SAWH Steel Pipe
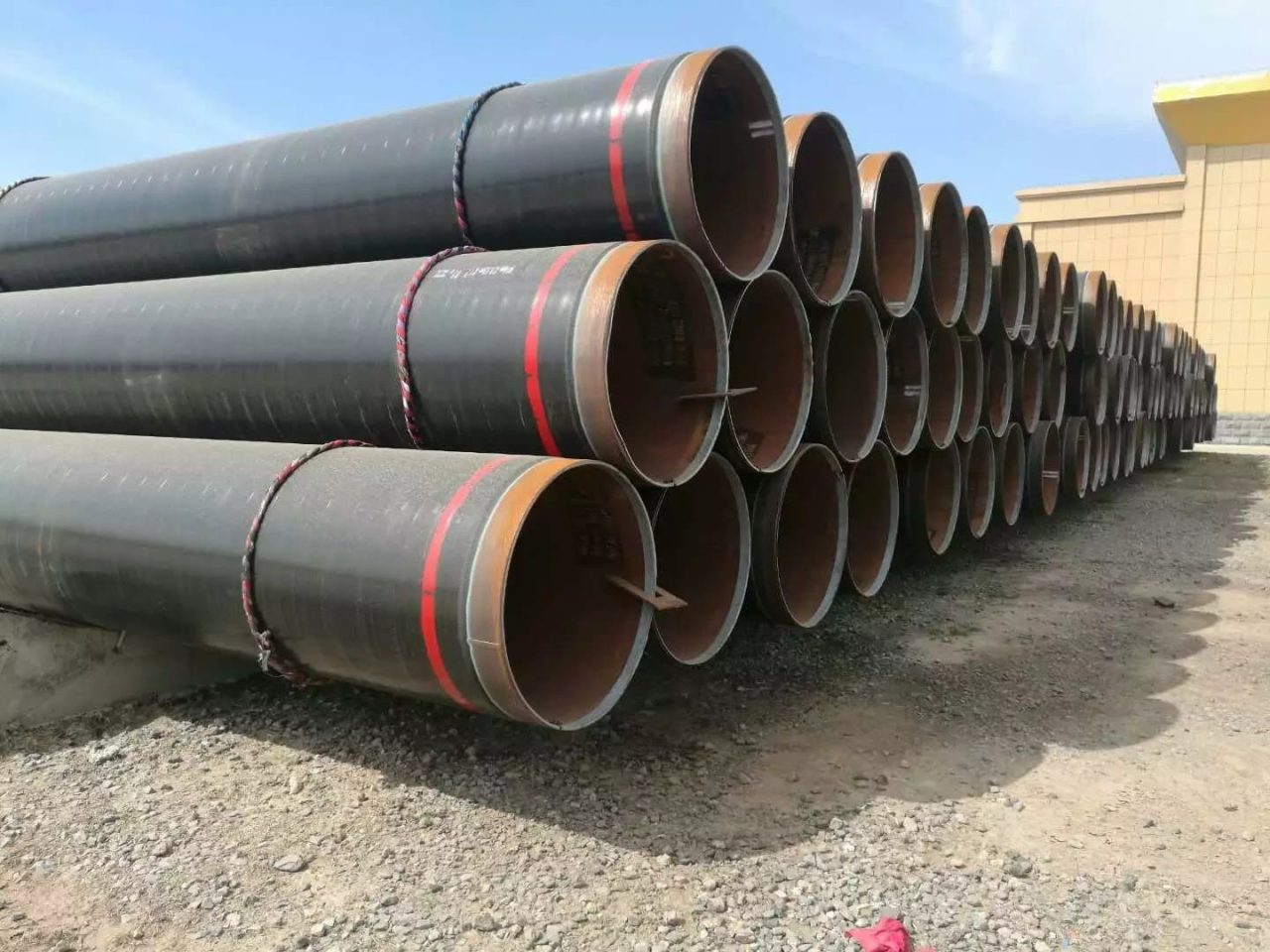
SAWH (Spiral Submerged Arc Welded) Steel Pipe
SAWH (Spiral Submerged Arc Welded) steel pipes are widely used in various industries for their strength, durability, and cost-effectiveness. These pipes are manufactured using a spiral welding process, which provides enhanced structural integrity and allows for the production of large diameter pipes.
Key Features
- Manufacturing Process: Spiral Submerged Arc Welding (SAW)
- Grades:
- API 5L (various grades such as X42, X52, X60, X70)
- ASTM A252
- ISO 3183
- Sizes:
- Outside Diameter: 8” to 120” (219.1 mm to 3048 mm)
- Wall Thickness: 0.157” to 1.575” (4 mm to 40 mm)
- Lengths: Up to 18 meters or custom lengths as per requirements
Chemical Composition
The chemical composition varies based on the specific grade and standard. Below is a general example for API 5L Grade X52:
Element | Maximum Percentage (%) |
---|---|
Carbon (C) | 0.22 |
Manganese (Mn) | 1.40 |
Phosphorus (P) | 0.025 |
Sulfur (S) | 0.015 |
Silicon (Si) | 0.45 |
Mechanical Properties
Mechanical properties also depend on the specific grade and standard. Below is an example for API 5L Grade X52:
Property | Value |
---|---|
Yield Strength (min) | 52,000 psi (360 MPa) |
Tensile Strength (min) | 66,000 psi (455 MPa) |
Elongation (min) | 21% |
SAWH Manufacturing Process
- Steel Coil Preparation: High-quality steel coils are selected and prepared.
- Edge Preparation: Edges of the steel coils are trimmed and beveled to ensure proper weld seam.
- Forming: Steel coils are fed into a spiral forming machine where they are formed into a spiral shape.
- Tack Welding: The edges of the spirally formed pipe are tack-welded to hold the shape.
- Submerged Arc Welding: The spiral seam is welded using submerged arc welding both internally and externally, ensuring deep penetration and strong weld integrity.
- Inspection: Pipes undergo various non-destructive tests such as ultrasonic testing, radiographic testing, and visual inspection to ensure weld quality and pipe integrity.
- Hydrostatic Testing: Each pipe is subjected to hydrostatic pressure testing to verify its pressure resistance.
- Finishing: Final processes include end beveling, coating, and marking as per customer specifications.
Applications
- Oil and Gas Transportation: Used in pipelines for transporting oil, gas, and other fluids.
- Water Transmission: Suitable for water supply and drainage systems.
- Structural Applications: Used in construction of bridges, buildings, and other infrastructure projects.
- Piling Foundations: Employed as piling pipes in foundation construction.
- Mechanical Applications: Utilized in various industrial and mechanical applications.
Advantages
- High Strength: Capable of withstanding high pressure and stress.
- Cost-Effective: Efficient manufacturing process reduces production costs.
- Large Diameter Production: Spiral welding allows for the production of large diameter pipes.
- Strong Weld Integrity: Spiral weld provides a strong and reliable seam.
- Versatility: Suitable for a wide range of applications and environments.
- Quality Assurance: Rigorous testing ensures high-quality output and compliance with standards.
Conclusion
SAWH steel pipes are an excellent choice for various industrial applications due to their strength, durability, and cost-effectiveness. Whether used in oil and gas transportation, water transmission, structural projects, or mechanical applications, these pipes provide reliable performance and long-term durability. The spiral welding process ensures strong weld integrity and allows for the production of large diameter pipes, making SAWH pipes a versatile and efficient solution for many engineering and construction needs.