Nickel 200 (UNS N02200/WS 2.4060) pipe Questions and Answers
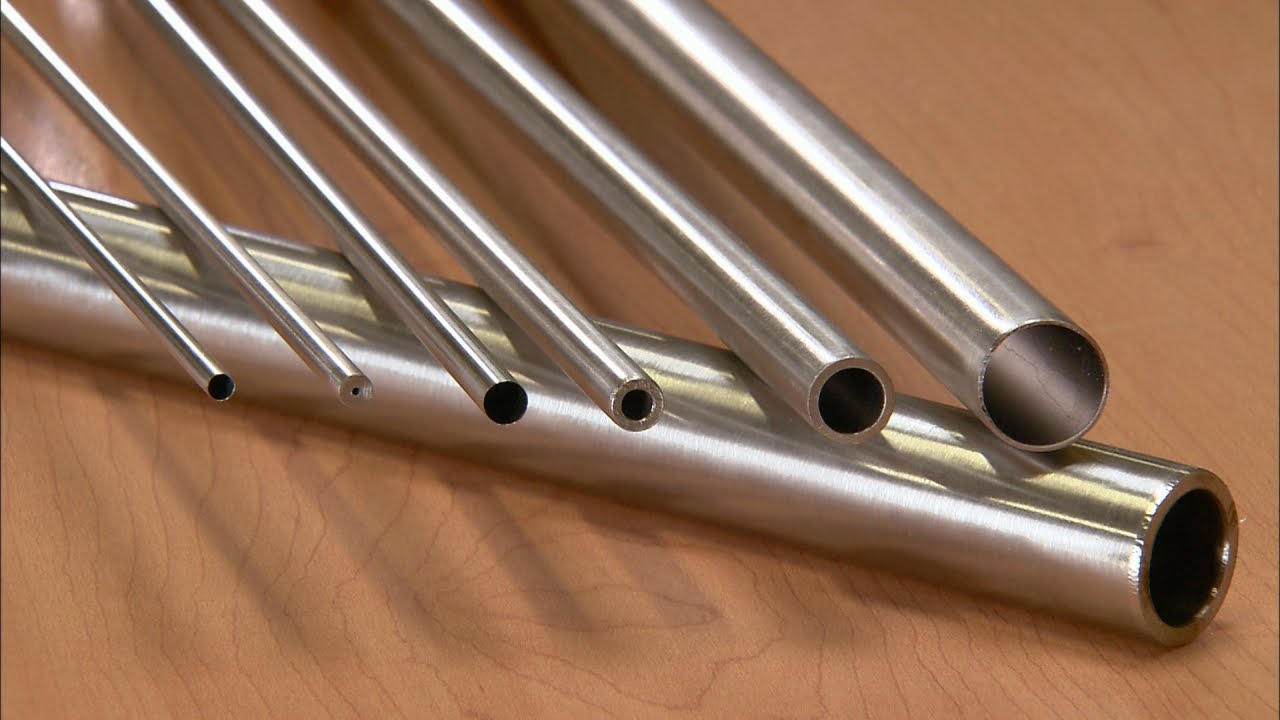
How does Nickel 200 (UNS N02200/WS 2.4060) perform in high temperatures, especially graphitization behavior at over 315°C?
The specific performance of Nickel 200 (UNS N02200/WS 2.4060) at high temperatures is as follows:
- Mechanical properties :
- Nickel 200 is usually limited to use below 600°F (315°C). At temperatures above 315°C, Nickel 200 may experience graphitization, resulting in severe damage to its performance .
- Nickel 201 is a more preferred material in applications above 600°F (315°C) .
- Corrosion resistance :
- Nickel 200 has good corrosion resistance, especially in low-carbon environments (carbon content is less than 0.02%). It does not graphitize due to carbide or graphite inclusion .
- Nickel 200 does not graphitize in the temperature range of 600°F to 1400°F (315°C to 760°C), thus providing excellent corrosion resistance at these temperatures .
- Thermal stability :
- Nickel 200 exhibits good stability at high temperatures, especially in the range of 300°C to 600°C, with extremely low oxidation rates and maintaining good performance.
- The Nickel 200 has slightly increased oxidative weight gain in the temperature range from 600°C to 800°C, but is still within the acceptable range.
- Creep behavior :
- At high temperatures, the creep rate of Nickel 200 gradually increases, resulting in greater plastic deformation, thereby shortening the service life of the material.
- At temperatures above 600°C, the strength of Nickel 200 has significantly decreased, and both yield strength and tensile strength have been reduced.
In summary, Nickel 200 performs well at high temperatures, especially below 315°C.
What are the comparative studies on corrosion resistance between Nickel 200 and other nickel alloys (such as Nickel 201 and Inconel 600)?
Comparative studies on corrosion resistance of Nickel 200 and other nickel alloys such as Nickel 201 and Inconel 600 are as follows:
- Alkaline resistance :
- Nickel 200 and high nickel alloys such as Inconel 600 and 625 exhibit good corrosion resistance when dealing with alkaline media. Nickel 200 is particularly resistant to caustic soda and other alkaline compounds (except ammonia water) and will not be attacked in 1% concentration of anhydrous ammonia, but in the presence of dissolved oxygen, strong concentrations of anhydrous ammonia can lead to rapid attack. .
- Oxidation-resistant acid salts :
- Inconel 600 has better corrosion resistance in oxidized acid solutions than Nickel 200 and MONEL 400. However, Inconel 600 is barely affected by silver-containing chloride solutions, which makes it very suitable for strongly hot solutions containing silver salts .
- Resistant to chloride and hydrochloric acid :
- Nickel 201 and Inconel 600 are the best choices in chloride and hydrochloric acid environments. Nickel 201 has better corrosion resistance at high temperatures, while Inconel 600 performs better at low temperatures .
- Hydrogen fluoride resistance :
- In anaerobic and aerobic aqueous hydrogen fluoride solution, Nickel 200 is not as corrosion-resistant as the 400 series alloy. In aqueous hydrogen fluoride solutions in the presence of air or oxygen, Nickel 200 has worse corrosion resistance and only exhibits good corrosion resistance under completely anaerobic conditions (below 170 to 180°C). Inconel 600, by contrast, has good corrosion resistance to diluted water hydrogen fluoride solutions, but may be significantly corroded in high-temperature water hydrogen fluoride solutions. .
- Resistant to chlorine and hydrochloric acid :
- Nickel 201 and Inconel 600 are the best choices in chlorine and hydrochloric acid environments. Nickel 201 has better corrosion resistance at high temperatures, while Inconel 600 performs better at low temperatures .
- Sulfide resistance :
- In sulfur-containing environments, both Nickel 201 and Inconel 600 are susceptible to sulfur-based inter-matrix crack corrosion. In applications where high temperature strength is needed, the Inconel 600 is the best alternative to the Nickel 200/201.
Nickel 200 exhibits good corrosion resistance in alkaline and non-oxidized acid environments, but is not as good as other nickel alloys in oxidized acid, chloride and high-temperature water hydrogen fluoride solutions.
What are the specific requirements of the ASTM B725 standard for Nickel 200 welded pipes, including detailed regulations on size, wall thickness and maximum length?
According to the ASTM B725 standard, the specific requirements for Nickel 200 welded pipe are as follows:
- size :
- Outer diameter range: 3-325mm.
- Wall thickness range: 0.5-20mm.
- Maximum length :
- The maximum length is 25 meters.
These regulations ensure the suitability and performance of Nickel 200 welded pipes in general corrosive services and mechanical applications. In addition, the standard covers other testing methods, the use of Material Safety Data Sheets (MSDS), the establishment of safety and health practices, and the applicability of regulatory restrictions.
What are the application cases of the Nickel 200 in the fields of food processing and electronic components, and how are its performance advantages reflected?
In the fields of food processing and electronic components, the application cases and performance advantages of Nickel 200 (N02200) are as follows:
Application cases and performance advantages in the field of food processing
- Food processing equipment :
- Application case : Nickel 200 is widely used in food processing equipment, such as mixers, mixers, conveyor belts, etc. These equipment need to operate in environments of high temperature, high corrosion and high sanitary standards.
- Performance advantages : Nickel 200 has excellent corrosion resistance, can resist corrosion of acid, alkali and salt solutions, ensuring hygiene and safety during food processing . In addition, its high thermal conductivity and low gas content allow it to maintain good thermal conductivity under high temperature environments, which helps the equipment to operate efficiently .
- Synthetic fiber production :
- Application Case : Nickel 200 is used in the production of synthetic fibers, especially when handling and storing corrosive chemicals.
- Performance Advantages : Nickel 200’s high purity and non-toxicity make it excellent in synthetic fiber production, while its high temperature and corrosion resistance ensures stability and safety in the production process.
Application cases and performance advantages in the field of electronic components
- Electronic component manufacturing :
- Application Case : Nickel 200 is used to manufacture electronic components such as batteries, capacitors and other products with high electrical conductivity and corrosion resistance requirements.
- Performance Advantages : The Nickel 200 has high conductivity and magnetism, making it an ideal material for manufacturing electronic components. Its high conductivity and stable expansion coefficient ensure high performance and reliability of electronic components.
- Heating element wire :
- Application case : Nickel 200 is used to manufacture heating element wires and is widely used in various heating equipment.
- Performance Advantages : The high temperature resistance of Nickel 200 makes it excellent in heating element wires and maintains stable performance in high temperature environments.
- Aerospace components :
- Application Case : Nickel 200 is used for component manufacturing in the aerospace field, such as engine parts and turbine engine parts.
- Performance Advantages : The Nickel 200’s high strength, toughness and high temperature resistance make it outstanding in the aerospace field, and can maintain structural integrity and stability in extreme environments.
Summarize
Nickel 200 is mainly used in the food processing and electronic components fields due to its excellent corrosion resistance, high conductivity and magnetism, and stable performance in high temperature environments.
What are the latest research or improvements for Nickel 200’s surface treatment technologies (such as pickling, bright annealing or polishing surfaces)?
According to available data, the following latest research or improvements have been made for Nickel 200’s surface treatment technologies, such as pickling, bright annealing or polishing surfaces:
- Pickling treatment :
- After welding, pickling treatment is recommended to remove oxide layers that may affect performance. Pickling is usually the last operation during the welding process to ensure that the surface after welding reaches an ideal surface state.
- Pickling treatment not only helps remove the oxide layer, but also improves the corrosion resistance of the material. In some cases, pickling may be used in combination with heat treatment to further optimize the performance of the material.
- Bright annealing :
- Bright annealing is a common surface treatment technique that is mainly used to improve the surface finish of materials and reduce surface defects. Bright annealing is usually performed at lower temperatures to avoid excessive softening of the material .
- The surface of the material after bright annealing is smoother, helping to improve the aesthetics of the material and performance in certain applications, such as the use in electronic components and chemical equipment. .
- Polished surface :
- Polishing is an advanced surface treatment technology that can significantly improve the surface finish and reflectivity of a material. The polished material surface is smoother, reducing surface defects and roughness .
- Polishing technology is very useful in applications requiring high precision and high performance, such as the use of aerospace components and precision instruments .
- Combination of heat treatment and surface treatment :
- The combination of heat treatment and surface treatment can further optimize the performance of the material. For example, solid solution treatment can improve the corrosion resistance and ductility of the material, while appropriate annealing treatment can improve the mechanical properties of the material.
- In some cases, the heat-treated material can be further processed by pickling or polishing to achieve optimal surface condition and performance .
To sum up, Nickel 200’s surface treatment technology includes methods such as pickling, bright annealing and polishing surfaces. These technologies have their unique advantages and room for improvement in different application scenarios.