Analisis Teknologi Kimpalan Inconel 625 dan paip keluli aloi p22
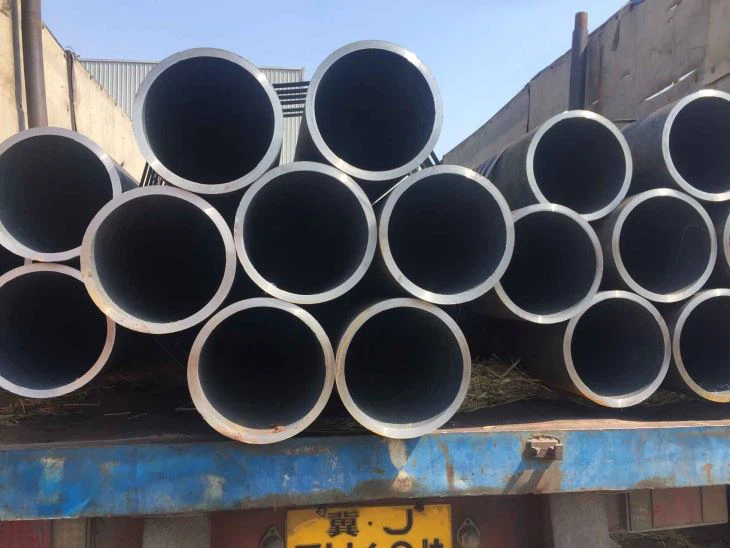
Analisis Teknologi Kimpalan Inconel 625 dan paip keluli aloi p22
1. pengenalan
Kimpalan bahan yang berbeza, seperti superalloy berasaskan nikel (cth., Inconel 625) dan keluli rendah aloi (cth., P22), membentangkan cabaran yang ketara kerana sifat metalurgi dan mekanikal mereka yang berbeza. Analisis ini secara komprehensif mengkaji teknik kimpalan, Parameter proses, kecacatan biasa, dan rawatan pasca kimpalan untuk bahan-bahan ini, disokong oleh piawaian industri dan kajian kes eksperimen.
Inconel 625 komposisi kimia paip aloi dan sifat mekanikal
Komposisi kimia dan sifat mekanik Inconel 625 Paip aloi adalah seperti berikut:
2. Ciri -ciri bahan
2.1 Inconel 625 Aloi
Komposisi Kimia ():
unsur | Dalam | Cr | Mo | Fe | NB+TA | C | Mn | Dan |
---|---|---|---|---|---|---|---|---|
% | ≥58 | 20-23 | 8-10 | ≤5 | 3.15–4.15 | ≤0.10 | ≤0.50 | ≤0.50 |
Sifat Mekanikal ():
- Kekuatan Tegangan: 827 MPa (min)
- Kekuatan Hasil (0.2% mengimbangi): 414 MPa (min)
- Pemanjangan: 35% (min)
- Kekerasan: ≤287 Hb (Keadaan Annealed)
- Takat Lebur: 1,290-1,350 ° C.
Inconel 625 mempamerkan rintangan pengoksidaan yang luar biasa sehingga 980 ° C dan rintangan kakisan dalam persekitaran yang kaya dengan klorida kerana kandungan CR dan MO yang tinggi .
2.2 P22 Alloy Steel
Komposisi Kimia ():
unsur | C | Cr | Mo | Mn | Dan | Fe |
---|---|---|---|---|---|---|
% | 0.05–0.15 | 1.90–2.60 | 0.87–1.13 | 0.30–0.61 | ≤0.50 | Bal. |
Sifat Mekanikal ():
- Kekuatan Tegangan: ≥415 MPa
- Kekuatan Hasil: ≥205 MPa
- Pemanjangan: ≥30%
- Kekerasan: 180-240 HB (selepas rawatan haba)
P22 adalah keluli cr-mo yang dioptimumkan untuk perkhidmatan suhu tinggi (sehingga 550-600 ° C.), dengan kebolehkalasan yang baik dan rintangan merayap
3. Cabaran kimpalan untuk sendi yang berbeza
3.1 Ketidakserasian metalurgi
- Pekali Pengembangan Terma (Cte) Tidak sepadan:
Inconel 625 (14.7 μm/m ° C.) lwn. P22 (12.3 μm/m ° C.) menjana tekanan sisa semasa penyejukan . - Migrasi Karbon:
Penyebaran Karbon dari P22 ke Inconel 625 Bentuk karbida rapuh (cth., CR23C6) di sempadan gabungan, mengurangkan ketangguhan . - Kesan pencairan:
Kandungan Fe yang tinggi di kolam kimpalan (dari p22) merendahkan rintangan kakisan Inconel 625 .
3.2 Pengurusan Kecerunan Thermal
- Kawalan input haba:
Input haba yang berlebihan di Inconel 625 menyebabkan gandum kasar, Walaupun tidak mencukupi untuk p22 meningkatkan risiko retak hidrogen .
4. Proses dan parameter kimpalan
4.1 Kaedah Kimpalan yang Disyorkan
Pasangan bahan | Kaedah pilihan | Pertimbangan Utama |
---|---|---|
Inconel 625 -inticonel 625 | TIG (GTAW), Kimpalan laser | Input haba yang rendah, kimpalan autogen |
P22 -P22 | SMAW, GTAW | Panaskan (170-190 ° C.), pelepasan tekanan pasca kimpalan |
Inconel 625 -P22 | TIG dengan pengisi berasaskan NI | Lapisan penampan, Pencairan terkawal |
4.2 Parameter proses untuk kimpalan yang berbeza
Kajian Kes: Inconel 625 hingga p22 menggunakan pengisi Ernicrmo-3 ():
- Pemanasan awal: 150-200 ° C. (P22 SAHAJA) untuk meminimumkan tekanan haba.
- Suhu interpass: ≤150 ° C. (menghalang pertumbuhan bijirin yang berlebihan di Inconel 625).
- Input Haba: 0.8-1.2 kJ/mm (TIG), 1.5-2.0 kJ/mm (SMAW).
- Perisai Gas: Argon + 2-5% H2 untuk kimpalan TIG untuk mengurangkan pengoksidaan.
Kimpalan rasuk elektron (EMB):
Digunakan untuk CUCRZR/Inconel 625 sendi dalam aplikasi vakum, mencapai haz sempit dan herotan minimum .
5. Pemilihan bahan pengisi
5.1 Inconel 625 Kimpalan
- Pengisi yang sepadan: Ernichrmo-3 (AWS A5.14) memastikan ketahanan kakisan dan pariti mekanikal .
- Kimpalan yang berbeza: Inconel Filler Metal 625 (Ernichrmo-10) kerana menyertai keluli tahan karat atau p22, Mengurangkan penghijrahan karbon .
5.2 P22 Kimpalan
- Pengisi yang sepadan: E9018-B3 (SMAW) atau ER90S-B3 (GTAW) Untuk keserasian keluli Cr-Mo .
6. Kecacatan kimpalan biasa dan pengurangan
6.1 Inconel 625
- Retak panas: Disebabkan oleh kekotoran S/P; dikurangkan menggunakan pengisi kemelut tinggi dan input haba yang rendah .
- Keliangan: Elakkan pencemaran kelembapan dalam pelindung gas (titik embun ≤ -50 ° C) .
6.2 P22
- Retak yang disebabkan oleh hidrogen: Dikawal melalui pemanasan, elektrod hidrogen rendah, dan dehidrogenasi pasca kimpalan pada suhu 300-350 ° C .
6.3 Sendi yang berbeza
- Fasa intermetallic rapuh: Gunakan penampan berasaskan NI (cth., Ernichrmo-3) Untuk menyerap pencairan FE .
7. Rawatan Haba Selepas Kimpalan (PWHT)
bahan | Parameter PWHT | Tujuan |
---|---|---|
Inconel 625 | Penyelesaian Penyepuh: 980-1,020 ° C., penyejukan cepat | Kembalikan rintangan kakisan |
P22 | Melegakan tekanan: 650-700 ° C., 1-2 jam | Mengurangkan tekanan sisa |
Inconel 625 -P22 | Elakkan penyepuh P22 di atas 750 ° C (menghalang karbida kasar) | Tekanan keseimbangan dan struktur mikro |
Hasil kajian: PWHT pada suhu 650 ° C 10 jam meningkatkan rintangan sscc dalam f22/inconel 625 Sendi oleh 40% .
8. Piawaian dan pematuhan industri
- Asme BPVC Action IX: Memenuhi syarat prosedur kimpalan dan kakitangan untuk aplikasi dandang/tekanan .
- AWS D10.18: Panduan kimpalan aloi ni-cr-mo dalam persekitaran yang menghakis.
- ASTM B444: Menentukan Inconel 625 Pembuatan dan ujian paip .
9. Kajian kes
9.1 Paip reaktor nuklear (Inconel 625 -P22)
- Permohonan: Tiub penjana stim dalam reaktor air bertekanan.
- Kaedah Kimpalan: Tig sempit dengan pengisi Ernicrmo-3.
- Hasilnya: Tiada retak atau kakisan selepas 10,000 jam perkhidmatan .
9.2 Paip petrokimia (P22 -P22)
- Permohonan: Penghantaran gas suhu tinggi.
- Kaedah Kimpalan: Smaw dengan E9018-B3, pelepasan tekanan pasca kimpalan pada suhu 680 ° C.
- Hasilnya: Pematuhan dengan API 1104 piawaian; tiada keretakan hidrogen yang dikesan .
10. Trend masa depan
- Kimpalan hibrid laser: Menggabungkan laser dan GMAW untuk kelajuan dan ketepatan yang lebih tinggi di Inconel 625 .
- Pembuatan Aditif: Wayar-arc untuk membaiki inconel 625 komponen dengan haz minimum .
Sifat mekanikal
Inconel 625 paip aloi mempunyai sifat mekanikal yang sangat baik, seperti berikut:
- Kekuatan tegangan : ≥120 MPa (keadaan anil).
- Kekuatan hasil : ≥827 MPa (keadaan anil).
- Pemanjangan : ≥60% (keadaan anil).
- Kekerasan : Hb ≤ 287 (keadaan anil).
- Prestasi suhu tinggi : Mengekalkan kekuatan tinggi dan rintangan pengoksidaan dalam persekitaran suhu tinggi, dengan suhu operasi maksimum sehingga 2000 ° F (kira -kira 1093 ° C.).
- Rintangan kakisan : Sangat tahan terhadap kakisan pitting dan celah dalam asid pengoksidaan, mengurangkan persekitaran asid dan klorida.
Ciri-ciri
- Rintangan kakisan : Inconel 625 mempunyai rintangan yang sangat baik terhadap pelbagai media yang menghakis, termasuk asid nitrik, asid sulfurik, asid fosforik dan asid hidroklorik.
- Kestabilan suhu tinggi : Ia dapat mengekalkan sifat mekanikal yang baik dan rintangan pengoksidaan pada suhu tinggi.
- Prestasi memproses : Ia mempunyai kebolehkalasan dan kebolehkerjaan yang baik, dan sesuai untuk pembuatan bahagian pelbagai bentuk kompleks.
Ringkasnya, Inconel 625 Paip aloi digunakan secara meluas dalam bahan kimia, marin, tenaga nuklear dan bidang lain kerana rintangan kakisan mereka, Kestabilan suhu tinggi dan sifat mekanikal.
P22 Paip Komposisi Kimia dan Sifat Mekanikal
Komposisi kimia dan sifat mekanikal paip keluli aloi p22 adalah seperti berikut:
Komposisi kimia
Komponen kimia utama paip keluli aloi p22 termasuk kromium (Cr), molibdenum (Mo), Karbon (C), Silikon (Dan), mangan (Mn), Fosforus (P) dan sulfur (S). Antara mereka, kromium dan molibdenum adalah elemen pengaliran utama, dengan kandungan kromium 2.25% dan kandungan molibdenum dari 0.87-1.37%. Selain itu, kandungan karbon biasanya kurang daripada 0.05%, kandungan silikon tidak melebihi 0.50%, kandungan mangan tidak melebihi 0.60%, dan kandungan fosforus dan sulfur tidak melebihi 0.025%.
Sifat mekanikal
- Kekuatan hasil : biasanya 205 MPa.
- Kekuatan tegangan : biasanya 415 MPa.
- Pemanjangan : Biasanya 30%.
- Kekerasan : Selepas rawatan haba, kekerasan dapat dicapai 180 HB.
- Prestasi merayap : Ia mempunyai rintangan rayap yang sangat baik pada suhu tinggi, Terutama pada 550 ℃/50 MPa, Kehidupan pecah merayap melebihi 100,000 jam.
- Prestasi anti-pengoksidaan : Ia mempunyai prestasi anti-pengoksidaan yang baik pada 600 ℃, dan kadar pengoksidaan ialah ≤0.1 mm/tahun.
Kawasan permohonan
Paip keluli aloi p22 digunakan secara meluas dalam persekitaran tinggi dan persekitaran tekanan tinggi, seperti Stesen Power Station Superheaters, pemanas semula, tajuk, Saluran stim utama dan peralatan lain, serta petrokimia, kuasa nuklear dan medan pembinaan kapal.
Ringkasnya, Paip keluli aloi p22 telah menjadi bahan penting dalam medan perindustrian suhu tinggi dan tekanan tinggi kerana rintangan suhu tinggi yang sangat baik, rintangan kakisan dan sifat mekanikal.
Parameter proses kimpalan untuk Inconel 625 paip aloi
Parameter Proses Kimpalan Inconel 625 paip aloi terutamanya termasuk kaedah kimpalan, kelajuan kimpalan, input haba, Pemilihan bahan pengisi, dll. Berikut adalah parameter proses kimpalan utama yang diringkaskan berdasarkan maklumat yang saya cari:
- Kaedah kimpalan :
- Inconel 625 Paip aloi boleh dikimpal dengan pelbagai kaedah, termasuk kimpalan gas lengai tungsten (TIG), kimpalan gas inert logam (SAYA), kimpalan laser, Kimpalan rasuk elektron, dll.
- Kimpalan laser sesuai untuk kimpalan Inconel 625 bahan yang disebabkan oleh input haba yang rendah, Ketepatan dan Kawalan Tinggi.
- Kimpalan rasuk elektron juga sesuai untuk Inconel 625, terutamanya dalam kimpalan paip logam titik lebur yang tinggi.
- Kelajuan kimpalan :
- Kelajuan kimpalan harus diselaraskan mengikut kaedah kimpalan tertentu dan sifat bahan. Contohnya, dalam kimpalan laser, kelajuan kimpalan yang disyorkan adalah 15 m/s.
- Dalam kimpalan TIG, Adalah disyorkan untuk memilih kelajuan kimpalan yang sesuai untuk mengelakkan terlalu panas dan retak.
- Input Haba :
- Mengawal input haba adalah kunci untuk memastikan kualiti kimpalan Inconel 625. Input haba yang berlebihan boleh menyebabkan gandum kasar, retak panas dan kemerosotan prestasi.
- Disarankan untuk menggunakan input haba yang rendah, kaedah kimpalan cepat dan menjalankan rawatan haba kimpalan yang sesuai untuk melegakan tekanan selepas kimpalan.
- Mengisi pemilihan bahan :
- Bahan pengisi harus mempunyai keserasian yang baik dengan bahan asas untuk memastikan sifat mekanikal dan rintangan kakisan kimpalan.
- Bahan pengisian yang biasa digunakan termasuk AWS A5.11 ERNICR-3 dan AWS A5.11 ERNICRMO-3, dll.
- Nota lain :
- Sebelum kimpalan, permukaan harus dibersihkan untuk menghilangkan kekotoran seperti minyak, skala oksida, dll. untuk meningkatkan kualiti kimpalan.
- Semasa proses kimpalan, Pengagihan suhu seragam harus dikekalkan untuk mengelakkan terlalu panas tempatan.
- Rawatan haba yang sesuai dapat dijalankan setelah kimpalan untuk memperbaiki struktur mikro dan sifat kimpalan.
Ringkasnya, Parameter Proses Kimpalan Inconel 625 paip aloi perlu secara komprehensif mempertimbangkan pemilihan kaedah kimpalan, kelajuan kimpalan, input haba dan bahan pengisi untuk memastikan prestasi dan kebolehpercayaan sendi dikimpal.
Parameter proses kimpalan untuk paip aloi p22
Parameter proses kimpalan paip keluli aloi p22 adalah seperti berikut:
- Semasa dan voltan kimpalan : Arus kimpalan adalah 160 A dan julat voltan adalah 22 kepada 26 V.
- Suhu pemanasan : Suhu preheating ialah 170 ~ 190 ℃.
- Bahan kimpalan : R407 (E6215-C2M1) Kimpalan Kimpalan atau Kawat Kimpalan ER90S-B3 disyorkan.
- Borang alur kimpalan : Gunakan alur berbentuk v berbentuk V 60 ° dan gunakan roda pengisaran untuk membersihkan antara lapisan.
- Urutan kimpalan : Selepas mengimpal, rawatan haba dehidrogenasi dan pengesanan kecacatan dijalankan, diikuti dengan rawatan haba pelepasan tekanan.
- Kaedah kimpalan : Pilih dari GTAW (Kimpalan arka tungsten gas), SMAW (kimpalan arka logam yang dilindungi) atau cinta/mig (Kimpalan arka logam gas).
- Pasca pemprosesan : Penyejukan perlahan diperlukan selepas kimpalan untuk melegakan tekanan sisa, dan rawatan haba harus dipertimbangkan berdasarkan ketebalan bahan dan spesifikasi pasca pemprosesan.
Parameter ini memastikan kualiti paip aloi P22 Pipa dikimpal, dengan kekuatan tegangan 515 MPa, yang memenuhi keperluan standard yang berkaitan.
Perbandingan prestasi bersama kimpalan antara Inconel 625 dan aloi p22
Terdapat perbezaan yang signifikan dalam prestasi sendi yang dikimpal antara Inconel 625 dan aloi p22, terutamanya dari segi sifat mekanikal, Rintangan kakisan dan proses kimpalan.
- Sifat mekanikal :
- Inconel 625 aloi mempunyai kekuatan dan ketangguhan suhu tinggi yang sangat baik, dengan kekuatan tegangan lebih dari 760mpa, kekuatan hasil kira -kira 345mpa, dan pemanjangan lebih daripada 30%. Selain itu, Inconel 625 mempunyai sifat mekanikal yang sangat baik pada suhu bilik dan suhu tinggi, terutamanya mengekalkan kekuatan tinggi dan kemuluran yang baik dalam persekitaran suhu tinggi.
- Aloi p22 terkenal dengan keplastikan yang tinggi dan ketangguhan suhu rendah yang baik, tetapi kekuatan tegangan dan kekuatan hasilnya umumnya lebih rendah daripada Inconel 625. Aloi p22 melakukan lebih baik daripada inconel 625 dalam persekitaran suhu rendah, Tetapi kekuatan dan rintangan panasnya pada suhu tinggi adalah miskin.
- Rintangan kakisan :
- Inconel 625 Alloy mempunyai rintangan kakisan yang kuat kerana komposisi berasaskan nikelnya dan elemen tambahan seperti niobium dan molibdenum. Ia dapat menahan hakisan dalam persekitaran yang keras seperti air laut, penyelesaian dan klorida berasid. Rintangannya terhadap Pitting dan Crevice Heoron sangat luar biasa.
- Walaupun aloi p22 juga mempunyai rintangan kakisan yang baik, ia mungkin tidak sebaik inconel 625 Dalam persekitaran yang menghakis tertentu tertentu (seperti asid kuat dan larutan garam suhu tinggi).
- Prestasi kimpalan :
- Inconel 625 aloi mempunyai prestasi kimpalan yang sangat baik dan boleh dikimpal oleh pelbagai kaedah kimpalan (seperti TIG, SAYA, Smaw dan saw). Kekerasan dan ketangguhan kawasan kimpalan tinggi, dan prestasi yang baik dapat dikekalkan tanpa rawatan haba setelah kimpalan. Kekuatan tegangan sendi yang dikimpal dapat dicapai 811.36 MPa.
- Prestasi kimpalan aloi p22 agak kompleks, dan perlu memilih bahan dan proses kimpalan yang sesuai untuk mengelakkan masalah pemanasan zon yang terjejas haba (HAZ). Dalam beberapa kes, retak atau patah rapuh mungkin berlaku di sendi aloi p22 yang dikimpal.
- Kawasan permohonan :
- Inconel 625 aloi digunakan secara meluas dalam aeroangkasa, industri kimia, Kejuruteraan Marin dan bidang lain, terutamanya dalam persekitaran tinggi dan persekitaran yang menghakis.
- Aloi p22 lebih banyak digunakan untuk paip dan peralatan dalam persekitaran suhu rendah, seperti reaktor nuklear dan tangki simpanan kriogenik.
Inconel 625 aloi lebih tinggi daripada aloi p22 dalam kekuatan suhu tinggi, rintangan kakisan dan prestasi kimpalan, Walaupun aloi p22 mempunyai prestasi yang lebih tinggi dalam persekitaran suhu rendah. Pemilihan aloi yang sesuai perlu dipertimbangkan secara komprehensif mengikut senario aplikasi tertentu dan keadaan persekitaran.
Kecacatan kimpalan biasa di Inconel 625 dan paip aloi P22
Kecacatan biasa dalam proses kimpalan Inconel 625 dan paip aloi p22 terutamanya termasuk yang berikut:
- Keretakan terma : Kecacatan inconel yang paling biasa 625 Semasa kimpalan adalah keretakan haba, yang disebabkan terutamanya oleh pencampuran belerang, memimpin, fosforus atau logam rendah-titik, membentuk filem intergranular yang menyebabkan pelengkap pada suhu tinggi. Selain itu, Input haba kimpalan yang berlebihan juga boleh menyebabkan terlalu panas sendi kimpalan dan menghasilkan bijirin kasar. Eutektik titik-titik rendah di sempadan bijian mempunyai kekuatan yang rendah dan kelembutan yang tinggi, dan terdedah kepada keretakan haba.
- Tekanan kakisan (SCC) : Inconel 625 Sendi yang dikimpal terdedah kepada penekanan kakisan di persekitaran tertentu, Terutama tanpa rawatan haba pasca yang betul (PWHT). Kajian telah menunjukkan bahawa rawatan haba selepas 650 ℃ × 10 Jam dapat meningkatkan rintangan SCC sendi yang dikimpal.
- Pengasingan elemen : Pengasingan elemen mungkin berlaku semasa kimpalan Inconel 625, Terutama niobium mempunyai kecenderungan yang lebih kuat untuk memisahkan, Walaupun molibdenum mempunyai kecenderungan yang lebih lemah untuk memisahkan. Pengasingan ini boleh menyebabkan sifat -sifat yang tidak sekata dari sendi yang dikimpal.
- Patah rapuh : Inconel 625 Sendi yang dikimpal mungkin mengalami patah rapuh dalam beberapa kes, Terutama tanpa rawatan haba yang betul. Contohnya, ketangguhan keluli p92 dan inconel 625 Sendi yang dikimpal pada suhu tinggi adalah miskin.
- Kecacatan permukaan : Kecacatan permukaan seperti liang atau retak mungkin berlaku semasa proses kimpalan inconel 625. Kecacatan ini boleh menjejaskan prestasi keseluruhan sendi yang dikimpal.
- Masalah kakisan yang disebabkan oleh kandungan besi yang berlebihan : Semasa mengimpal permukaan Inconel 625, Kandungan besi yang berlebihan akan menyebabkan oksida besi (Fe₂o₃) untuk membentuk di permukaan dan bukannya kromium oksida pelindung (Cr₂o₃), dengan itu mengurangkan rintangan kakisan.
Untuk mengurangkan kejadian kecacatan ini, Langkah -langkah berikut disyorkan:
- Mengoptimumkan Parameter Proses Kimpalan : Kawalan input haba kimpalan untuk mengelakkan terlalu panas kimpalan kerana input haba yang berlebihan.
- Rawatan pasca panas yang sesuai : seperti 650 ℃ × 10 jam rawatan pasca panas, dapat meningkatkan ketahanan SCC dan ketangguhan sendi yang dikimpal.
- Pilih bahan pengisi yang betul : Menggunakan Inconel 625 Oleh kerana logam pengisi dapat mengurangkan kejadian kecacatan kimpalan dengan berkesan.
- Mengawal kandungan besi : Meminimumkan kandungan besi semasa kimpalan untuk mengelakkan pembentukan oksida besi dan meningkatkan rintangan kakisan.
Melalui langkah -langkah di atas, kecacatan biasa dalam proses kimpalan Inconel 625 dan paip aloi p22 dapat dikurangkan dengan berkesan, memastikan prestasi dan kebolehpercayaan sendi yang dikimpal.
Keperluan rawatan haba pasca kimpalan untuk kedua-dua aloi
Keperluan rawatan haba pasca kimpalan untuk kedua-dua aloi adalah seperti berikut:
- GH2132 aloi : Rawatan haba pasca kimpalan adalah penting untuk menghapuskan tekanan sisa yang dihasilkan semasa kimpalan, Tingkatkan struktur kimpalan, dan memulihkan dan memperbaiki sifat mekanikal dan rintangan kakisan kawasan kimpalan. Biasanya, Rawatan penyelesaian pepejal diperlukan, Suhu penyelesaian pepejal biasanya 980-1020 ℃, Masa pegangan adalah 1-2 jam, dan kemudian penyejukan cepat dilakukan.
- GH4021 aloi : Rawatan haba pasca kimpalan juga sangat penting. Biasanya, Rawatan penyelesaian pepejal diperlukan, dengan suhu penyelesaian pepejal 950 ° C, masa pegangan 1 jam, dan kemudian penyejukan cepat.
Ringkasan: Kedua-dua aloi GH2132 dan GH4021 memerlukan rawatan haba pasca kimpalan untuk menghapuskan tekanan sisa dan mengoptimumkan sifat-sifat kawasan kimpalan.
Bahan pengisi yang disyorkan untuk kimpalan Inconel 625 dan aloi p22
Bahan pengisi yang disyorkan untuk kimpalan Inconel 625 dan aloi p22 adalah seperti berikut:
- Inconel 625 logam pengisi : Inconel 625 Adakah logam pengisi nikel-kromium-molibdenum yang digunakan secara meluas sesuai untuk kimpalan inconel 625 sendiri dan logam yang berbeza dengan aloi berasaskan nikel lain (seperti Monel 400, Incoloy 825) dan keluli tahan karat (seperti 316, 316L). Komposisi kimianya terutamanya termasuk 65% nikel, 22% kromium, 9% Molybdenum dan 3.5% niobium. Ia mempunyai rintangan kakisan yang sangat baik dan rintangan pengoksidaan, dan dapat mengekalkan kekuatan dan kemuluran yang tinggi tanpa rawatan haba pasca kimpalan.
- Ernicrmo-3 Kimpalan Kimpalan : Ernicrmo-3 adalah logam pengisi berasaskan nikel yang biasa digunakan untuk mengimpal pelbagai aloi berasaskan nikel, termasuk Inconel 625. Kandungan kromium yang tinggi dan kandungan molibdenum yang tinggi memberikan rintangan yang baik terhadap kakisan pitting dan celah, menjadikannya sesuai untuk kimpalan logam yang berbeza.
- ER2209A Welding Wire : ER2209A adalah logam pengisi berasaskan nikel yang sesuai untuk kimpalan Inconel 625 dan keluli tahan karat dupleks seperti saf 2205. Kajian telah menunjukkan bahawa sifat ikatan yang baik dapat dicapai menggunakan ER2209A, Walaupun kasar bijirin mungkin berlaku di zon terjejas haba (HAZ).
- Inconel 622 Logam pengisi : Inconel 622 Adakah logam pengisi molibdenum yang tinggi sesuai untuk kimpalan inconel 625 dan aloi berasaskan nikel lain. Kandungan molibdenum yang tinggi meningkatkan rintangan kakisan tetapi boleh menyebabkan masalah pemisahan elemen.
- AWS A5.11 Standard Inconel 625 Batang kimpalan : AWS A5.11 Standard Inconel 625 Batang kimpalan adalah bahan pilihan untuk kimpalan Inconel 625, dengan rintangan kakisan yang baik dan sifat mekanikal, Sesuai untuk kimpalan arka tungsten gas dan kimpalan arka logam gas.
Ringkasan: Untuk kimpalan Inconel 625 dan aloi p22, Inconel 625 Logam pengisi atau dawai kimpalan Ernicrmo-3 disyorkan sebagai bahan pilihan, dan ER2209A atau Inconel 622 logam pengisi boleh dipilih mengikut keperluan khusus. Semasa proses kimpalan, Perhatian harus dibayar untuk mengawal input haba dan parameter kimpalan untuk mengelakkan tekanan dan keretakan haba.
Piawaian industri untuk mengimpal aloi ini (ASME, AWS, dll.)
Piawaian industri untuk aloi berasaskan nikel kimpalan terutamanya termasuk spesifikasi yang berkaitan dengan Persatuan Jurutera Mekanikal Amerika (ASME) dan Persatuan Kimpalan Amerika (AWS).
- Piawaian ASME :
- ASME IX adalah standard kelayakan untuk kimpalan, Brazing, dan prosedur kimpalan gabungan dalam kod dandang dan tekanan kapal dan terpakai kepada kimpalan aloi asas nikel.
- ASME B16.11 Menentukan Reka Bentuk, dimensi, dan keperluan fabrikasi untuk sendi dikimpal untuk bebibir dan sambungan paip yang diperbuat daripada aloi berasaskan nikel.
- ASME B36.10 merangkumi piawai paip keluli yang dikimpal dan lancar dan juga terpakai untuk kimpalan paip aloi nikel-asas.
- Piawaian AWS :
- AWS A5.14 Menentukan bahan kimpalan dan proses untuk aloi berasaskan nikel (seperti 625) dan sesuai untuk kimpalan dengan kekuatan suhu tinggi dan keperluan rintangan kakisan.
- AWS D1.1 adalah standard untuk kimpalan struktur keluli dan juga terpakai kepada kimpalan aloi berasaskan nikel.
- AWS A5.5 dan A5.10 Nyatakan Bahan dan Proses Kimpalan untuk Keluli Tahan Haba dan Keluli Tahan Karat. Piawaian ini juga boleh digunakan untuk kimpalan aloi berasaskan nikel.
- Piawaian lain yang berkaitan :
- ISO 13856-1 dan ISO 13856-2 Nyatakan bahan dan proses kimpalan untuk aloi berasaskan nikel, masing -masing, dan bersamaan dengan piawaian AWS dan ASME.
- DALAM 14380-1 dan dan 14380-2 juga menyediakan keperluan bahan kimpalan dan proses yang serupa.
Ringkasnya, Semasa aloi berasaskan nikel kimpalan, piawaian seperti asme ix, AWS A5.14, dan AWS D1.1 harus dirujuk untuk memastikan kualiti kimpalan dan pematuhan dengan spesifikasi industri.
Kajian kes mengenai aplikasi kimpalan untuk kedua -dua aloi
Kajian kes mengenai aplikasi kimpalan dua aloi adalah seperti berikut:
- Aloi 32 Aloi ketepatan
Permohonan aloi 32 aloi ketepatan dalam bidang kimpalan terutamanya tertumpu pada kimpalan laser, Kimpalan Brazing dan Geseran. Teknologi kimpalan laser telah digunakan secara meluas dalam kimpalan aloi 32 kerana ketepatan dan kecekapannya yang tinggi, dan dapat mencapai penembusan yang mendalam dan kesan kimpalan berkualiti tinggi. - Cuni34 aloi nikel tembaga tahan kakisan
Aloi cuni34 digunakan secara meluas dalam medan aeroangkasa untuk mengeluarkan bahagian dan penyambung konduktif pada suhu tinggi. Namun begitu, mudah untuk menghasilkan keretakan terma semasa kimpalan, dan rintangan kakisan sendi yang dikimpal mungkin terjejas. Oleh itu, Dalam aplikasi praktikal, Parameter proses yang sesuai dan bahan kimpalan perlu digunakan untuk memastikan kualiti kimpalan. - 800H nickel-iron-chromium aloi
800Aloi H Nickel-Iron-Chromium mempunyai kesesuaian kimpalan yang baik dan dapat mencapai kesan kimpalan berkualiti tinggi melalui pelbagai kaedah kimpalan seperti kimpalan arka manual (SMAW), Kimpalan TIG (Argon Arc Welding) dan kimpalan mig (Gas dilindungi kimpalan). Terutamanya dalam kimpalan keluli tahan karat, 800H menunjukkan prestasi yang sangat baik. - Aloi titanium
Teknologi kimpalan aloi titanium termasuk kaedah canggih seperti kimpalan laser dan kimpalan rasuk elektron. Teknologi ini dapat menyelesaikan masalah seperti retak dengan berkesan, liang dan ubah bentuk yang mungkin berlaku semasa kimpalan aloi titanium, memastikan kualiti dan kebolehpercayaan kimpalan. - Niobium tungsten aloi
Teknologi kimpalan laser menunjukkan kelebihan yang ketara dalam kimpalan aloi niobium tungsten. Ia dapat meningkatkan kecekapan kerja dan memastikan penampilan kimpalan yang indah, kimpalan kecil, Kedalaman kimpalan besar dan kualiti kimpalan yang tinggi. - Aloi nikel-chromium
Teknologi kimpalan laser mempunyai ciri -ciri ketepatan tinggi, Kecekapan dan fleksibiliti yang tinggi dalam kimpalan aloi nikel-kromium, dan boleh mencapai kesan kimpalan yang cekap dan tepat. - X1NICRMOCUN25-20-7 aloi berasaskan nikel
X1nicrmocun25-20-7 aloi berasaskan nikel menghadapi cabaran seperti keretakan haba dan liang semasa kimpalan. Kualiti sendi dikimpal dapat diperbaiki dengan berkesan dengan mengoptimumkan proses kimpalan, input haba, pelindung gas dan rawatan pasca kimpalan.