Welding Technology Analysis of Inconel 625 and P22 Alloy Steel Pipes
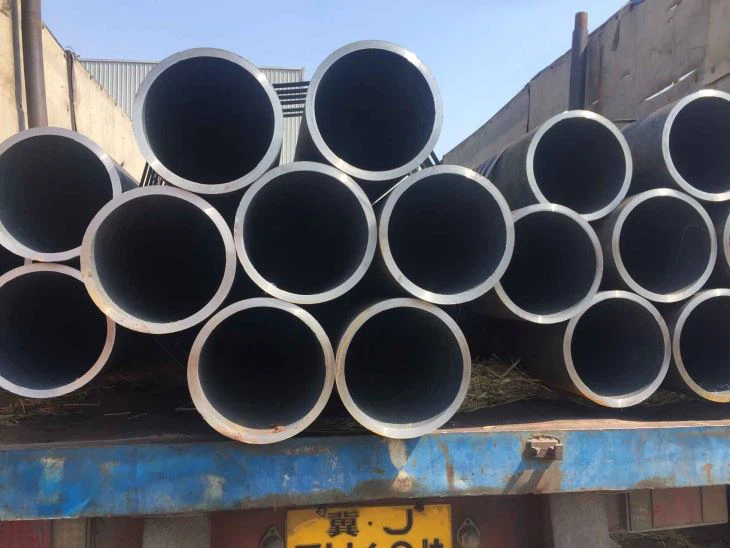
Welding Technology Analysis of Inconel 625 and P22 Alloy Steel Pipes
1. Introduction
The welding of dissimilar materials, such as nickel-based superalloys (e.g., Inconel 625) and low-alloy steels (e.g., P22), presents significant challenges due to their distinct metallurgical and mechanical properties. This analysis comprehensively examines the welding techniques, process parameters, common defects, and post-weld treatments for these materials, supported by industry standards and experimental case studies.
Inconel 625 alloy pipe chemical composition and mechanical properties
The chemical composition and mechanical properties of Inconel 625 alloy pipe are as follows:
2. Material Characteristics
2.1 Inconel 625 Alloy
Chemical Composition ():
Element | Ni | Cr | Mo | Fe | Nb+Ta | C | Mn | Si |
---|---|---|---|---|---|---|---|---|
% | ≥58 | 20–23 | 8–10 | ≤5 | 3.15–4.15 | ≤0.10 | ≤0.50 | ≤0.50 |
Mechanical Properties ():
- Tensile Strength: 827 MPa (min)
- Yield Strength (0.2% offset): 414 MPa (min)
- Elongation: 35% (min)
- Hardness: ≤287 HB (annealed condition)
- Melting Point: 1,290–1,350°C
Inconel 625 exhibits exceptional oxidation resistance up to 980°C and corrosion resistance in chloride-rich environments due to its high Cr and Mo content .
2.2 P22 Alloy Steel
Chemical Composition ():
Element | C | Cr | Mo | Mn | Si | Fe |
---|---|---|---|---|---|---|
% | 0.05–0.15 | 1.90–2.60 | 0.87–1.13 | 0.30–0.61 | ≤0.50 | Bal. |
Mechanical Properties ():
- Tensile Strength: ≥415 MPa
- Yield Strength: ≥205 MPa
- Elongation: ≥30%
- Hardness: 180–240 HB (after heat treatment)
P22 is a Cr-Mo steel optimized for high-temperature service (up to 550–600°C), with good weldability and creep resistance
3. Welding Challenges for Dissimilar Joints
3.1 Metallurgical Incompatibilities
- Coefficient of Thermal Expansion (CTE) Mismatch:
Inconel 625 (14.7 µm/m°C) vs. P22 (12.3 µm/m°C) generates residual stresses during cooling . - Carbon Migration:
Diffusion of carbon from P22 to Inconel 625 forms brittle carbides (e.g., Cr23C6) at the fusion boundary, reducing toughness . - Dilution Effects:
High Fe content in the weld pool (from P22) degrades the corrosion resistance of Inconel 625 .
3.2 Thermal Gradient Management
- Heat Input Control:
Excessive heat input in Inconel 625 causes grain coarsening, while insufficient preheating for P22 increases hydrogen cracking risk .
4. Welding Processes and Parameters
4.1 Recommended Welding Methods
Material Pair | Preferred Methods | Key Considerations |
---|---|---|
Inconel 625–Inconel 625 | TIG (GTAW), Laser Welding | Low heat input, autogenous welding |
P22–P22 | SMAW, GTAW | Preheat (170–190°C), post-weld stress relief |
Inconel 625–P22 | TIG with Ni-based filler | Buffer layers, controlled dilution |
4.2 Process Parameters for Dissimilar Welding
Case Study: Inconel 625 to P22 using ERNiCrMo-3 filler ():
- Preheating: 150–200°C (P22 side only) to minimize thermal stress.
- Interpass Temperature: ≤150°C (prevents excessive grain growth in Inconel 625).
- Heat Input: 0.8–1.2 kJ/mm (TIG), 1.5–2.0 kJ/mm (SMAW).
- Shielding Gas: Argon + 2–5% H2 for TIG welding to reduce oxidation.
Electron Beam Welding (EBW):
Used for CuCrZr/Inconel 625 joints in vacuum applications, achieving a narrow HAZ and minimal distortion .
5. Filler Material Selection
5.1 Inconel 625 Welding
- Matching Filler: ERNiCrMo-3 (AWS A5.14) ensures corrosion resistance and mechanical parity .
- Dissimilar Welds: INCONEL Filler Metal 625 (ERNiCrMo-10) for joining to stainless steels or P22, mitigating carbon migration .
5.2 P22 Welding
- Matching Filler: E9018-B3 (SMAW) or ER90S-B3 (GTAW) for Cr-Mo steel compatibility .
6. Common Welding Defects and Mitigation
6.1 Inconel 625
- Hot Cracking: Caused by S/P impurities; mitigated using high-purity fillers and low heat input .
- Porosity: Avoid moisture contamination in shielding gas (dew point ≤ -50°C) .
6.2 P22
- Hydrogen-Induced Cracking: Controlled via preheating, low-hydrogen electrodes, and post-weld dehydrogenation at 300–350°C .
6.3 Dissimilar Joints
- Brittle Intermetallic Phases: Use Ni-based buffers (e.g., ERNiCrMo-3) to absorb Fe dilution .
7. Post-Weld Heat Treatment (PWHT)
Material | PWHT Parameters | Purpose |
---|---|---|
Inconel 625 | Solution annealing: 980–1,020°C, rapid cooling | Restore corrosion resistance |
P22 | Stress relief: 650–700°C, 1–2 hours | Reduce residual stresses |
Inconel 625–P22 | Avoid annealing P22 above 750°C (prevents carbide coarsening) | Balance stress and microstructure |
Study Result: PWHT at 650°C for 10 hours improved SSCC resistance in F22/Inconel 625 joints by 40% .
8. Industry Standards and Compliance
- ASME BPVC Section IX: Qualifies welding procedures and personnel for boiler/pressure vessel applications .
- AWS D10.18: Guides welding of Ni-Cr-Mo alloys in corrosive environments.
- ASTM B444: Specifies Inconel 625 pipe manufacturing and testing .
9. Case Studies
9.1 Nuclear Reactor Piping (Inconel 625–P22)
- Application: Steam generator tubing in pressurized water reactors.
- Welding Method: Narrow-gap TIG with ERNiCrMo-3 filler.
- Outcome: No cracks or corrosion after 10,000 service hours .
9.2 Petrochemical Pipeline (P22–P22)
- Application: High-temperature gas transmission.
- Welding Method: SMAW with E9018-B3, post-weld stress relief at 680°C.
- Outcome: Compliance with API 1104 standards; no hydrogen cracks detected .
10. Future Trends
- Laser Hybrid Welding: Combines laser and GMAW for higher speed and precision in Inconel 625 .
- Additive Manufacturing: Wire-arc AM for repairing Inconel 625 components with minimal HAZ .
Mechanical properties
Inconel 625 alloy pipe has excellent mechanical properties, as follows:
- Tensile strength : ≥120 MPa (annealed state).
- Yield strength : ≥827 MPa (annealed state).
- Elongation : ≥60% (annealed state).
- Hardness : HB ≤ 287 (annealed state).
- High temperature performance : Maintains high strength and oxidation resistance in high temperature environments, with a maximum operating temperature of up to 2000°F (about 1093°C).
- Corrosion resistance : Highly resistant to pitting and crevice corrosion in oxidizing acid, reducing acid and chloride environments.
Features
- Corrosion resistance : Inconel 625 has excellent resistance to a variety of corrosive media, including nitric acid, sulfuric acid, phosphoric acid and hydrochloric acid.
- High temperature stability : It can maintain good mechanical properties and oxidation resistance at high temperatures.
- Processing performance : It has good weldability and machinability, and is suitable for manufacturing parts of various complex shapes.
In summary, Inconel 625 alloy pipes are widely used in chemical, marine, nuclear energy and other fields due to their excellent corrosion resistance, high temperature stability and mechanical properties.
P22 alloy pipe chemical composition and mechanical properties
The chemical composition and mechanical properties of P22 alloy steel pipe are as follows:
Chemical composition
The main chemical components of P22 alloy steel pipe include chromium (Cr), molybdenum (Mo), carbon (C), silicon (Si), manganese (Mn), phosphorus (P) and sulfur (S). Among them, chromium and molybdenum are the main alloying elements, with chromium content of 2.25% and molybdenum content of 0.87-1.37%. In addition, the carbon content is usually less than 0.05%, the silicon content does not exceed 0.50%, the manganese content does not exceed 0.60%, and the phosphorus and sulfur contents do not exceed 0.025%.
Mechanical properties
- Yield strength : typically 205 MPa.
- Tensile strength : typically 415 MPa.
- Elongation : Usually 30%.
- Hardness : After heat treatment, the hardness can reach 180 HB.
- Creep performance : It has excellent creep resistance at high temperatures, especially at 550℃/50 MPa, the creep rupture life exceeds 100,000 hours.
- Anti-oxidation performance : It has good anti-oxidation performance at 600℃, and the oxidation rate is ≤0.1 mm/year.
Application areas
P22 alloy steel pipes are widely used in high temperature and high pressure environments, such as power station boiler superheaters, reheaters, headers, main steam ducts and other equipment, as well as petrochemical, nuclear power and shipbuilding fields.
In summary, P22 alloy steel pipe has become an important material in the high temperature and high pressure industrial field due to its excellent high temperature resistance, corrosion resistance and mechanical properties.
Welding process parameters for Inconel 625 alloy pipes
The welding process parameters of Inconel 625 alloy pipe mainly include welding method, welding speed, heat input, filler material selection, etc. The following are the key welding process parameters summarized based on the information I searched:
- Welding method :
- Inconel 625 alloy pipe can be welded by a variety of methods, including tungsten inert gas welding (TIG), metal inert gas welding (MIG), laser welding, electron beam welding, etc.
- Laser welding is suitable for welding Inconel 625 materials due to its low heat input, high precision and controllability.
- Electron beam welding is also suitable for Inconel 625, especially in the welding of high melting point metal pipes.
- Welding speed :
- The welding speed should be adjusted according to the specific welding method and material properties. For example, in laser welding, the recommended welding speed is 15 m/s.
- In TIG welding, it is recommended to select an appropriate welding speed to avoid overheating and cracking.
- Heat Input :
- Controlling heat input is the key to ensuring the welding quality of Inconel 625. Excessive heat input may cause grain coarsening, hot cracking and performance degradation.
- It is recommended to use low heat input, fast welding method and carry out appropriate post weld heat treatment to relieve stress after welding.
- Filling material selection :
- The filler material should have good compatibility with the base material to ensure the mechanical properties and corrosion resistance of the weld.
- Commonly used filling materials include AWS A5.11 ERNiCr-3 and AWS A5.11 ERNiCrMo-3, etc.
- Other notes :
- Before welding, the surface should be cleaned to remove impurities such as oil, oxide scale, etc. to improve the welding quality.
- During the welding process, uniform temperature distribution should be maintained to avoid local overheating.
- Appropriate heat treatment can be carried out after welding to improve the microstructure and properties of the weld.
In summary, the welding process parameters of Inconel 625 alloy pipe need to comprehensively consider the selection of welding method, welding speed, heat input and filler material to ensure the performance and reliability of the welded joint.
Welding process parameters for P22 alloy pipes
The welding process parameters of P22 alloy steel pipe are as follows:
- Welding current and voltage : The welding current is 160 A and the voltage range is 22 to 26 V.
- Preheating temperature : The preheating temperature is 170~190℃.
- Welding materials : R407 (E6215-C2M1) welding rod or ER90S-B3 welding wire is recommended.
- Welding groove form : Use machined V-shaped 60° groove and use grinding wheel to clean between layers.
- Welding sequence : After welding, dehydrogenation heat treatment and flaw detection are carried out, followed by stress relief heat treatment.
- Welding method : Choose from GTAW (gas tungsten arc welding), SMAW (shielded metal arc welding) or GMAW/MIG (gas metal arc welding).
- Post-processing : Slow cooling is required after welding to relieve residual stress, and heat treatment should be considered based on material thickness and post-processing specifications.
These parameters ensure the quality of P22 alloy steel pipe welded joints, with a tensile strength of 515 MPa, which meets the requirements of relevant standards.
Comparison of weld joint performance between Inconel 625 and P22 alloys
There are significant differences in the performance of welded joints between Inconel 625 and P22 alloys, mainly in terms of mechanical properties, corrosion resistance and welding process.
- Mechanical properties :
- Inconel 625 alloy has excellent high temperature strength and toughness, with a tensile strength of more than 760MPa, a yield strength of about 345MPa, and an elongation of more than 30%. In addition, Inconel 625 has excellent mechanical properties at both room temperature and high temperature, especially maintaining high strength and good ductility in high temperature environments.
- P22 alloy is known for its high plasticity and good low-temperature toughness, but its tensile strength and yield strength are generally lower than Inconel 625. P22 alloy performs better than Inconel 625 in low-temperature environments, but its strength and heat resistance at high temperatures are poor.
- Corrosion resistance :
- Inconel 625 alloy has strong corrosion resistance due to its nickel-based composition and added elements such as niobium and molybdenum. It can resist erosion in harsh environments such as seawater, acidic solutions and chlorides. Its resistance to pitting and crevice corrosion is particularly outstanding.
- Although P22 alloy also has good corrosion resistance, it may not be as good as Inconel 625 in certain specific corrosive environments (such as strong acid and high temperature salt solution).
- Welding performance :
- Inconel 625 alloy has excellent welding performance and can be welded by a variety of welding methods (such as TIG, MIG, SMAW and SAW). The hardness and toughness of the weld area are high, and good performance can be maintained without heat treatment after welding. The tensile strength of its welded joint can reach 811.36 MPa.
- The welding performance of P22 alloy is relatively complex, and it is necessary to select appropriate welding materials and processes to avoid the embrittlement problem of the heat affected zone (HAZ). In some cases, cracks or brittle fractures may occur in the welded joints of P22 alloy.
- Application areas :
- Inconel 625 alloy is widely used in aerospace, chemical industry, marine engineering and other fields, especially in high temperature and corrosive environments.
- P22 alloy is more used for pipes and equipment in low-temperature environments, such as nuclear reactors and cryogenic storage tanks.
Inconel 625 alloy is superior to P22 alloy in high temperature strength, corrosion resistance and welding performance, while P22 alloy has more outstanding performance in low temperature environment. The selection of suitable alloys needs to be comprehensively considered according to specific application scenarios and environmental conditions.
Common welding defects in Inconel 625 and P22 alloy pipes
Common defects in the welding process of Inconel 625 and P22 alloy pipes mainly include the following:
- Thermal cracks : The most common defect of Inconel 625 during welding is thermal cracks, which is mainly due to the mixing of sulfur, lead, phosphorus or low-melting-point metals, forming intergranular films that cause embrittlement at high temperatures. In addition, excessive welding heat input can also cause overheating of the weld joint and produce coarse grains. The low-melting-point eutectics on the grain boundaries have low strength and high brittleness, and are prone to thermal cracks.
- Stress corrosion cracking (SCC) : Inconel 625 welded joints are prone to stress corrosion cracking in certain environments, especially without proper post heat treatment (PWHT). Studies have shown that post heat treatment at 650℃ × 10 hours can significantly improve the SCC resistance of welded joints.
- Element segregation : Element segregation may occur during the welding of Inconel 625, especially niobium has a stronger tendency to separate, while molybdenum has a weaker tendency to separate. This segregation may lead to uneven properties of the welded joint.
- Brittle fracture : Inconel 625 welded joints may experience brittle fracture in some cases, especially without proper heat treatment. For example, the toughness of P92 steel and Inconel 625 welded joints at high temperatures is poor.
- Surface defects : Surface defects such as pores or cracks may occur during the welding process of Inconel 625. These defects may affect the overall performance of the welded joint.
- Corrosion problems caused by excessive iron content : When welding the surface of Inconel 625, excessive iron content will cause iron oxide (Fe₂O₃) to form on the surface instead of protective chromium oxide (Cr₂O₃), thereby reducing corrosion resistance.
To reduce the occurrence of these defects, the following measures are recommended:
- Optimize welding process parameters : control welding heat input to avoid overheating of the weld due to excessive heat input.
- Appropriate post-heat treatment : such as 650℃ × 10 hours of post-heat treatment, can significantly improve the SCC resistance and toughness of the welded joint.
- Choose the right filler material : Using Inconel 625 as filler metal can effectively reduce the occurrence of welding defects.
- Controlling Iron Content : Minimize the iron content during welding to avoid the formation of iron oxides and improve corrosion resistance.
Through the above measures, the common defects in the welding process of Inconel 625 and P22 alloy pipes can be effectively reduced, ensuring the performance and reliability of the welded joints.
Post-weld heat treatment requirements for both alloys
The post-weld heat treatment requirements for the two alloys are as follows:
- GH2132 alloy : Post-weld heat treatment is essential to eliminate the residual stress generated during welding, improve the weld structure, and restore and improve the mechanical properties and corrosion resistance of the weld area. Usually, solid solution treatment is required, the solid solution temperature is generally 980-1020℃, the holding time is 1-2 hours, and then rapid cooling is performed.
- GH4021 alloy : Post-weld heat treatment is also very important. Usually, solid solution treatment is required, with a solid solution temperature of 950°C, a holding time of 1 hour, and then rapid cooling.
Summary: Both GH2132 and GH4021 alloys require post-weld heat treatment to eliminate residual stresses and optimize the properties of the weld area.
Recommended filler materials for welding Inconel 625 and P22 alloys
Recommended filler materials for welding Inconel 625 and P22 alloys are as follows:
- Inconel 625 filler metal : Inconel 625 is a widely used nickel-chromium-molybdenum filler metal suitable for welding Inconel 625 itself and dissimilar metals with other nickel-based alloys (such as Monel 400, Incoloy 825) and stainless steel (such as 316, 316L). Its chemical composition mainly includes 65% nickel, 22% chromium, 9% molybdenum and 3.5% niobium. It has excellent corrosion resistance and oxidation resistance, and can maintain high strength and ductility without post-weld heat treatment.
- ERNiCrMo-3 welding wire : ERNiCrMo-3 is a commonly used nickel-based filler metal suitable for welding a variety of nickel-based alloys, including Inconel 625. Its high chromium and high molybdenum content gives it good resistance to pitting and crevice corrosion, making it suitable for dissimilar metal welding.
- ER2209a welding wire : ER2209a is a nickel-based filler metal suitable for welding Inconel 625 and duplex stainless steels such as SAF 2205. Studies have shown that good bonding properties can be achieved using ER2209a, although grain coarsening may occur in its heat affected zone (HAZ).
- Inconel 622 Filler Metal : Inconel 622 is a high molybdenum filler metal suitable for welding Inconel 625 and other nickel-based alloys. Its high molybdenum content improves corrosion resistance but may cause element segregation problems.
- AWS A5.11 Standard Inconel 625 Welding Rod : AWS A5.11 standard Inconel 625 welding rod is the preferred material for welding Inconel 625, with good corrosion resistance and mechanical properties, suitable for gas tungsten arc welding and gas metal arc welding.
Summary: For welding Inconel 625 and P22 alloys, Inconel 625 filler metal or ERNiCrMo-3 welding wire is recommended as the preferred material, and ER2209a or Inconel 622 filler metal can be selected according to specific needs. During the welding process, attention should be paid to controlling the heat input and welding parameters to avoid thermal stress and cracks.
Industry standards for welding these alloys (ASME, AWS, etc.)
The industry standards for welding nickel-based alloys mainly include the relevant specifications of the American Society of Mechanical Engineers (ASME) and the American Welding Society (AWS).
- ASME Standards :
- ASME IX is the qualification standard for welding, brazing, and fusion welding procedures in the Boiler and Pressure Vessel Code and applies to the welding of nickel-base alloys.
- ASME B16.11 specifies the design, dimensions, and fabrication requirements for welded joints for flanges and pipe connections made of nickel-based alloys.
- ASME B36.10 covers the standard for welded and seamless rolled steel pipe and is also applicable to pipe welding of nickel-base alloys.
- AWS Standards :
- AWS A5.14 specifies welding materials and processes for nickel-based alloys (such as 625) and is suitable for welding with high temperature strength and corrosion resistance requirements.
- AWS D1.1 is the standard for steel structure welding and is also applicable to the welding of nickel-based alloys.
- AWS A5.5 and A5.10 specify welding materials and processes for heat-resistant steel and stainless steel respectively. These standards are also applicable to the welding of nickel-based alloys.
- Other relevant standards :
- ISO 13856-1 and ISO 13856-2 specify welding materials and processes for nickel-based alloys, respectively, and are equivalent to AWS and ASME standards.
- EN 14380-1 and EN 14380-2 also provide similar welding material and process requirements.
In summary, when welding nickel-based alloys, standards such as ASME IX, AWS A5.14, and AWS D1.1 should be referred to to ensure welding quality and compliance with industry specifications.
Case studies of welding applications for both alloys
A case study on the welding application of the two alloys is as follows:
- Alloy 32 Precision Alloy
The application of Alloy 32 precision alloy in the field of welding is mainly concentrated on laser welding, brazing and friction welding. Laser welding technology has been widely used in the welding of Alloy 32 due to its high precision and efficiency, and can achieve deep penetration and high-quality welding effects. - CuNi34 corrosion resistant copper nickel alloy
CuNi34 alloy is widely used in the aerospace field to manufacture conductive parts and connectors at high temperatures. However, it is easy to produce thermal cracks during welding, and the corrosion resistance of the welded joint may be affected. Therefore, in practical applications, appropriate process parameters and welding materials need to be adopted to ensure welding quality. - 800H Nickel-Iron-Chromium Alloy
800H nickel-iron-chromium alloy has good welding adaptability and can achieve high-quality welding effects through a variety of welding methods such as manual arc welding (SMAW), TIG welding (argon arc welding) and MIG welding (gas shielded welding). Especially in stainless steel welding, 800H shows excellent performance. - Titanium Alloy
Titanium alloy welding technologies include advanced methods such as laser welding and electron beam welding. These technologies can effectively solve problems such as cracks, pores and deformation that may occur during titanium alloy welding, ensuring welding quality and reliability. - Niobium Tungsten Alloy
Laser welding technology shows significant advantages in the welding of niobium tungsten alloy. It can improve work efficiency and ensure beautiful weld appearance, small weld, large welding depth and high welding quality. - Nickel-chromium alloy
Laser welding technology has the characteristics of high precision, high efficiency and flexibility in the welding of nickel-chromium alloys, and can achieve efficient and accurate welding effects. - X1NiCrMoCuN25-20-7 nickel-based alloy
X1NiCrMoCuN25-20-7 nickel-based alloy faces challenges such as thermal cracks and pores during welding. The quality of welded joints can be effectively improved by optimizing welding process, heat input, shielding gas and post-weld treatment.