Inconel'in Kaynak Teknolojisi Analizi 625 ve p22 alaşımlı çelik borular
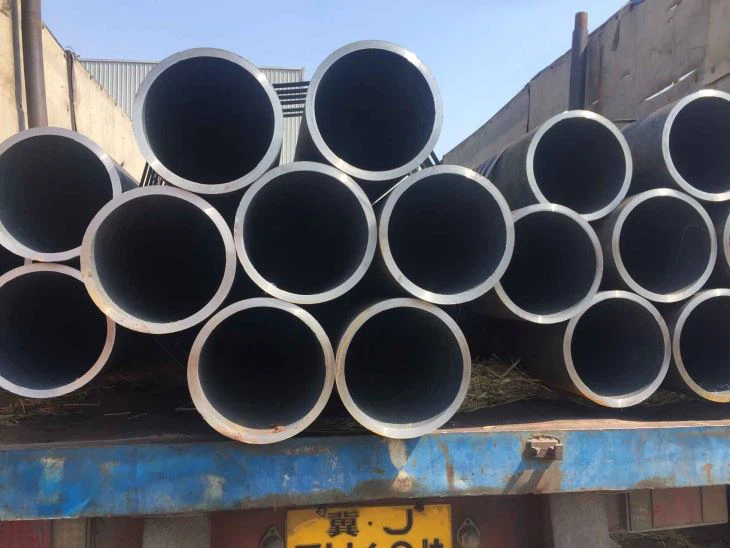
Inconel'in Kaynak Teknolojisi Analizi 625 ve p22 alaşımlı çelik borular
1. giriiş
Farklı malzemelerin kaynağı, Nikel bazlı süper alaşımlar gibi (örneğin, İnkonel 625) ve alçak alaşım çelikler (örneğin, P22), farklı metalurjik ve mekanik özellikleri nedeniyle önemli zorluklar sunar. Bu analiz, kaynak tekniklerini kapsamlı bir şekilde inceler, İşlem parametreleri, ortak kusurlar, ve bu materyaller için weld sonrası tedaviler, endüstri standartları ve deneysel vaka çalışmaları tarafından desteklenmektedir.
İnkonel 625 Alaşım Boru Kimyasal Bileşimi ve Mekanik Özellikler
Inconel'in kimyasal bileşimi ve mekanik özellikleri 625 alaşım boru aşağıdaki gibidir:
2. Malzeme özellikleri
2.1 İnkonel 625 Alaşım
Kimyasal Bileşim ():
Öğe | İçinde | CR | Ay | Fe | NB+TA | C | Mn | Ve |
---|---|---|---|---|---|---|---|---|
% | ≥58 | 20–23 | 8–10 | ≤5 | 3.15–4.15 | ≤0,10 | ≤0.50 | ≤0.50 |
Mekanik Özellikler ():
- Çekme Dayanımı: 827 MPa (dk.)
- Akma Dayanımı (0.2% telafi etmek): 414 MPa (dk.)
- Uzama: 35% (dk.)
- Sertlik: ≤287 hb (tavlanmış durum)
- Erime Noktası: 1,290–1,350 ° C
İnkonel 625 Yüksek CR ve MO içeriği nedeniyle klorür açısından zengin ortamlarda 980 ° C'ye kadar olağanüstü oksidasyon direnci ve korozyon direnci sergiler .
2.2 P22 Alaşımlı Çelik
Kimyasal Bileşim ():
Öğe | C | CR | Ay | Mn | Ve | Fe |
---|---|---|---|---|---|---|
% | 0.05–0,15 | 1.90–2.60 | 0.87–1.13 | 0.30–0,61 | ≤0.50 | bal. |
Mekanik Özellikler ():
- Çekme Dayanımı: ≥415 MPa
- Akma Dayanımı: ≥205 MPa
- Uzama: ≥% 30
- Sertlik: 180–240 hb (Isı işlemden sonra)
P22, yüksek sıcaklık hizmeti için optimize edilmiş bir CR-MO çeliğidir (550-600 ° C'ye kadar), İyi kaynaklanabilirlik ve sürünme direnci ile
3. Farklı eklemler için kaynak zorlukları
3.1 Metalurjik uyumsuzluklar
- Termal Genleşme Katsayısı (CTE) Uyuşmazlık:
İnkonel 625 (14.7 µm/m ° C) vs. P22 (12.3 µm/m ° C) Soğutma sırasında artık gerilmeler üretir . - Karbon göçü:
Karbonun P22'den Inconel'e difüzyonu 625 kırılgan karbürler oluşturur (örneğin, CR23C6) füzyon sınırında, Sertliği azaltmak . - Seyreltme etkileri:
Kaynak havuzunda yüksek FE içeriği (P22'den) Inconel'in korozyon direncini bozar 625 .
3.2 Termal gradyan yönetimi
- Isı giriş kontrolü:
Inconel'de aşırı ısı girişi 625 tahıl kabılcına neden olur, P22 için yetersiz ön ısıtma hidrojen çatlama riskini arttırır .
4. Kaynak işlemleri ve parametreler
4.1 Önerilen Kaynak Yöntemleri
Malzeme çifti | Tercih edilen yöntemler | Temel Hususlar |
---|---|---|
Inconel 625 - 625 | TIG (GTAW), Lazer kaynağı | Düşük ısı girişi, otojen kaynak |
P22 - P22 | SMAW, GTAW | Önceden ısıtmak (170–190 ° C), Anlatılan stres rahatlaması |
Inconel 625 - P22 | Ni tabanlı dolgu ile tig | Arabellek katmanları, kontrollü seyreltme |
4.2 Farklı kaynak için proses parametreleri
Örnek Olay İncelemesi: İnkonel 625 Ernicrmo-3 dolgu kullanarak P22'ye ():
- Ön ısıtma: 150–200 ° C (Sadece p22 tarafı) Termal stresi en aza indirmek için.
- Interpass Sıcaklığı: ≤150 ° C (Inconel'de aşırı tahıl büyümesini önler 625).
- Isı Girişi: 0.8–1.2 kJ/mm (TIG), 1.5–2.0 kj/mm (SMAW).
- Koruyucu gazı: Argon + 2Oksidasyonu azaltmak için TIG kaynağı için –5 h2.
Elektron ışını kaynağı (Emn):
Cucrzr/Incon için kullanılır 625 Vakum uygulamalarında eklemler, Dar bir HAZ ve minimal bozulma elde etmek .
5. Dolgu Malzemesi Seçimi
5.1 İnkonel 625 Kaynak
- Eşleşen Dolgu: Ernichrmo-3 (AWS A5.14) korozyon direncini ve mekanik pariteyi sağlar .
- Farklı kaynaklar: Inconel Dolgu Metal 625 (Ernichrmo-10) Paslanmaz çeliklere veya p22'ye katılmak için, Karbon göçünü azaltma .
5.2 P22 Kaynak
- Eşleşen Dolgu: E9018-B3 (SMAW) veya ER90S-B3 (GTAW) CR-MO çelik uyumluluğu için .
6. Yaygın kaynak kusurları ve hafifletme
6.1 İnkonel 625
- Sıcak Çatlama: S/P safsızlıklarının neden olduğu; Yüksek saflıkta dolgu maddeleri ve düşük ısı girişi kullanılarak hafifletilmiş .
- Gözeneklilik: Koruyucu gazda nem kontaminasyonundan kaçının (çiy noktası ≤ -50 ° C) .
6.2 P22
- Hidrojen kaynaklı çatlak: Ön ısıtma yoluyla kontrol edilir, düşük hidrojen elektrotlar, ve 300-350 ° C'de anılan sonrası dehidrojenasyon .
6.3 Farklı eklemler
- Kırılgan metaller arası aşamalar: NI tabanlı arabellekler kullanın (örneğin, Ernichrmo-3) Fe seyreltisini emmek için .
7. Kaynak Sonrası Isıl İşlem (PWHT)
Malzeme | PWHT parametreleri | Amaç |
---|---|---|
İnkonel 625 | Çözüm tavlama: 980–1,020 ° C, Hızlı Soğutma | Korozyon direncini geri yükleyin |
P22 | Stres giderme: 650–700 ° C, 1–2 saat | Artık gerilmeleri azaltın |
Inconel 625 - P22 | 750 ° C'nin üzerindeki P22'yi tavlamadan kaçının (Karbür kaba olmayı önler) | Denge stresi ve mikro yapı |
Çalışma sonucu: 650 ° C'de PWHT 10 Saatler F22/Inconel'de SSCC direncini geliştirdi 625 Eklemler 40% .
8. Endüstri standartları ve uyumluluk
- ASME BPVC Eylem IX: Kazan/Basınçlı Kaplama Uygulamaları için Kaynak Prosedürlerini ve Personelini Nitelikler .
- AWS D10.18: Aşındırıcı ortamlarda ni-cr-mo alaşımlarının kaynakları.
- ASTM B444: Inconel'i belirtir 625 Boru üretimi ve testleri .
9. Vaka çalışmaları
9.1 Nükleer reaktör boruları (Inconel 625 - P22)
- Başvuru: Basınçlı su reaktörlerinde buhar jeneratör borusu.
- Kaynak Yöntemi: Ernicrmo-3 dolgu ile dar boşluk tig.
- Sonuç: Sonra çatlak veya korozyon yok 10,000 hizmet saatleri .
9.2 Petrokimyasal boru hattı (P22 - P22)
- Başvuru: Yüksek sıcaklık gaz iletimi.
- Kaynak Yöntemi: E9018-B3 ile Smaw, 680 ° C'de kılan stres giderme.
- Sonuç: API'ya uyum 1104 standartlar; Hidrojen çatlakları tespit edilmedi .
10. Gelecek Eğilimler
- Lazer hibrit kaynak: Inconel'de daha yüksek hız ve hassasiyet için lazer ve gmaw'ı birleştirir 625 .
- Katkı maddesi üretimi: Inconel'i tamir etmek için Wire-Arc AM 625 Minimal HAZ ile bileşenler .
Mekanik özellikler
İnkonel 625 Alaşım borusu mükemmel mekanik özelliklere sahiptir, aşağıdaki gibi:
- Çekme mukavemeti : ≥120 MPa (tavlanmış devlet).
- Verim gücü : ≥827 MPa (tavlanmış devlet).
- Uzama : ≥% 60 (tavlanmış devlet).
- Sertlik : HB ≤ 287 (tavlanmış devlet).
- Yüksek sıcaklık performansı : Yüksek sıcaklık ortamlarında yüksek mukavemet ve oksidasyon direncini korur, 2000 ° F'ye kadar maksimum çalışma sıcaklığı ile (yaklaşık 1093 ° C).
- Korozyon direnci : Oksitleyici asitte çukurlaşma ve çatlak korozyonuna oldukça dirençli, Asit ve klorür ortamlarının azaltılması.
Özellikler
- Korozyon direnci : İnkonel 625 Çeşitli aşındırıcı ortamlara karşı mükemmel bir dirence sahiptir, nitrik asit dahil, sülfürik asit, fosforik asit ve hidroklorik asit.
- Yüksek sıcaklık dengesi : Yüksek sıcaklıklarda iyi mekanik özellikleri ve oksidasyon direncini koruyabilir.
- İşleme performansı : İyi kaynaklanabilirlik ve işlenebilirliğe sahiptir, ve çeşitli karmaşık şekillerin parçalarını üretim için uygundur.
Özetle, İnkonel 625 Alaşım boruları kimyasalda yaygın olarak kullanılır, Deniz, Mükemmel korozyon direncleri nedeniyle nükleer enerji ve diğer alanlar, Yüksek sıcaklık stabilitesi ve mekanik özellikler.
P22 Alaşım Boru Kimyasal Bileşimi ve Mekanik Özellikler
P22 alaşımlı çelik borunun kimyasal bileşimi ve mekanik özellikleri aşağıdaki gibidir:
Kimyasal bileşim
P22 alaşımlı çelik borunun ana kimyasal bileşenleri krom içerir (CR), molibden (Ay), karbon (C), silikon (Ve), manganez (Mn), fosfor (P) ve kükürt (S). Aralarında, Krom ve molibden, ana alaşım elemanlarıdır, krom içeriği ile 2.25% ve molibden içeriği 0.87-1.37%. Ek olarak, Karbon içeriği genellikle daha azdır 0.05%, Silikon içeriği aşmıyor 0.50%, Manganez içeriği aşmıyor 0.60%, ve fosfor ve kükürt içeriği aşmıyor 0.025%.
Mekanik özellikler
- Verim gücü : tipik olarak 205 MPa.
- Çekme mukavemeti : tipik olarak 415 MPa.
- Uzama : Genellikle 30%.
- Sertlik : Isı işlemden sonra, Sertlik ulaşabilir 180 HB.
- Sürünme performansı : Yüksek sıcaklıklarda mükemmel sürünme direncine sahiptir, Özellikle 550 ℃/50 MPa'da, Sürünme rüptürü hayatı aşıyor 100,000 saat.
- Anti-oksidasyon performansı : 600'de iyi anti-oksidasyon performansına sahiptir., ve oksidasyon oranı ≤0,1 mm/yıl.
Uygulama alanları
P22 Alaşımlı Çelik Borular, yüksek sıcaklık ve yüksek basınçlı ortamlarda yaygın olarak kullanılmaktadır., Power Station Kazan Superheaters gibi, yeniden ısıtıcılar, başlıklar, Ana buhar kanalları ve diğer ekipmanlar, ve petrokimyasal, Nükleer enerji ve gemi inşa alanları.
Özetle, P22 Alaşımlı Çelik Boru, mükemmel yüksek sıcaklık direnci nedeniyle yüksek sıcaklık ve yüksek basınçlı endüstriyel alanda önemli bir malzeme haline gelmiştir., korozyon direnci ve mekanik özellikler.
Inconel için Kaynak İşlem Parametreleri 625 alaşım boruları
Inconel'in Kaynak İşlem Parametreleri 625 Alaşım borusu esas olarak kaynak yöntemini içerir, kaynak hızı, ısı girişi, Dolgu Malzemesi Seçimi, vesaire. Aradığım bilgilere göre özetlenen temel kaynak işlemi parametreleri aşağıdadır.:
- Kaynak yöntemi :
- İnkonel 625 Alaşım borusu çeşitli yöntemlerle kaynaklanabilir, Tungsten inert gaz kaynağı dahil (TIG), metal inert gaz kaynağı (MİG), lazer kaynağı, elektron ışını kaynağı, vesaire.
- Lazer kaynağı, kaynağın boşluğu için uygundur 625 düşük ısı girişi nedeniyle malzemeler, Yüksek hassasiyet ve kontrol edilebilirlik.
- Elektron ışını kaynağı da Inconel için uygundur 625, özellikle yüksek erime noktası metal borularının kaynağında.
- Kaynak hızı :
- Kaynak hızı, spesifik kaynak yöntemine ve malzeme özelliklerine göre ayarlanmalıdır. Örneğin, Lazer Kaynağında, Önerilen kaynak hızı 15 m/sn.
- TIG kaynağında, Aşırı ısınmayı ve çatlamayı önlemek için uygun bir kaynak hızı seçmeniz önerilir.
- Isı Girişi :
- Isı girişini kontrol etmek, Inconel'in kaynak kalitesini sağlamanın anahtarıdır 625. Aşırı ısı girişi, tahıl kabalılmasına neden olabilir, Sıcak çatlama ve performans bozulması.
- Düşük ısı girişinin kullanılması önerilir, Hızlı kaynak yöntemi ve kaynak sonrası stresi hafifletmek için uygun kaynak ısıl işlemi gerçekleştirin.
- Dolgu Malzeme Seçimi :
- Dolgu malzemesi, kaynağın mekanik özelliklerini ve korozyon direncini sağlamak için temel malzeme ile iyi uyumluluğa sahip olmalıdır..
- Yaygın olarak kullanılan dolgu malzemeleri AWS A5.11 ERNICR-3 ve AWS A5.11 ERNICRMO-3'ü içerir, vesaire.
- Diğer Notlar :
- Kaynak yapmadan önce, Yağ gibi safsızlıkları gidermek için yüzey temizlenmelidir, oksit ölçeği, vesaire. Kaynak kalitesini artırmak için.
- Kaynak işlemi sırasında, Yerel aşırı ısınmayı önlemek için düzgün sıcaklık dağılımı korunmalıdır.
- Kaynaktan ve kaynağın mikro yapısını ve özelliklerini iyileştirmek için kaynaktan sonra uygun ısı işlemi yapılabilir..
Özetle, Inconel'in Kaynak İşlem Parametreleri 625 Alaşım borusunun kaynak yönteminin seçimini kapsamlı bir şekilde dikkate alması gerekir, kaynak hızı, Kaynaklı eklemin performansını ve güvenilirliğini sağlamak için ısı girişi ve dolgu malzemesi.
P22 alaşım boruları için kaynak işlemi parametreleri
P22 alaşımlı çelik borunun kaynak işlemi parametreleri aşağıdaki gibidir.:
- Kaynak akımı ve voltajı : Kaynak akımı 160 A ve voltaj aralığı 22 ile 26 V.
- Ön ısıtma sıcaklığı : Ön ısıtma sıcaklığı 170 ~ 190 ℃.
- Kaynak malzemeleri : R407 (E6215-C2M1) Kaynak çubuğu veya ER90S-B3 kaynak teli önerilir.
- Kaynak oluk formu : İşlenmiş V şeklinde 60 ° oluk kullanın ve katmanlar arasında temizlemek için öğütme tekerleği kullanın.
- Kaynak sırası : Kaynak sonrası, Dehidrojenasyon Isıl işlem ve kusur tespiti gerçekleştirilir, STRESS REFORUN.
- Kaynak yöntemi : GTAW arasından seçim yapın (gaz tungsten ark kaynağı), SMAW (korumalı metal ark kaynağı) veya aşk/mig (gaz metal ark kaynağı).
- İşleme sonrası : Kaynaktan sonra artık stresi hafifletmek için yavaş soğutma gereklidir, ve ısı işlemi malzeme kalınlığına ve işleme sonrası spesifikasyonlara göre dikkate alınmalıdır..
Bu parametreler, P22 alaşımlı çelik boru kaynaklı eklemlerin kalitesini sağlar, gerilme mukavemetiyle 515 MPa, ilgili standartların gereksinimlerini karşılayan.
Inconel arasındaki kaynak ortak performansının karşılaştırılması 625 ve p22 alaşımları
Inconel arasında kaynaklı eklemlerin performansında önemli farklılıklar vardır 625 ve p22 alaşımları, esas olarak mekanik özellikler açısından, korozyon direnci ve kaynak işlemi.
- Mekanik özellikler :
- İnkonel 625 Alaşım mükemmel yüksek sıcaklık mukavemeti ve tokluğa sahiptir, 760MPA'dan fazla gerilme mukavemeti ile, Yaklaşık 345MPa'lık bir verim mukavemeti, ve daha fazlasını uzatma 30%. Ek olarak, İnkonel 625 hem oda sıcaklığında hem de yüksek sıcaklıkta mükemmel mekanik özelliklere sahiptir, Özellikle yüksek sıcaklık ortamlarında yüksek mukavemet ve iyi sünekliği korumak.
- P22 alaşımı, yüksek plastisitesi ve iyi düşük sıcaklıklı tokluğu ile bilinir, Ancak gerilme mukavemeti ve akma mukavemeti genellikle inconel'den daha düşüktür 625. P22 Alaşım, Inconel'den daha iyi performans gösterir 625 Düşük sıcaklık ortamlarında, Ancak yüksek sıcaklıklardaki gücü ve ısı direnci zayıf.
- Korozyon direnci :
- İnkonel 625 Alaşım, nikel bazlı bileşimi ve niyobyum ve molibden gibi ek elementler nedeniyle güçlü korozyon direncine sahiptir.. Deniz suyu gibi sert ortamlarda erozyona direnebilir, asidik çözeltiler ve klorürler. Çukurlaşma ve çatlak korozyonuna karşı direnci özellikle olağanüstü.
- P22 alaşımının da iyi korozyon direncine sahip olmasına rağmen, Inconel kadar iyi olmayabilir 625 belirli aşındırıcı ortamlarda (güçlü asit ve yüksek sıcaklık tuz çözeltisi gibi).
- Kaynak performansı :
- İnkonel 625 Alaşım mükemmel kaynak performansına sahiptir ve çeşitli kaynak yöntemleriyle kaynaklanabilir (Tig gibi, MİG, Smaw ve Saw). Kaynak alanının sertliği ve tokluğu yüksektir, ve kaynaktan sonra ısı işlemi olmadan iyi performans korunabilir. Kaynaklı ekleminin gerilme mukavemeti ulaşabilir 811.36 MPa.
- P22 alaşımının kaynak performansı nispeten karmaşıktır, ve ısıdan etkilenen bölgenin Embrittling probleminden kaçınmak için uygun kaynak malzemelerini ve işlemlerini seçmek gerekir. (HAZ). Bazı durumlarda, P22 alaşımının kaynaklı eklemlerinde çatlaklar veya kırılgan kırıklar oluşabilir.
- Uygulama alanları :
- İnkonel 625 Alaşım havacılıkta yaygın olarak kullanılır, kimya endüstrisi, Deniz Mühendisliği ve diğer alanlar, özellikle yüksek sıcaklık ve aşındırıcı ortamlarda.
- P22 Alaşım, düşük sıcaklıklı ortamlarda borular ve ekipmanlar için daha fazla kullanılır, nükleer reaktörler ve kriyojenik depolama tankları gibi.
İnkonel 625 Alaşım, yüksek sıcaklık mukavemetinde p22 alaşımından daha üstündür, korozyon direnci ve kaynak performansı, P22 alaşımı düşük sıcaklık ortamında daha olağanüstü performansa sahipken. Belirli uygulama senaryolarına ve çevre koşullarına göre uygun alaşımların seçilmesinin kapsamlı bir şekilde dikkate alınması gerekir..
Inconel'de yaygın kaynak kusurları 625 ve p22 alaşım boruları
Inconel kaynak işleminde yaygın kusurlar 625 ve P22 alaşım boruları esas olarak aşağıdakileri içerir:
- Termal çatlaklar : Inconel'in en yaygın kusuru 625 Kaynak sırasında termal çatlaklar, bu esas olarak kükürtün karıştırılmasından kaynaklanmaktadır, yol göstermek, fosfor veya düşük eritme noktalı metaller, Yüksek sıcaklıklarda kucaklamaya neden olan taneler arası filmler oluşturmak. Ek olarak, Aşırı kaynak ısı girişi, kaynak ekleminin aşırı ısınmasına ve kaba taneler üretebilir. Tahıl sınırlarındaki düşük eritme noktalı eutectics, düşük mukavemete ve yüksek kırılganlığa sahiptir, ve termal çatlaklara eğilimlidir.
- Stres korozyonu çatlaması (SCC) : İnkonel 625 Kaynaklı eklemler, belirli ortamlarda stres korozyonu çatlamasına eğilimlidir, Özellikle uygun ısıl işlem sonrası (PWHT). Çalışmalar, 650 ℃ × 'da ısı işlem sonrası olduğunu göstermiştir 10 Saatler, kaynaklı eklemlerin SCC direncini önemli ölçüde artırabilir.
- Eleman ayrımı : INCEEL'in kaynağı sırasında eleman ayrımı meydana gelebilir 625, özellikle niyobyumun ayrılma eğilimi daha güçlü bir eğilime sahiptir., molibden ayrılma eğilimi daha zayıf olsa da. Bu ayrım, kaynaklı eklemin eşit olmayan özelliklerine yol açabilir.
- Kırılgan kırılma : İnkonel 625 Kaynaklı eklemler bazı durumlarda kırılgan kırık yaşayabilir, özellikle uygun ısı işlemi olmadan. Örneğin, P92 çeliğinin ve inconel'in tokluğu 625 Yüksek sıcaklıklarda kaynaklı eklemler zayıftır.
- Yüzey kusurları : Gözenekler veya çatlaklar gibi yüzey kusurları, Inconel'in kaynak işlemi sırasında ortaya çıkabilir 625. Bu kusurlar, kaynaklı eklemin genel performansını etkileyebilir.
- Aşırı demir içeriğinin neden olduğu korozyon problemleri : Inconel'in yüzeyini kaynaklarken 625, Aşırı demir içeriği demir okside neden olur (Fe₂o₃) koruyucu krom oksit yerine yüzeyde oluşmak için (Cr₂o₃), böylece korozyon direncini azaltır.
Bu kusurların oluşumunu azaltmak için, Aşağıdaki önlemler önerilir:
- Kaynak işlemi parametrelerini optimize et : Aşırı ısı girişi nedeniyle kaynağın aşırı ısınmasını önlemek için kaynak ısısı girişini kontrol edin.
- Uygun ısı sonrası tedavi : 650 ℃ × gibi 10 Isıtma Sonrası Saatler, kaynaklı eklemin SCC direncini ve tokluğunu önemli ölçüde artırabilir.
- Doğru dolgu malzemesini seçin : Inconel'i kullanmak 625 Dolgu metali kaynak kusurlarının oluşumunu etkili bir şekilde azaltabilir.
- Demir içeriğini kontrol etmek : Demir oksit oluşumunu önlemek ve korozyon direncini iyileştirmek için kaynak sırasında demir içeriğini en aza indirin.
Yukarıdaki önlemlerle, Inconel kaynak işlemindeki ortak kusurlar 625 ve p22 alaşım boruları etkili bir şekilde azaltılabilir, kaynaklı eklemlerin performansını ve güvenilirliğini sağlamak.
Her iki alaşım için anaç sonrası ısı işlem gereksinimleri
İki alaşım için anılan sonrası ısı işlem gereksinimleri aşağıdaki gibidir.:
- GH2132 Alaşım : Kaynak sırasında üretilen kalıntı stresi ortadan kaldırmak için weld sonrası ısıl işlem gereklidir, Kaynak yapısını geliştirin, ve kaynak alanının mekanik özelliklerini ve korozyon direncini geri yükleyin ve geliştirin. Genellikle, Katı Çözelti Tedavisi Gerekir, Katı çözelti sıcaklığı genellikle 980-1020 ℃, tutma süresi 1-2 saat, Ve sonra hızlı soğutma yapılır.
- GH4021 alaşımı : Koşun sonrası ısı işlemi de çok önemlidir. Genellikle, Katı Çözelti Tedavisi Gerekir, 950 ° C'lik katı çözelti sıcaklığı ile, bir tutma süresi 1 saat, Ve sonra hızlı soğutma.
Özet: Hem GH2132 hem de GH4021 alaşımları, kalıntı gerilmeleri ortadan kaldırmak ve kaynak alanının özelliklerini optimize etmek için anaç sonrası ısıl işlem gerektirir.
Inconel Kaynak İçin Önerilen Dolgu Malzemeleri 625 ve p22 alaşımları
Inconel Kaynak İçin Önerilen Dolgu Malzemeleri 625 ve p22 alaşımları aşağıdaki gibidir:
- İnkonel 625 Dolgu Metal : İnkonel 625 Inconel kaynakları için uygun yaygın olarak kullanılan bir nikel-krom-molibden dolgu metalidir 625 Kendisi ve diğer nikel bazlı alaşımlarla farklı metaller (Monel gibi 400, Incoloy 825) ve paslanmaz çelik (örneğin 316, 316L). Kimyasal bileşimi esas olarak 65% nikel, 22% krom, 9% molibden ve 3.5% niyobyum. Mükemmel korozyon direncine ve oksidasyon direncine sahiptir, ve weld sonrası ısı işlemi olmadan yüksek mukavemet ve sünekliği koruyabilir.
- Ernicrmo-3 kaynak teli : Ernicrmo-3, çeşitli nikel bazlı alaşımları kaynaklamak için uygun yaygın olarak kullanılan bir nikel bazlı dolgu metalidir., Inconel dahil 625. Yüksek krom ve yüksek molibden içeriği, çukurlaşma ve çatlak korozyonuna karşı iyi bir direnç sağlar, farklı metal kaynak için uygun hale getirmek.
- ER2209A Kaynak Teli : ER2209A, Inconel Kaynağı için uygun nikel bazlı bir dolgu metalidir 625 ve SAF gibi dubleks paslanmaz çelikler 2205. Çalışmalar, ER2209A kullanılarak iyi bağlanma özelliklerinin elde edilebileceğini göstermiştir, ısı etkilenen bölgesinde tahıl kabuklanması meydana gelebilir (HAZ).
- İnkonel 622 Dolgu Metal : İnkonel 622 Inconel kaynakları için uygun yüksek molibden dolgu metali 625 ve diğer nikel bazlı alaşımlar. Yüksek molibden içeriği korozyon direncini iyileştirir, ancak element ayrım sorunlarına neden olabilir.
- AWS A5.11 Standart Inconel 625 Kaynak çubuğu : AWS A5.11 Standart Inconel 625 Kaynak çubuğu, kaynağı aralık için tercih edilen malzemedir 625, İyi korozyon direnci ve mekanik özelliklerle, Gaz tungsten ark kaynağı ve gaz metal ark kaynağı için uygun.
Özet: Inconel Kaynak İçin 625 ve p22 alaşımları, İnkonel 625 Tercih edilen malzeme olarak dolgu metali veya Ernicrmo-3 kaynak teli önerilir, ve ER2209a veya Inconel 622 Dolgu metali belirli ihtiyaçlara göre seçilebilir. Kaynak işlemi sırasında, Termal stres ve çatlakları önlemek için ısı girişinin ve kaynak parametrelerinin kontrol edilmesine dikkat edilmelidir..
Bu alaşımları kaynaklamak için endüstri standartları (ASME, Aws, vesaire.)
Kaynak nikel bazlı alaşımlar için endüstri standartları esas olarak Amerikan Makine Mühendisleri Derneği'nin ilgili özelliklerini içerir. (ASME) ve Amerikan Kaynak Derneği (Aws).
- ASME Standartları :
- ASME IX, kaynak için yeterlilik standardıdır, lehimleme, ve Kazan ve Basınçlı Kap Kodu'ndaki füzyon kaynak prosedürleri ve nikel bazlı alaşımların kaynağı için geçerlidir.
- ASME B16.11 Tasarımı belirtir, boyutlar, ve nikel bazlı alaşımlardan yapılmış flanşlar ve boru bağlantıları için kaynaklı eklemler için imalat gereksinimleri.
- ASME B36.10, kaynaklı ve kesintisiz haddelenmiş çelik boru için standardı kapsar ve ayrıca nikel bazlı alaşımların boru kaynağı için de geçerlidir..
- AWS Standartları :
- AWS A5.14, nikel bazlı alaşımlar için kaynak malzemelerini ve işlemlerini belirtir (örneğin 625) ve yüksek sıcaklık mukavemeti ve korozyon direnci gereksinimlerine sahip kaynak için uygundur.
- AWS D1.1, çelik yapı kaynağı için standarttır ve nikel bazlı alaşımların kaynağı için de geçerlidir..
- AWS A5.5 ve A5.10, sırasıyla ısıya dayanıklı çelik ve paslanmaz çelik için kaynak malzemelerini ve işlemlerini belirtin. Bu standartlar, nikel bazlı alaşımların kaynağı için de geçerlidir..
- Diğer ilgili standartlar :
- ISO 13856-1 ve ISO 13856-2 Nikel bazlı alaşımlar için kaynak malzemeleri ve işlemleri belirtin, sırasıyla, ve AWS ve ASME standartlarına eşdeğerdir.
- İÇİNDE 14380-1 Ve ve 14380-2 Ayrıca benzer kaynak malzemesi ve süreç gereksinimleri sağlar.
Özetle, Nikel bazlı alaşımları kaynak yaparken, ASME IX gibi standartlar, AWS A5.14, ve AWS D1.1, kaynak kalitesini ve endüstri spesifikasyonlarına uyum sağlamak için atıfta bulunulmalıdır..
Her iki alaşım için kaynak uygulamalarının vaka çalışmaları
İki alaşımın kaynak uygulaması hakkında bir vaka çalışması aşağıdaki gibidir.:
- Alaşım 32 Hassas alaşım
Alaşım uygulaması 32 Kaynak alanındaki hassas alaşım esas olarak lazer kaynağı üzerinde yoğunlaşmıştır., lehimleme ve sürtünme kaynağı. Lazer kaynak teknolojisi, alaşımın kaynağında yaygın olarak kullanılmaktadır 32 Yüksek hassasiyeti ve verimliliği nedeniyle, ve derin penetrasyon ve yüksek kaliteli kaynak efektleri elde edebilir. - CUNI34 Korozyona Dayanıklı Bakır Nikel Alaşım
CUNI34 Alaşım, havacılık alanında yüksek sıcaklıklarda iletken parçalar ve konektörler üretmek için yaygın olarak kullanılmaktadır.. Fakat, Kaynak sırasında termal çatlaklar üretmek kolaydır, ve kaynaklı eklemin korozyon direnci etkilenebilir. Öyleyse, Pratik uygulamalarda, Kaynak kalitesini sağlamak için uygun işlem parametreleri ve kaynak malzemeleri benimsenmelidir. - 800H nikel-demir krom alaşımı
800H Nikel-demir-krom alaşımı iyi kaynak uyarlanabilirliğine sahiptir ve manuel ark kaynağı gibi çeşitli kaynak yöntemleri aracılığıyla yüksek kaliteli kaynak efektleri elde edebilir (SMAW), TIG kaynağı (argon ark kaynağı) ve MIG kaynağı (gaz korumalı kaynak). Özellikle paslanmaz çelik kaynağında, 800H Mükemmel Performans Gösteriyor. - Titanyum alaşımı
Titanyum alaşım kaynak teknolojileri, lazer kaynağı ve elektron ışını kaynağı gibi gelişmiş yöntemleri içerir. Bu teknolojiler çatlaklar gibi sorunları etkili bir şekilde çözebilir, Titanyum alaşım kaynağı sırasında ortaya çıkabilecek gözenekler ve deformasyon, Kaynak kalitesinin ve güvenilirliğin sağlanması. - Niobium tungsten alaşımı
Lazer Kaynak Teknolojisi, niyobyum tungsten alaşımının kaynağında önemli avantajlar göstermektedir. İş verimliliğini artırabilir ve güzel kaynak görünümünü sağlayabilir, küçük kaynak, Büyük kaynak derinliği ve yüksek kaynak kalitesi. - Nikel-krom alaşımı
Lazer Kaynak Teknolojisi, yüksek hassasiyetin özelliklerine sahiptir, Nikel-krom alaşımlarının kaynağında yüksek verimlilik ve esneklik, ve verimli ve doğru kaynak etkileri elde edebilir. - X1nicrmocun25-20-7 nikel bazlı alaşım
X1nicrmocun25-20-7 Nikel bazlı alaşım, kaynak sırasında termal çatlaklar ve gözenekler gibi zorluklar. Kaynaklı derzlerin kalitesi, kaynak işlemini optimize ederek etkili bir şekilde geliştirilebilir, ısı girişi, Koruyucu Gaz ve Kazanma Sonrası Tedavi.