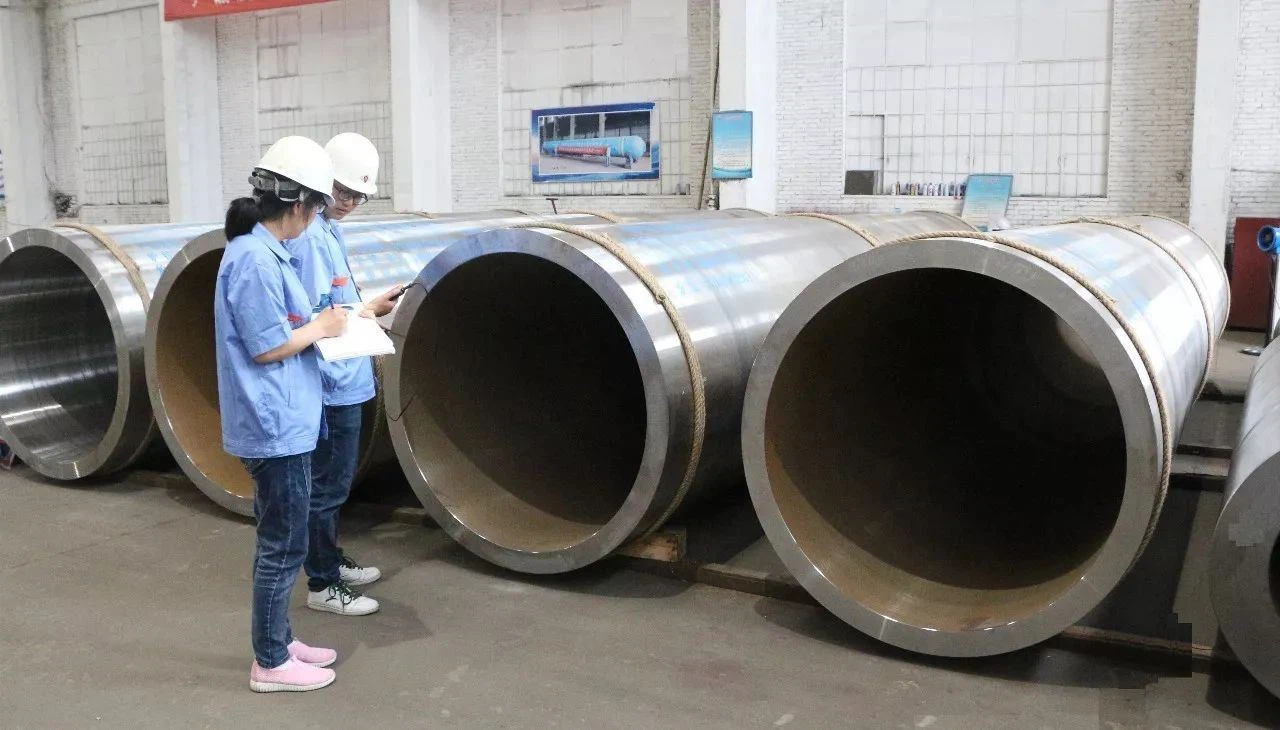
Producción y aplicación de tuberías de acero sin costuras de paredes gruesas de gran diámetro
Las tuberías de acero sin costuras de pared gruesa de gran diámetro son componentes críticos en industrias que requieren materiales robustos capaces de resistir altas presiones, temperaturas extremas, y tensiones mecánicas. Estas tuberías, caracterizado por diámetros externos que exceden 200 mm y espesores de la pared a menudo mayores que 20 milímetros, son esenciales en aplicaciones como cilindros hidráulicos de alta presión, oleoductos y gasoductos, y maquinaria pesada. Este documento explora sus procesos de producción., propiedades del material, comportamiento mecánico, y aplicaciones prácticas, con énfasis en los estándares materiales internacionales.
1. Procesos de producción
La fabricación de tuberías de acero sin costuras de paredes gruesas de gran diámetro implica técnicas sofisticadas para garantizar la integridad estructural y la precisión dimensional. A continuación se presentan las etapas clave:
1.1 Selección de materia prima y preparación de palanquillas
La producción comienza con billets de acero de alta calidad, típicamente producido a través del horno de arco eléctrico (EAF) o horno de oxígeno básico (BOF) metodos. Los materiales comunes incluyen aceros de carbono (p.ej., ASTM A106 Gr.B, 20#) y aceros de aleación (p.ej., 42CrMo, 34CrMo4). Se inspeccionan billets para la composición química y defectos internos utilizando técnicas como espectrometría y pruebas ultrasónicas.
1.2 Perforación en caliente
El tocho se calienta a 1100–1250 ° C en un horno de hogar rotativo, luego perforó usando un molino de perforación de Mannesmann para crear un caparazón hueco. Este proceso asegura una estructura perfecta, con diámetros externos típicos que van desde 100 mm a 500 Mm y espesores de la pared de 20–80 mm para tuberías de gran diámetro.
1.3 Rolling o extrusión en caliente
La carcasa hueco se procesa aún más a través del rodamiento en caliente (Usando una fábrica de mandril) o extrusión caliente. Diámetros de trajes de rodadura caliente hasta 600 milímetros, Mientras que la extrusión se prefiere para las secciones de paredes gruesas (Relación de espesor de la pared/diámetro exterior >0.1), ofreciendo uniformidad y fuerza superiores. Las temperaturas se mantienen por encima de 1000 ° C para mejorar la ductilidad.
1.4 Acabado en frío (Opcional)
Para aplicaciones que requieren tolerancias precisas (p.ej., ± 0.1 mm) o superficies suaves, Se aplica el dibujo en frío o el rodamiento en frío. Esto aumenta la fuerza del rendimiento a través del endurecimiento del trabajo y refina las dimensiones de la tubería, crítico para barriles de cilindro hidráulico.
1.5 Tratamiento térmico
El tratamiento térmico mejora las propiedades mecánicas:
- Normalizando: Calentamiento a 850–900 ° C y enfriamiento de aire para aliviar el estrés.
- Temple y revenido: Apagado a 860 ° C y templado a 500–600 ° C (p.ej., para 42crmo) Para lograr la alta fuerza y la dureza.
Las superficies internas pueden ser perfeccionadas hasta un acabado de RA ≤ 0.4 μm para aplicaciones hidráulicas.
1.6 Control de calidad
Las tuberías terminadas se someten a pruebas rigurosas, incluyendo pruebas de presión hidrostática (arriba a 100 MPa), detección de defectos ultrasónicos, y cheques dimensionales, Asegurar el cumplimiento de estándares como ASTM A519, EN 10297-1, o GB/T 8162.
2. Especificaciones y propiedades del material
La elección del material depende de la presión, temperatura, y las condiciones ambientales. Dos tablas se proporcionan a continuación: uno para calificaciones chinas comunes (Normas GB) y otro para europeo (EN) y americano (ASTM/ASME) calificaciones ampliamente utilizadas en los mercados internacionales.
2.1 Estándares materiales chinos (ES)
Calificación | Estándar | Fuerza de producción (MPa) | Resistencia a la tracción (MPa) | Rango de espesor de pared (milímetros) | Elementos de aleación clave |
---|---|---|---|---|---|
20# | GB/T 8162 | ≥410 | ≥550 | 10–50 | c: 0.17–0.24, Minnesota: 0.35–0,65 |
45# | GB/T 8162 | ≥600 | ≥750 | 10–50 | c: 0.42–0,50, Minnesota: 0.50–0,80 |
16Minnesota (Q345) | GB/T 1591 | ≥345 | ≥470 | 15–60 | c: ≤0,20, Minnesota: 1.00–1.60 |
42CrMo | GB/T 3077 | ≥650 | ≥850 | 20–80 | c: 0.38–0.45, cr: 0.90–1.20, Mes: 0.15–0.25 |
2.2 Estándares materiales europeos y americanos (En y astm/asme)
Calificación | Estándar | Fuerza de producción (MPa) | Resistencia a la tracción (MPa) | Rango de espesor de pared (milímetros) | Elementos de aleación clave |
---|---|---|---|---|---|
P355N | EN 10216-3 | ≥355 | 490–630 | 10–60 | c: ≤0,20, Minnesota: 0.90–1.70 |
34CrMo4 | EN 10297-1 | ≥650 | ≥900 | 20–80 | c: 0.30–0.37, cr: 0.90–1.20, Mes: 0.15–0,30 |
A106 Gr.B | ASTM A106 | ≥240 | ≥415 | 10–50 | c: ≤0,30, Minnesota: 0.29–1,06 |
A519 4140 | ASTM A519 | ≥655 | ≥855 | 20–80 | c: 0.38–0.43, cr: 0.80–1,10, Mes: 0.15–0.25 |
A335 P22 | ASTM A335 | ≥205 | ≥415 | 15–60 | c: ≤0,15, cr: 1.90–2,60, Mes: 0.87–1,13 |
Notas: El rendimiento y las resistencias a la tracción pueden variar según el tratamiento térmico y el grosor de la pared. Las calificaciones europeas como P355N y 34CRMO4 son comunes en los vasos a presión, mientras que ASTM califica como A519 4140 Excel en aplicaciones hidráulicas de alta presión.
3. Análisis mecánico
3.1 Estrés de aro
Estrés de aro (S_H) ¿Es la tensión dominante en las tuberías presurizadas?:
S_h = (P × D_i) / (2 × t)
Ejemplo: P = 80 MPa, D_i = 300 milímetros, t = 40 milímetros, S_h = (80 × 300) / (2 × 40) = 300 MPa, seguro para A519 4140 (S_y = 655 MPa).
3.2 Diseño de grosor de pared
Espesor mínimo de pared (t_min) incorpora un factor de seguridad (SF = 2):
t_min = (P × D_i) / (2 × S_Y / SF)
Para p = 80 MPa, D_i = 300 milímetros, S_y = 655 MPa, t_min = (80 × 300) / (2 × 655 / 2) = 36.64 milímetros, Entonces t = 40 mm es adecuado.
3.3 Presión de ráfaga
Presión de ráfaga (P_burst) indica el umbral de falla:
P_burst = (2 × S_U × T) / D_i
Para A519 4140 (Σ_u = 855 MPa), P_burst = (2 × 855 × 40) / 300 = 228 MPa, un margen significativo arriba 80 MPa.
3.4 Consideraciones de fatiga
Para carga cíclica, el límite de resistencia (σ_e ≈ 0.4-0.5 × σ_u) debe exceder la amplitud del estrés. Para 34crmo4 (Σ_u = 900 MPa), σ_e ≈ 400–450 MPa, Asegurar la durabilidad.
4. Aplicaciones
4.1 Cilindros hidráulicos de alta presión
Grados como A519 4140 y 34CRMO4 se utilizan en equipos pesados (p.ej., excavadoras, prensas), Manejo de 50–100 MPa y fuerzas a 1000 montones.
4.2 Transporte de petróleo y gas
Tuberías A106 Gr.B y P355N con paredes de 30–60 mm transportan hidrocarburos de alta presión, resistir la corrosión y la fatiga.
4.3 Maquinaria pesada y sistemas marinos
En grúas y plataformas en alta mar, 42Las tuberías CRMO o A335 P22 soportan cargas dinámicas y entornos duros.
4.4 Generación de energía
A335 P22 y grados similares en las calderas de plantas de energía manejan vapor de alta temperatura de hasta 540 ° C y 10 MPa.
5. Ejemplo de diseño práctico
Para un cilindro hidráulico con p = 90 MPa, diámetro exterior = 400 milímetros, Usando A519 4140:
- D_i = 340 milímetros, t = 30 milímetros
- S_h = (90 × 340) / (2 × 30) = 510 MPa (<655 MPa)
- t_min = (90 × 340) / (2 × 655 / 2) = 46.72 milímetros (requiere una pared más gruesa)
- P_burst = (2 × 855 × 30) / 340 = 150.88 MPa
A 40 mm rave de pared σ_h = 382.5 MPa, Asegurar la seguridad con el ajuste SF.