História da fabricação de tubos de aço e pesquisa de processos
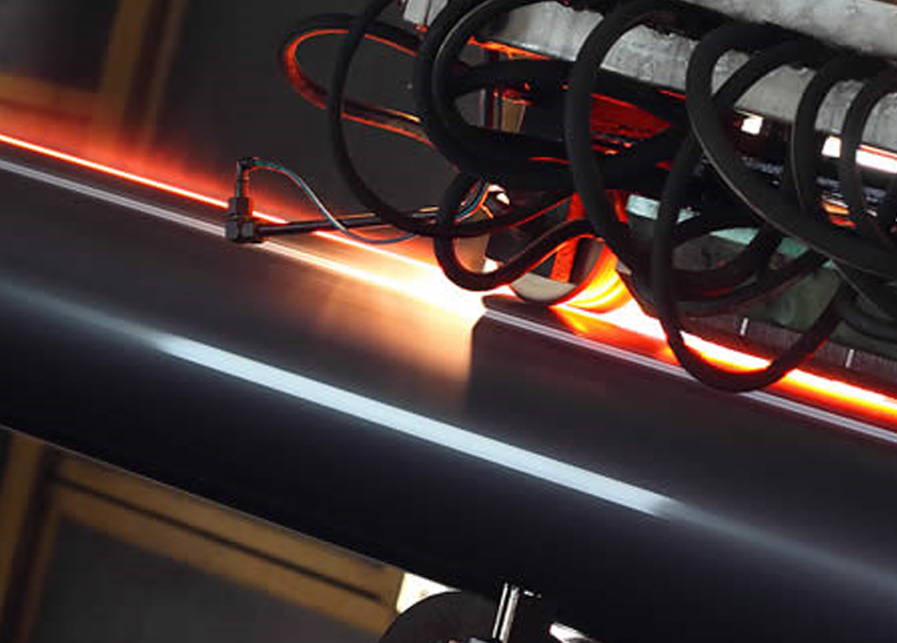
Tubo de aço carbono
O tubo de aço carbono começa chegando ao moinho de tubos na forma de um tarugo (Basicamente, uma grande barra de aço sólido) ou uma bobina (Imagine um rolo de papel higiênico feito de aço). Dependendo do método de fabricação usado pelo moinho, Esses tarugos ou bobinas serão processados para produzir o produto final acabado. Examinaremos os vários métodos de fabricação usados para fazer tubos de aço carbono, Mas primeiro vamos ver como o aço carbono chegou aqui em primeiro lugar.
Processo de fabricação de aço cru
Os seres humanos estão derretendo minério de ferro através de um processo chamado fundição por milhares de anos. O ferro fundido ou semi-molteado seria martelado (forjado) ou derramado em suas formas desejadas e deixado esfriar. As pessoas descobriram rapidamente que as propriedades do produto acabado (força, ductilidade, longevidade) poderia ser controlado de várias maneiras; manipular o tempo e condições de resfriamento ou adicionar/remover certos mídias, por exemplo. O aço carbono foi um derivado popular de ferro cru fabricado pela introdução de carbono elementar no processo de fundição na forma de carvão vegetal. Tão útil quanto o aço era, Era hora e trabalho intensivos para produzir, tornando -o geralmente um material ruim para o consumo em massa. Em meados do século 19, O processo de Bessemer foi patenteado onde por ferro fundido derretido (barato feito e cheio de alto carbono, silício, e impurezas de manganês) está sujeito a explosões de oxigênio que oxidam as impurezas, tornando -as simples de remover do aço fundido. Esse método de remover o excesso de elementos era muito mais fácil e barato do que adicionar elementos de liga ao ferro, e é diretamente responsável pela revolução industrial e pelo início da produção em massa de aço carbono. Hoje a tecnologia mudou, Mas os mesmos princípios básicos do processo Bessemer ainda são a espinha dorsal para a moderna produção de aço bruto.
As fábricas de aço modernas produzem aço por sucata de fusão ou adicionando coca (carvão pulverizado com os hidrocarbonetos removidos) para o minério de ferro fundido. O metal fundido está sujeito a um derivado moderno do processo Bessemer para remover elementos indesejáveis, Outros elementos desejáveis são então adicionados (dependendo das propriedades finais desejadas do aço), E então o aço é fundido e resfriado para o que sempre molda os clientes desejam. Como mencionado anteriormente, No caso do tubo de aço carbono, esses elencos geralmente estão na forma de bobinas ou tarugos.
Hora de fazer o cachimbo
Bailetos e bobinas são entregues no moinho de tubos pronto para ser transformado em tubo de aço carbono. Dependendo das capacidades do moinho de tubos e do uso final do produto final, Os elencos serão formados em tubo por meio de quatro métodos distintos de fabricação diferentes; sem costura, solda de resistência elétrica (ERW), solda de arco submersa dupla (DSAW), ou solda espiral.
Tubo de aço carbono sem costura
Tubo de aço carbono sem costura tem, Como o próprio nome implica, Sem costura longitudinal de solda. Isso é, em essência, um sólido pedaço homogêneo de aço. Um tarugo sólido é simplesmente aquecido e depois esticado sobre uma série de mandrels até que o tubo atinja o diâmetro desejado e a espessura da parede. Tipicamente o tubo de aço carbono em carbono quatorze polegadas e maior em diâmetro são rolados de conchas que expandem o diâmetro e reduzem a parede até que as dimensões desejadas sejam alcançadas. Os tamanhos menores que quatorze polegadas de diâmetro são tipicamente reduzidos por estiramento, pelo qual o diâmetro é gradualmente reduzido e a parede aumentou relativamente através de uma série de rolos. Há também um processo de formação a frio para produção de tubos sem costura, Mas esses processos de fabricação geralmente são reservados para diferentes ligas. Sendo que não há costura, O tubo de aço carbono sem costura é normalmente usado em aplicações de alta pressão. Especificações perfeitas comuns incluem; API5LB, A106, A333
Solda de resistência elétrica (ERW)
Os primeiros produtores de tubos de aço carbono empregavam um método de fabricação chamado Butt-Welding. O processo de lança-bunda era bastante elementar, pois apenas rolou um pedaço de placa de aço aquecida em forma tubular e criou uma solda longitudinal através da compressão e calor direto. Em 1922 A Fetz Moon Tube Company instituiu a primeira linha de solda contínua, onde por bobinas de aço enroladas (de novo, Imagine um rolo de papel higiênico feito de aço) pode ser desenrolado, nivelado, e contínuo, alimente uma linha de rolos que dobrariam lentamente o aço em forma eventualmente a um ponto em que as extremidades podem ser soldadas de bunda. Quando o moinho chegou ao fim de uma bobina, Eles poderiam simplesmente soldá -lo no início da próxima bobina com pouca interrupção na produção. Como a indústria pedia tolerâncias mais rígidas e melhores soldas, O processo contínuo da solda de bunda deu lugar à soldagem de resistência elétrica (ERW). O ERW é bastante semelhante ao processo de solda contínuo, pois as bobinas de aço são niveladas e distribuídas em uma linha de formação de rolos, Mas é aí que as semelhanças terminam. Durante o processo ERW, as bobinas desenroladas (Ovelha) não são aquecidos e a solda longitudinal é criada por meio de uma corrente elétrica. A solda é então inspecionada eletronicamente por defeitos, normalizado para manter a consistência com o restante do aço, e resfriado. Neste ponto, o tubo às vezes é redimensionado e depois cortado, revestido, e ou testado para atender às especificações desejadas. O tubo ERW normalmente mantém tolerâncias muito mais rígidas e mantém a consistência da superfície e da parede muito mais do que o tubo de aço carbono perfeito. As especificações comuns de ERW incluem; API5LB, A53, e A500
Solda de arco submersa dupla (DSAW)
A solda de arco submerso duplo (DSAW) O processo é semelhante ao do processo ERW, pois as bobinas de aço carbono são desenroladas em uma fita contínua. Como o método DSAW de fabricação é normalmente usado para tubos de maior diâmetro, O método de roll formando o skelp é semelhante, mas não exatamente como o de erw. O tubo dsaw é tipicamente pirâmide enrolado (Três oda angulares rolam na forma de uma pirâmide o tubo) ou rolou usando o processo U-O-E (Skelp está primeiro sujeito a um “Você” Pressionada em forma, seguido por a “Ó” Pressionada em forma). A diferença mais proeminente entre o tubo de aço de ERW e Dsaw Carbon é a solda longitudinal. A solda de arco Dsaw está submersa em uma mídia de fluxo para impedir que a solda seja exposta a contaminantes ambiente. Também, Tanto o OD quanto o ID do tubo são soldados, normalmente em momentos separados, criando uma situação em que uma solda consome a outra criando uma solda de maior qualidade. O tubo de aço carbono Dsaw é facilmente distinguível devido ao seu ID e costura de solda de OD de destaque e OD. As especificações comuns do DSAW incluem; API5L, A252, e A139.
Solda em espiral
O método de fabricação mais facilmente distinguível para o tubo de aço carbono é a solda em espiral. Nesse processo, a solda é criada exatamente da mesma maneira que a de Dsaw, Somente a costura de solda assume uma aparência helicoidal ou em espiral devido à maneira como o skelp é enrolado para formar. Assim como no caso do processo ERW e DSAW, Uma fita contínua de Skelp é nivelada e enviada através de uma série de rolos para formar. No caso do processo de solda em espiral, uma dobra simples de três rolos é típica e, portanto, é mais rápida, mais eficiente, e processo de fabricação menos caro. O processo de solda em espiral também permite que o moinho role uma gama muito mais ampla de tamanhos do que Dsaw ou Erw Mills. Também, Devido à sua simetria axial, O tubo de aço carbono de solda em espiral tem uma capacidade inerente de manter a direita. Especificações comuns de solda em espiral incluem; API5LB e A252. Entre em contato conosco para o seu próximo projeto de tubo de aço carbono.
Tripulação, C.P. e Fruehan, R.J. Tecnologias emergentes para fabricação de aço. Vamos (53) 10. 2001
Ashton, T.S. Ferro e aço na revolução industrial. Nova Iorque: Augustus 1000. Kelley, 1968.
Stubbles, John. “O processo básico de fabricação de aço de oxigênio.” Centro de Aprendizagem American Iron and Steel Institute Steelworks.
Esporel, Joseph. Uma breve história de produção de ferro e aço.
Associação Nacional de Distribuidores de Pipes de Aço. Manual de produtos tubulares Um tubo de aço e um livro de tubos. Terceira edição 1996
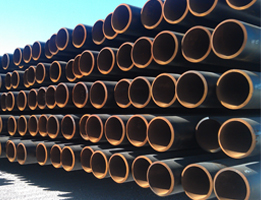
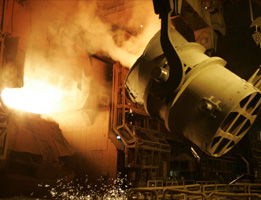
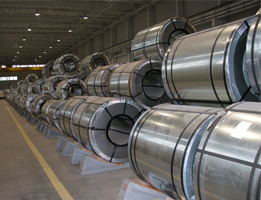
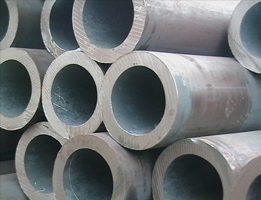

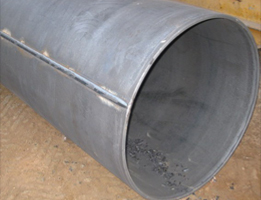
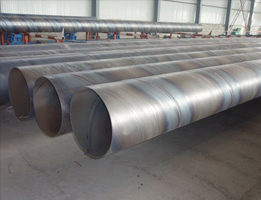
2 comments
Shanteta
October 6, 2022 at 7:30 am
What are the three major methods of steel pipe manufacturing?
admin
March 28, 2025 at 1:58 pm
There are three main processes used in the manufacturing of metal tubing and pipe.
Electric Welded Tubing. Also referred to as Electric Resistance Welded or ERW tubing, is produced when a strip of steel is passed through rollers to form the desired shape. …
D.O.M. or Drawn over Mandrel tubing. …
Seamless Tubing Process.