Galvanized Steel Pipe – Hot Dip Galvanized Steel Pipe
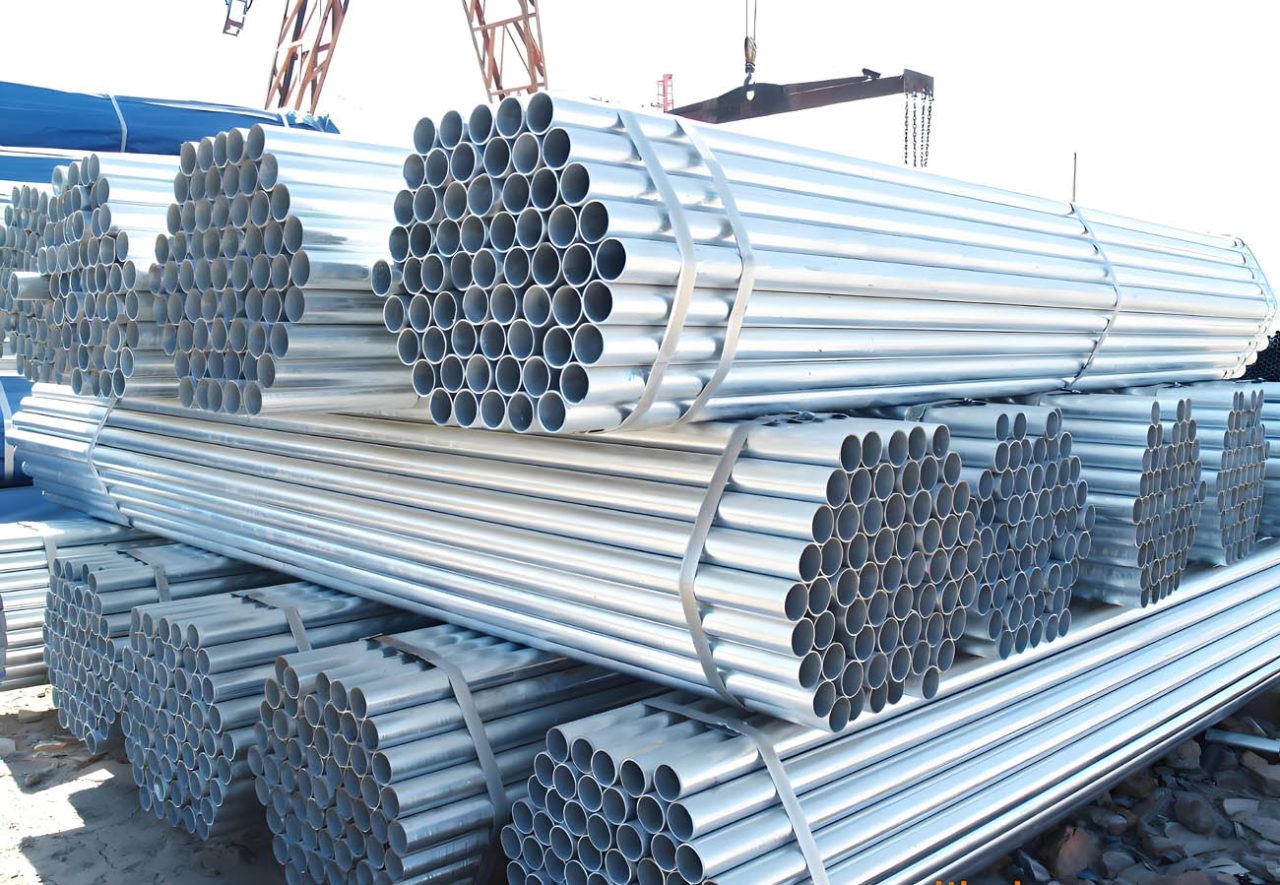
Galvanized Steel Pipe Overview
Galvanized steel pipes are steel pipes that have been coated with a layer of zinc to protect against corrosion. This process, known as galvanization, helps to extend the life of the pipe by preventing rust and other forms of corrosion. These pipes are commonly used in various applications, including plumbing, water supply, fencing, and structural support.
Key Features of Galvanized Steel Pipe
- Corrosion Resistance:
- The zinc coating protects the steel from environmental elements, preventing rust and corrosion.
- Durability:
- Galvanized steel pipes are known for their long lifespan and ability to withstand harsh environmental conditions.
- Cost-Effective:
- While slightly more expensive than non-coated steel, the extended lifespan and reduced maintenance costs make them a cost-effective choice over time.
- Versatility:
- Used in a wide range of applications including plumbing, irrigation, fencing, and construction.
- Strength:
- Maintains the inherent strength of steel, making it suitable for structural applications.
Types and Dimensions of Galvanized Steel Pipe
Galvanized steel pipes come in various types and dimensions to suit different needs:
- Types:
- Pre-Galvanized Pipe: The pipe is coated with zinc before it is formed into its final shape.
- Hot-Dip Galvanized Pipe: The completed steel pipe is dipped into molten zinc, coating both the interior and exterior surfaces.
- Dimensions:
- Diameter: Typically ranges from 1/2 inch to 12 inches in nominal diameter.
- Wall Thickness: Varies based on the diameter and application, commonly found in standard schedules such as Schedule 40 and Schedule 80.
- Length: Standard lengths are usually 21 feet (6.4 meters) or 24 feet (7.3 meters), but custom lengths can be manufactured.
Difference Between Hot-Dip Galvanizing and Pre-Galvanizing
Hot-Dip Galvanizing (HDG Pipe)
Zinc has been used to protect iron and steel from corrosion for over a hundred years. The hot dip galvanizing process involves dipping the steel into a vat of molten zinc. The zinc bonds to the iron, forming a layer that prevents rust and corrosion. Hot dip galvanized pipe is used in a wide variety of applications, from residential to industrial. It is available in a variety of shapes and sizes, making it versatile for both new construction and repairs. When properly maintained, hot dip galvanized pipe can last for decades, making it an economical choice for both homeowners and businesses.
Pre-Galvanizing (Pre-Galvanized Pipes)
The pre-galvanized pipe is a steel pipe that has been coil coated with a zinc-based metallic coating prior to fabrication. The steel pipe is roll-formed, welded where necessary, and then passed through a high-speed set of rollers that form the desired shape. The zinc coating provides excellent corrosion resistance to the base metal, and this type of pipe is often used in construction and other applications where a long-lasting finish is required. While, due to the manufacturing method, the welding seam inside the pipe cannot be coated with zinc spray, so rust may still exist.
Galvanization Process
- Surface Preparation:
- The steel pipe is cleaned to remove impurities such as oil, grease, and rust, typically using a combination of degreasing, pickling in acid, and fluxing.
- Galvanizing:
- The cleaned steel pipe is dipped into a bath of molten zinc, typically heated to around 450°C (842°F). The zinc chemically bonds with the steel, forming a protective layer.
- Cooling:
- After galvanizing, the pipe is cooled in a quench tank to solidify the zinc coating.
- Inspection:
- Finally, the galvanized pipe is inspected for coating thickness, uniformity, and overall quality.
Applications of Galvanized Steel Pipe
- Plumbing: Used for water supply lines, especially in outdoor and industrial environments.
- Construction: Structural applications such as scaffolding, supports, and handrails.
- Agriculture: Irrigation systems and fencing.
- Transportation: Guardrails and road signs.
- HVAC Systems: Ductwork and ventilation.
Comparison with Other Pipe Materials
- Vs. Black Steel Pipe:
- Corrosion Resistance: Galvanized pipes are more resistant to corrosion.
- Cost: Galvanized pipes are generally more expensive due to the zinc coating process.
- Vs. PVC Pipe:
- Strength: Galvanized steel is stronger and more durable.
- Corrosion: PVC does not rust but is less strong compared to galvanized steel.
DIMENSIONS AND SIZES OF GALVANIZED PIPE
This section will show you the different outer diameters of the pipes manufactured by TUSPIPE, including:1 1/4 galvanized pipe, 1-1/2 galvanized pipe, 2 galvanized steel pipe, 2 1 2 galvanized pipe, 3 galvanized pipe, 4 inch galvanized pipe, 6 galvanized pipe, 10 ft galvanized pipe.
DN | O.D. | W.T. | |||||||||||||||
---|---|---|---|---|---|---|---|---|---|---|---|---|---|---|---|---|---|
Inch | mm | SCH5S | SCH10S | SCH10 | SCH20 | SCH30 | SCH40 | SCH60 | SCH80 | SCH100 | SCH120 | SCH140 | SCH160 | Sth | XS | XXS | |
50 | 2″ | 60.3 | 1.65 | 2.77 | – | – | – | 3.91 | – | 5.54 | – | – | – | 8.74 | 3.91 | 5.54 | 11.07 |
65 | 2 1/2″ | 73 | 2.11 | 3.05 | – | – | – | 5.16 | – | 7.01 | – | – | – | 9.53 | 5.16 | 7.01 | 14.02 |
80 | 3″ | 88.9 | 2.11 | 3.05 | – | – | – | 5.49 | – | 7.62 | – | – | – | 11.13 | 5.49 | 7.52 | 15.24 |
90 | 3 1/2″ | 101.6 | 2.11 | 3.05 | – | – | – | 5.74 | – | 8.08 | – | – | – | – | 5.74 | 8.08 | – |
100 | 4″ | 114.3 | 2.11 | 3.05 | – | – | – | 6.02 | – | 8.58 | – | 11.13 | – | 13.49 | 6.02 | 8.56 | 17.12 |
125 | 5″ | 141.3 | 2.77 | 3.4 | – | – | – | 6.55 | – | 9.53 | – | 12.7 | – | 15.88 | 6.55 | 9.53 | 18.05 |
150 | 6″ | 168.3 | 2.77 | 3.4 | – | – | – | 7.11 | – | 10.97 | – | 14.27 | – | 18.26 | 7.11 | 10.97 | 21.95 |
200 | 8″ | 219.1 | 2.77 | 3.76 | – | 6.35 | 7.04 | 8.18 | 10.31 | 12.7 | 15.09 | 18.26 | 20.62 | 23.01 | 8.18 | 12.7 | 22.23 |
250 | 10″ | 273.1 | 3.4 | 4.19 | – | 6.35 | 7.8 | 9.27 | 12.7 | 15.09 | 18.26 | 21.44 | 25.4 | 28.58 | 9.27 | 12.7 | 25.4 |
300 | 12″ | 323.9 | 3.96 | 4.57 | – | 6.35 | 8.38 | 10.31 | 14.27 | 17.48 | 21.44 | 25.4 | 28.58 | 33.32 | 9.53 | 12.7 | 25.4 |
350 | 14″ | 355.5 | 3.96 | 4.78 | 6.35 | 7.92 | 9.53 | 11.13 | 15.09 | 19.05 | 23.83 | 27.79 | 31.75 | 35.71 | 9.53 | 12.7 | – |
400 | 16″ | 406.4 | 4.19 | 4.78 | 6.35 | 7.92 | 9.53 | 12.7 | 16.66 | 21.44 | 26.19 | 30.96 | 36.53 | 40.49 | 9.53 | 12.7 | – |
450 | 18″ | 457.2 | 4.19 | 4.78 | 6.35 | 7.92 | 11.13 | 14.27 | 19.05 | 23.83 | 39.36 | 34.93 | 39.67 | 45.24 | – | – | – |
500 | 20″ | 508 | 4.78 | 5.54 | 6.35 | 9.53 | 12.7 | 15.09 | 20.62 | 26.19 | 32.54 | 38.1 | 44.45 | 50.01 | – | – | – |
550 | 22″ | 558.8 | 4.78 | 5.54 | 6.35 | 9.53 | 12.7 | – | 22.23 | 28.58 | 34.93 | 41.28 | 47.63 | 53.98 | – | – | – |
600 | 24″ | 609.6 | 5.54 | 6.35 | 6.35 | 9.53 | 14.27 | 17.48 | 24.61 | 30.96 | 38.89 | 46.02 | 52.37 | 59.54 | – | – | – |
Maintenance and Lifespan
- Maintenance:
- Galvanized steel pipes require minimal maintenance due to their corrosion-resistant properties. Regular inspections can help identify any potential issues early.
- Lifespan:
- Typically, galvanized steel pipes can last between 40 to 50 years in rural areas and up to 25 years in severely polluted urban and coastal environments.
Referred Standards
- ASTM A53: Standard Specification for Pipe, Steel, Black and Hot-Dipped, Zinc-Coated, Welded, and Seamless.
- ASTM A123/A123M: Standard Specification for Zinc (Hot-Dip Galvanized) Coatings on Iron and Steel Products.
- BS 1387: Specification for screwed and socketed steel tubes and tubulars and for plain end steel tubes suitable for welding or for screwing to BS 21 pipe threads.
Conclusion
Galvanized steel pipes offer a robust and durable solution for a wide range of applications, thanks to their enhanced corrosion resistance and strength. By following stringent manufacturing processes and standards, these pipes provide a reliable and long-lasting option for both industrial and residential purposes.