Bengkok Paip : keluli karbon, keluli aloi dan keluli tahan karat
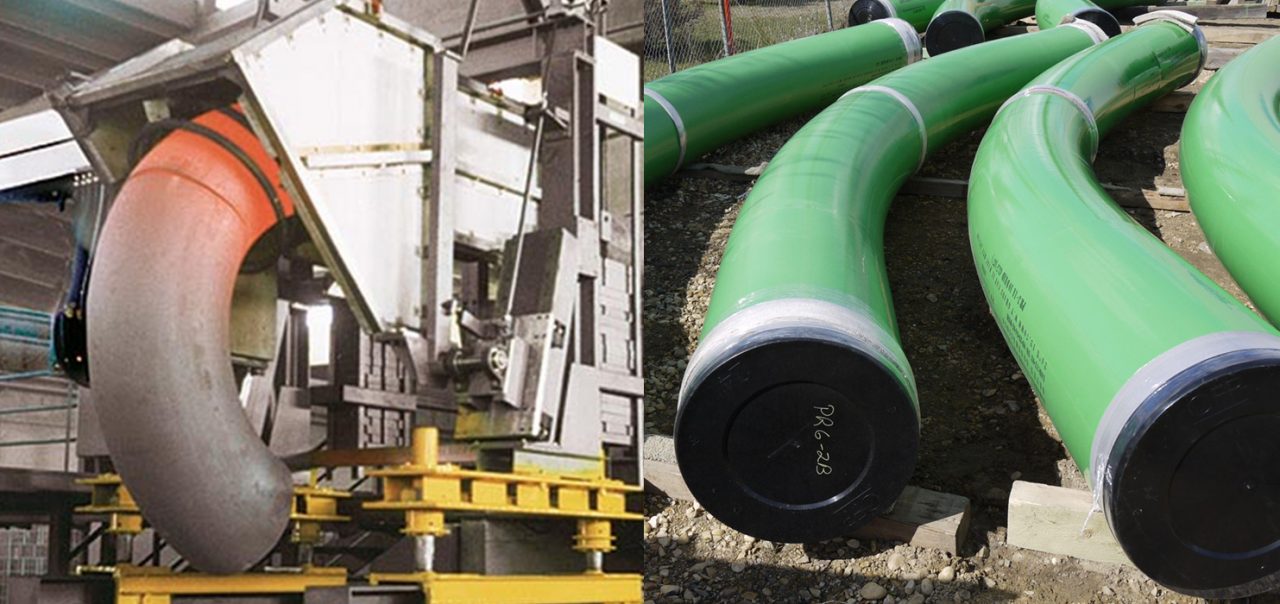
The steel bend is a common connecting piece in the pipe system. It is used to link two pipes of the same or different nominal bore turning direction due to relevant angles according to different bending radius. A steel pipe bend is used in almost every machine. Our company adopts advanced production technologies to bend, stamp, push forming, compression molding and machining to manufacture the steel bend.
Steel bends are mainly used in oil, gas and liquid transportation and play an important role in airplanes and aircraft engines. Selain itu, they are widely used in electric, kimia, ship building, heat supply system, paper making, metallurgic and other industries.
Raw Materials of the Steel Bend
Our company provides carbon steel pipe bend, alloy steel bend, stainless steel bend, low temperature steel bend and high performance steel pipe bend. Maklumat terperinci disenaraikan di bawah.
Keluli Karbon: ASTM/ASME A234 WPB、WPC
Keluli Aloi: ASTM/ASME A234 WP 1-WP 12-WP 11-WP 22-WP 5-WP 91-WP 911
Keluli Tahan Karat: ASTM/ASME A403 WP 304-304L-304H-304LN-304N, ASTM/ASME A403 WP 316-316L-316H-316LN-316N-316Ti, ASTM/ASME A403 WP 321-321H ASTM/ASME A403 WP 347-347H
Keluli Suhu Rendah: ASTM/ASME A402 WPL 3-WPL 6
Keluli Berprestasi Tinggi: ASTM/ASME A860 WPHY 42-46-52-60-65-70
Specifications of the Steel Bend
Bend Type: | Bend Type: Bengkok Paip, Steel Pipe Bend, Hot Bend, Induction Bend, Induction Hot Bend | ||
Seamless Bend | Straight Seam Bend | Spiral Pipe Bend | |
Diameter Keluar | 1/2″~24″ | 4″~24″ | 8″ ~78″ |
Ketebalan Dinding | 3 mm ~ 200 mm | ||
Bending Radius | R=2.5D/3D/4D/5D/6D/7D/8D/9D/10D/ 20D | ||
Sudut | 15/30/45/60/90/135/180 deg |
Standards Available for the Pipe Bend
Our company offers steel bend of different standards. Detailed information is listed bellow.
ASME B16.49-2007
ASME B16.25-2007
SY/T5257-2004
DL/T515-2004 GD2000 GD87-1101
As an experienced pipe fittings steel bend manufacturer and supplier in China, we offer a wide variety of products, including flanged pipe, pipe fittings steel tee, paip keluli, and plate steel pipe flange, dll.
Manufacture of Induction Bends
Induction bends are formed in a factory by passing a length of straight pipe through an induction bending machine. This machine uses an induction coil to heat a narrow band of the pipe material. The leading end of the pipe is clamped to a pivot arm.
As the pipe is pushed through the machine, a bend with the desired radius of curvature is produced. The heated material just beyond the induction coil is quenched with a water spray on the outside surface of the pipe. Thermal expansion of the narrow heated section of pipe is restrained due to the unheated pipe on either side, which causes diameter shrinkage upon cooling.
The induction bending process also causes wall thickening on the intrados and thinning on the extrados. The severity of thickening/thinning is dependant on the bending temperature, the speed at which the pipe is pushed through the induction coil, the placement of the induction coil relative to the pipe (closer to the intrados or extrados), and other factors.
Most induction bends are manufactured with tangent ends (straight sections) that are not affected by the induction bending process. Field welds are made or pipe pup sections are attached to the unaffected tangent ends, allowing for fitup similar to that found when welding straight sections of pipe together.
Induction bends come in standard bend angles (e.g. 45°, 90°, dll.) or can be custom made to specific bend angles. Compound bends (out-of-plane) bends in a single joint of pipe can also be produced. The bend radius is specified as a function of the diameter. Contohnya, common bend radii for induction bends are 3D, 5D and 7D, where D is the nominal pipe diameter.
Induction bending of 48 inch line pipe | View on induction coil and heated zone during bending |
What is Induction Bending?
Induction Bending is a controlled means of bending pipes through the application of local heating using high frequency induced electrical power.
Originally used for the purpose of surface hardening steels, induction technology when used in pipe bending consists basically of an induction coil placed around the pipe to be bent. The induction coil heats a narrow, circumferential section of the pipe to a temperature of between 850 dan 1100 °rees Celsius (dependant on the material to be formed). As the correct bending temperature range is reached, the pipe is moved slowly through the induction coil whilst the bending force is applied by a fixed radius arm arrangement.